Controlled traffic farming helps cut autumn establishment costs
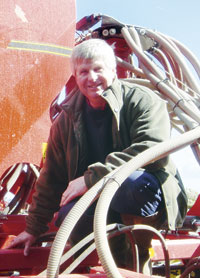
Growers who doubt whether grain prices will see much improvement are looking to more radical crop establishment techniques to drive down costs – including direct seeding and controlled traffic operations. Peter Hill takes a look
It may still be a step too far for some and an approach not suited to the rotation for others. But more growers are looking to some form of “controlled traffic” system to improve crop yields and drive down costs.
At Walkington in East Yorkshire, Neal Evison is one such grower. He has replaced the plough and power harrow for a non-inversion establishment system and ditched his minimum tillage disc drill for a tined machine that operates with little or no pre-sowing preparation.
The new drill – a 6m wide Vaderstad Seed Hawk – will be used to establish spring and winter cereals and oilseed rape on 550ha of owned, contracted and tenanted land around Samples Farm. The drill is a core component of Mr Evison’s planned switch to controlled traffic field operations.
“We don’t see the average price of wheat going much over £100/t in future so in order to improve gross margins, we have to reduce costs and become more efficient,” he says. “Although yields may dip at first, I think we’ll eventually see a yield increase of around 8% – but more significantly a potential reduction of 25% in crop input costs.”
Controlled traffic principles also fit well with environmental protocols, he suggests, in that the technique aims to reduce the trafficked area in fields and, thereby, minimise soil compaction. Soil structure should improve naturally, with less remedial action needed to put right the effects of running farm machinery across it.
“By travelling less and using the same wheelings as far as possible, we hope to reduce fuel costs and general wear and tear,” Mr Evison adds. “Seed and fertiliser costs could also be cut, as well as the labour needed for a more streamlined approach to crop establishment.”
Starting off
The starting point for setting up the controlled traffic system is the farm’s combine, which has the widest track setting and runs with a 7.5m cutting table.
It sits on 900mm wide tyres, but some flotation will be sacrificed when they are replaced by 800mm tyres to reduce the trafficked area. All other machinery will have to fit these dimensions and use the same wheelings as far as possible.
Historically, Mr Evison has started autumn and spring cultivations by ploughing, with a power harrow then working down the land before drilling.
Now, a Spaldings Flatlift soil loosener is often the only cultivator used – to remove any compaction from previous cultivations or harvesting operations. A Carrier disc and packer implement is drafted in if necessary to create a shallow stale seed-bed for weed control.
Two vital components for an effective no-tillage controlled traffic system are a consistently accurate GPS steering system and a seed drill capable of working direct into stubbles while coping with a lot of trash and debris.
“A high-definition RTK system is critical for the GPS because you need repeatability in policing the wheelings every year to within 2cm accuracy,” says Mr Evison, who opted for a TopCon system. “And because we’re chopping and spreading the straw rather than baling it, we must use a drill that allows straw to run freely between the tines rather than bulldozing it.”
The Vaderstad Seed Hawk, with its purpose-designed separate knife coulters for fertiliser and seed, performs well in that respect, it seems.
“There are no discs to cause ‘hair pinning’ of straw into the seed slot and the toxic conditions that can result as the material breaks down,” Mr Evison points out. “Also, the 75cm spacing allows straw and trash to pass freely between the tines. The 4m Rapid we used previously is an excellent drill, but the Seed Hawk, although it’s not perfect, is a better fit for what we are trying to do.”
Trash clearance and no-till drilling aside, the seeder’s other key benefit is its divided hopper – applying seed and fertiliser in one operation could be helpful in a system that aims to reduce passes as well as confine wheelings.
The Seed Hawk coulter assembly places fertiliser slightly to one side and below the seed delivered by the second knife.
“I think the idea of applying seed and fertiliser together works really well for oilseed rape, when we can place fertiliser near the seed in the root zone,” says Mr Evison. “For cereal crops, we’ve tried band sowing through both knife coulters and we’ll have a go at applying phosphate at sowing – it’s not very mobile in the soil so that could be a useful technique.”
Still learning
Only the vining peas are treated to a ploughed and prepared seed-bed, but that may also change if a small trial area sown into lightly cultivated ground proves successful.
“We are still learning with the new drill and further down the line we’ll be experimenting with reduced seed rates in the wide rows, as well as variable seed rates within fields,” says Mr Evison. “But I like what I’ve seen so far and I’m confident we can go a long way with the principles of controlled traffic farming.”