Simple ideas make a New Holland TF combine better
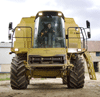
Want to see the pictures bigger? Visit the gallery
Adapting and improving his combine has allowed a Warwickshire farm manager to squeeze every ounce of performance out of it, as he told David Cousins
Richard Ward, it has to be said, is a bit of a fan of second-hand New Holland TF combines. Now running a TF78 (which replaced a TF44 and before that a TF42), he likes their zippy forward speed, their excellent straw-chopping abilities and their reliability.
But that hasn’t stopped him making all sorts of modifications to it over the years to ensure the most important arable task of the year gets done smoothly and quickly.
The TF combine is a half conventional, half rotary machine. Everything from the drum to the rotary separator is conventional, but instead of straw walkers it has a double-width twin flow rotor that divides the straw in two, then spins it to get all the remaining grain out by centrifugal force.
It was eight years old when he bought it three years ago and cost ÂŁ32,000. “It was 20-25% cheaper than a conventional TX combine of the same age because of the myth that it leaves the straw very mangled,” he says. “It is slightly more mangled but it makes for higher density bales which we like.”
The standard header is 7.3m (24ft) with 9.1m (30ft) as an option, but Mr Ward chose this machine because of it carries the rarer 6m (20ft) version. His small field size and narrow gateways made this the practical option and its good forward speeds (typically 7.5kph in wheat) still allow more-than-respectable throughputs of 35t/hour. On the 550ha (1250-acre) farm he manages for Barton Farms Ltd at Barton-on-the Heath, near Moreton-in-Marsh, there are 320ha (800 acres) of combinable crops plus another 120ha (300 acres) that he cuts for another farmer.
So what changes has he made to the TF78?
(1) TFs normally leave a pyramid-shaped swath, 0.9m (3ft) wide and as much as 0.6m (2ft 6in) high. That means bales tend to be over-dense on the inside and too loose on the outside, plus the tractor drawbar bulldozes the straw badly.
The answer came from local contractor Tim Ingles. He designed a v-shaped baffle that attaches to the inside of the rear hood, just where the two streams of straw are thrown back together at the rear end. This redistributes the straw into a much more manageable shape.
“The resulting, almost double-rowed, swath is now 5ft wide and the height is less than half what it was,” he says. “The baler can go up to two-and-a-half times faster and there’s no need for it to weave from side to side to achieve an even bale.”
(2) Oil seeping through the filler cap on the top of the Iveco engine proved more than just a nuisance. It gathers dust, chaff and barley awns and, just 5in from the exposed turbocharger, presented an obvious fire hazard.
Which is exactly what it proved to be in the hot harvest of 2006. Smouldering awns were blown on to ground when Mr Ward revved up the engine and set light to the stubble. “Luckily I got the combine out of the way,” he says, “but the field caught light and it was a four-fire-engine job to put it out.”
The answer was to fit a 50mm (2in) diameter piece of galvanized water pipe on top of the filler cap with a proper bung that stops any oil seepage. A word of warning, though because this also prevents gas escaping, it is vitally important to keep the bottom breather vent pipe free from blockages to prevent back pressure in the engine. Check it every day, he says.
(3) Last year’s wet harvest sorely tested the patience and ingenuity of farmers across central and western parts of the country. With 140mm (5.5in) of rain falling on 20 July, Mr Ward knew he was going to have problems with boggy ground.
Not to be knocked off course, he fitted a pair Steiger tractor wheels (with 2in less diameter than the existing ones) as duals on the front of the combine. They helped a lot, but fitting and removing each took two hours and the steps to the cab had to be altered to accommodate the extra width.
Wider rear wheels were also tried. A set of bigger-diameter but slightly narrower ex-sprayer wheels were no good. “They just acted as anchors,” he says. A pair of ultra-wide 48x25x20 LGP tyres worked much better, so much so that he reckons they were much more effective in keeping the combine afloat, than the front dual wheels.
(4) Mr Ward is convinced that leaving the lifters on for all crops other than beans makes the best sense. But when they do have to be removed, why leave them lying around in a corner of the workshop when you could slot them neatly on an on-board rack like this homemade addition?
(5) The TF78 has a 150mm (60in) intake, but the flights on the table auger are arranged in a way that, somewhat illogically, narrows the incoming swath to several inches less than that. That means that the edges of the drum, beater and rotary separator are not doing their fair share of work.
The solution, which came from joint head-scratching by Mr Ward and local combine service engineer Will Slatter, was to grind about 75mm (3in) width off the end of the flight to widen the crop flow and boost throughput. Wider headers may have bolt-on sections that can be more simply removed.
(6) Baffled by combine manufacturers’ habit of wiring the worklights so that you can’t put them all on at once? Mr Ward simply used spade connectors and wire to bridge the positive terminals of both the “on” and “off” bulbs on both sides of the cab.
There is more load when they are all on, so they are slightly dimmer than before, but it has never blown a fuse, he says. He also fixed a spotlight to the end of the discharge auger (which illuminates the trailer alongside far better than the existing one on the side of the tank) and wired it into the latter’s circuit.
(7) Two throw-out beaters (one on each side of the combine) propel straw from the TF rotor into either the chopper intakes or the doors that rejoin the two swathes into one. This system works fine, but in damper evening conditions the straw can quickly bridge (especially if you are not chopping), blocking the beater, then within seconds bunging up the rest of the threshing mechanism and ultimately necessitating a four-hour unblocking exercise.
His solution? Two flap-activated switches, identical to those fitted above the back of the straw walkers, but fixed behind each of the throw-out beaters (and wired to the horn terminal on the steering column).
These sense when straw is building up and sound the horn. “The system also acts as a good warning device,” says Mr Ward. “When straw starts to become damp, the horn will start to pulse. Slow down forward speed and it stops sounding, so you know you can keep combining.”
(8) Here’s a nice simple combining system. With 80ft tramlines and a 20ft header, Mr Ward starts with the left-hand divider in the left-hand track of a tramline, then turns back on himself for the next bout.
He then moves to the next tramline and does the mirror image. That means no half-width strips to reduce workrate and never having to put the wider left-hand divider into the crop. Better still, turn-round time is minimal.
(9) Constant cleaning of the cab glass is an annoying harvest time-waster.
Mr Ward says he has heard of farmers who have fitted a fan to suck dusty air away from the topside of the straw elevator housing, alleviating that waft of dust that heads straight at you. Anyone out there cracked this problem?
If you have a machine (whether it’s a tractor, combine, baler or whatever) you have adapted and improved to get the best out of it, let us know. Email david.cousins@rbi.co.uk. Equally, if you want to find out more about Richard Ward’s ideas and adaptations, contact him on Richard Ward richardward@homefarm59.fsnet.co.uk
Want to see the pictures bigger? Visit the gallery.