6 top tips to minimise compaction at harvest
Climate predictions indicate that for the next 20 years there is a 35-40% chance of a wetter-than-average summer, giving rise to the potential for disrupted and challenging harvests.
Aside from the yield and quality implications, soil health can be severely affected too. Experts share their tips on how minimise compaction at harvest.
See also: Rules reminder: Stay road legal this harvest
1. Tyre inflation pressure
High tyre inflation pressures increase compaction, with wetter, weaker soils suffering significant surface and deeper compaction, explains Dick Godwin of Harper Adams University.
Most major manufacturers have mobile apps to help calculate pressures and Prof Godwin recommends growers check the tyre specifications and aim for the lowest inflation pressure to carry the load, but be mindful of remaining safe on the roads too.
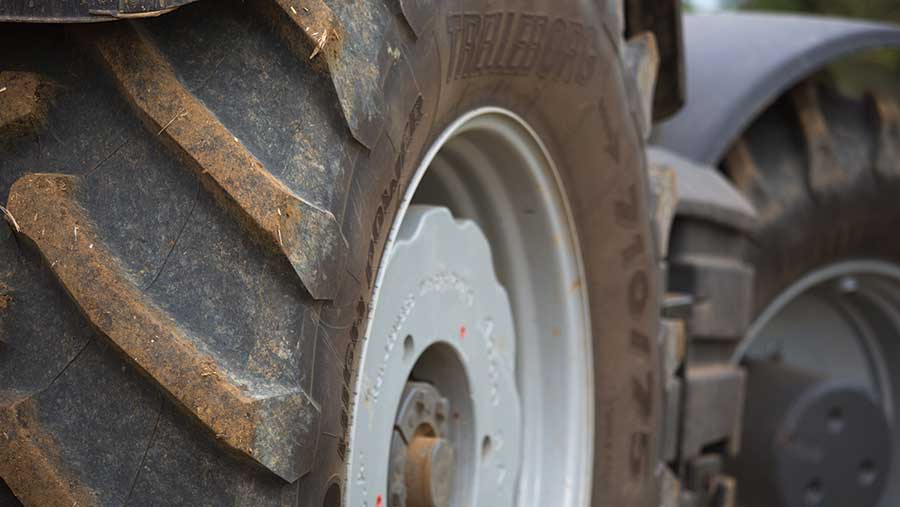
© Tim Scrivener
“While you can tolerate tyre flexing at low speed on the field, at high speed on the road you can’t,” he says.
Kirk Walker of Mitas tyres suggest growers consider investment in tractor and combine tyres with increased flexion; some can operate as low as 8psi, he says.
These can minimise compaction damage by increasing the footprint, allow a wider harvest window and are lower maintenance as they can run at low pressure on the roads too.
Don’t forget trailers – choose the biggest section tyres you can get and run those at the lowest inflation pressures, or fit dual-axle tyres, adds Prof Godwin.
2. Minimise weight
Weight influences the depth to which compaction is driven, so in susceptible areas don’t fill trailers up and empty them at the end of each run so you are not running with a full combine.
Don’t use the greedy boards and be sensible about the extra burden you put in the tank, advises Prof Godwin.
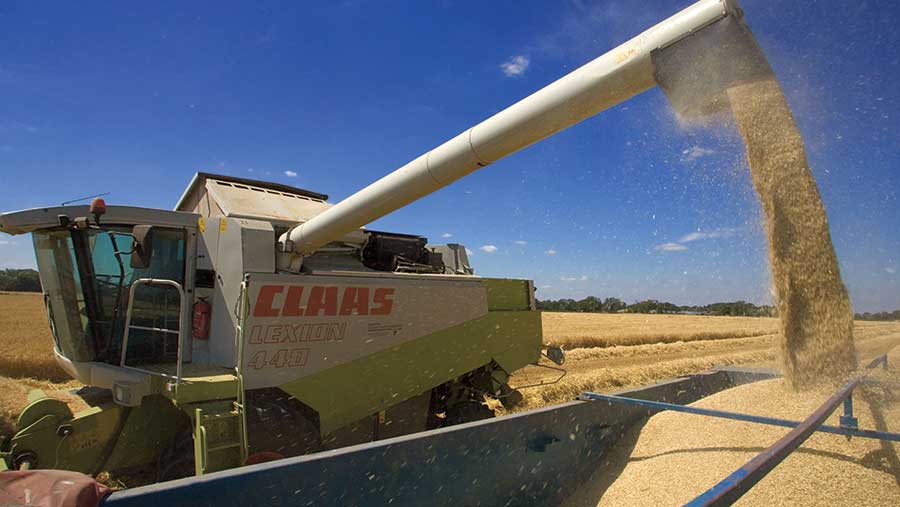
© Tim Scrivener
3. Tracks v tyres
Switching from tyres to tracks is a consideration when planning future purchases, as they reduce the depth of compaction, confining it to the top 35-40cm compared with 60cm for conventional tyres, says Prof Godwin.
Alleviating compaction from the combine tracks also costs less. A subsoiler working at two-thirds the depth results in an approximately 50% reduction in the draught force required, using less energy.
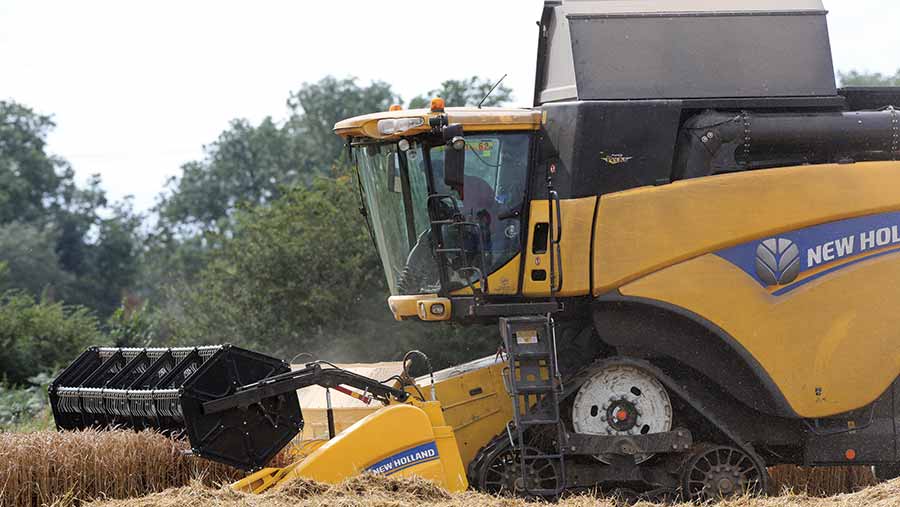
© Tim Scrivener
4. Controlled traffic farming (CTF)
Focusing traffic into single lanes reduces compaction throughout the year and harvest time is crucial as field traffic is at its peak, explains independent agronomist Simon Draper.
Growers who have adopted CTF will be set up in terms of permanent lanes and machinery spacings, but even those who are not can unload the combine at the end of the run, keep trailers off the field or run them up existing tramlines and combine tracks.
And if you get a straw contractor in, get them to stick to tramlines rather than wandering all over the field.
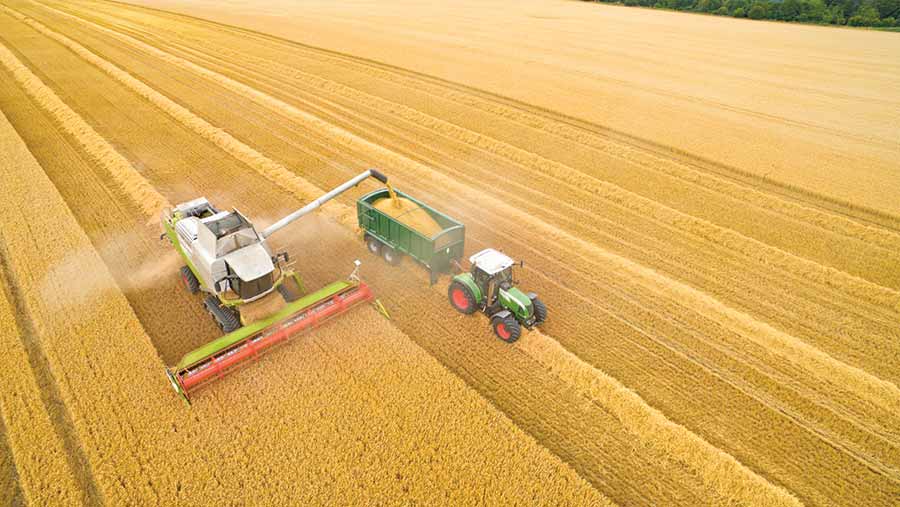
© Juice/Rex/Shutterstock
5. Prioritise fields
As crops senesce, their ability to pump water from the soil diminishes. Evaporation and drainage rates will determine how much moisture the soil will tolerate before conditions for travel become marginal.
Mr Draper suggests growers identify which fields are the wettest and target those fields to combine first. If conditions do turn wet, growers can expect to add up to 12.5cm of compaction at harvest.
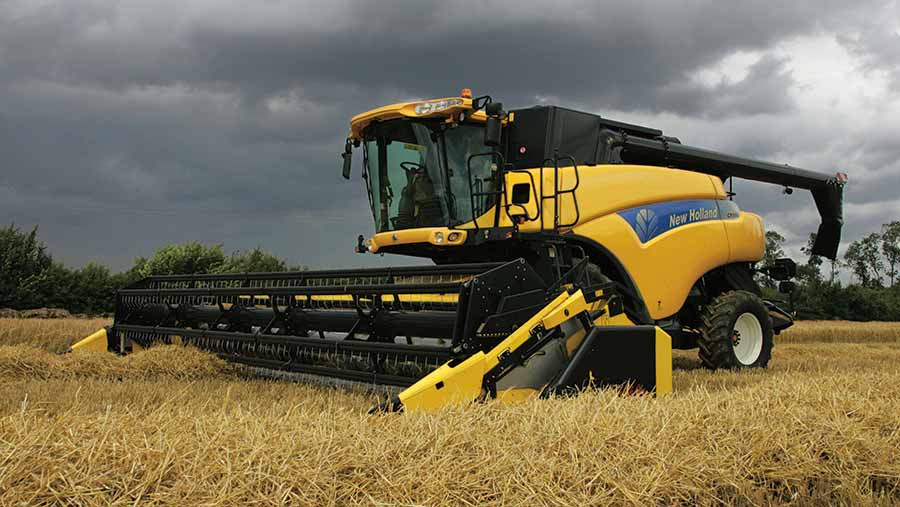
© Tim Scrivener
6. Taking remedial action
In a wet harvest, compaction may be unavoidable. When planning remedial subsoiling action, Mr Draper advises growers to dig down to the depth of the subsoiler and collect a handful of soil.
“If you can form it into a ball without cracking it is too wet,” says Mr Draper.
In this case, the best option is to leave it alone and let the soil dry out, he says. Either plough or cultivate down to 15cm and aim to subsoil later.
Compaction normally only goes in to subsoil depth, so the base of the subsoiler wing should travel at the break point between the top and subsoil.
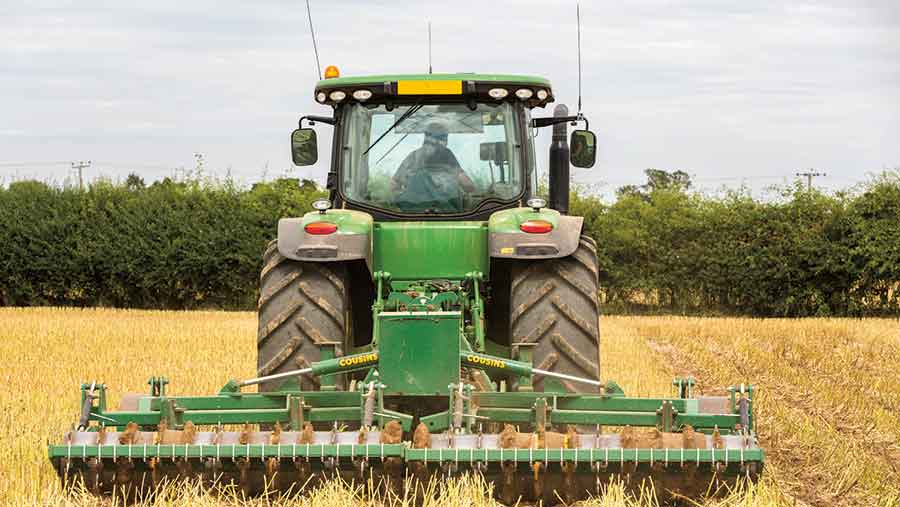
© Tim Scrivener
“If you are subsoiling more than 1-2in [2.5-5cm] below the break point, ask yourself why you are doing it.”
Prof Godwin suggests growers focus on wheelings, headlands and turns. “That might only be 30% of the field and only 30% of the subsoiling cost.”
He advises putting the winged tines in the combine wheel marks and running a pair of shallow tines, 15cm deep and 30cm apart, ahead of the deeper ones to take off the overburden and prevent the main tine pulling up big lumps.
“By taking the overburden off, your tines will be more effective and the inherent soil pressure will be less.”