Simple steps to energy-efficient dairy farming
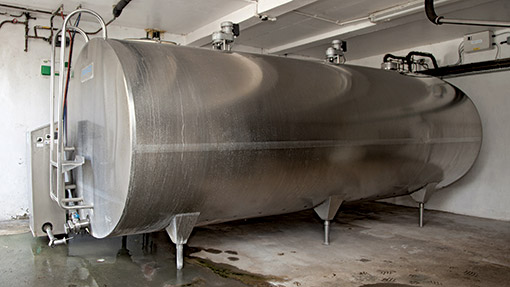
Milk cooling, water heating and vacuum pumps account for the biggest proportion of energy use on dairy farms, so it is these areas that offer scope for the greatest savings.
DairyCo estimates each of these three areas accounts for 25-30% of electricity consumption on a typical farm. But there is a massive range in total energy use (electric and fuel) across farms, says Ian Powell, director of The Dairy Group. Electricity costs, for example, range from ÂŁ23-85 a cow a year (see table 2).
This variation is due to many factors, from fuel use to the proportion of more expensive day tariff (normally 7am until midnight) electricity used and its unit cost, he says.
“With profit margins under pressure, there is an urgent need to review all business costs, including electricity, power and diesel.”
Cutting costs
Plenty of companies offer energy audit services, but the first step any farmer can take to improve efficiency is to identify the main consumers of electricity. Record consumption, collect data from bills, read meters regularly, or install a smart meter.
Next, ensure the business is on the best tariff and maximise use of off-peak electricity (Economy 7). DairyCo says E7-type tariffs usually charge a higher unit price for daytime electricity, so at least 15% of total electricity use must be during the cheap-rate period to save money over a standard tariff, although most farms can do this by heating all hot water during this period.
Basic measures, such as using timer switches, lagging pipes (hot and cold) and water tanks, replacing halogen floodlights with sodium lights, plus ensuring equipment, such as condensers, are clean and well-maintained also make a big difference, says Neil Nicholas of the Dairy Development Centre.
A DDC audit of 225 Welsh dairy farms carried out by the Farm Energy Centre (FEC) during the past three years suggests many energy-saving measures will pay for themselves relatively quickly.
Condenser maintenance is a common problem, adds Jon Swain of the FEC. “Half an hour spent cleaning condensers with a low pressure hose and soft brush will pay off instantly. Make sure condensers are well located to avoid recirculating warm exhaust air.”
Installing energy-efficient equipment such as bulk tanks, variable-drive vacuum pumps or heat recovery units can make a big difference to energy use, but the high capital costs often mean the scale of energy savings is unlikely to warrant early replacement, Richard Davies of DairyCo adds.
“Electricity only accounts for 1.5-2% of the cost of producing milk – about 0.5p/litre – so keep it in context before buying new kit. When equipment needs replacing, certainly consider systems that save energy – it may be possible to get some capital grant funding through the RDP [England] or Glastir [Wales] to help fund such investments.”
Table 1 – Costs and savings | |||
Item | Typical saving (ÂŁ) | Annual cost (ÂŁ) | Payback from energy saving alone (years) |
Bulk tank | |||
Convert from large (<20,000 litres) ice bank (IB) to direct expansion (DX) tank | 32,000 | 1,250 | 25.6 |
Medium (<10,000 litres) IB to DX | 17,000 | 500 | 34.0 |
Small (<5,000 litres) IB to DX | 14,500 | 275 | 52.7 |
New compressors | |||
Large tank | 10,000 | 987 | 10.1 |
Medium tank | 5,500 | 434 | 12.7 |
Small tank | 4,800 | 217 | 22.1 |
Fit a plate heat exchanger (PHE) – 5C | |||
Small | 1,600 | 240 | 6.7 |
Medium | 2,400 | 487 | 4.9 |
Large | 3,200 | 1,107 | 2.9 |
New water heater | |||
100 litre | 920 | 64 | 14.4 |
300 litre | 1,800 | 193 | 9.3 |
500 litre | 3,000 | 322 | 9.3 |
Heat recovery unit (HRU) | |||
300 litre/day | 2,500 | 388 | 6.4 |
500 litre/day | 3,100 | 648 | 4.8 |
1000 litre/day | 4,000 | 1,296 | 3.1 |
Retrofit a variable-speed drive to existing vacuum pump | |||
3kW of pumps | 1,200 | 292 | 4.1 |
6kW of pumps | 1,500 | 584 | 2.6 |
9kW of pumps | 2,000 | 877 | 2.3 |
Source: FEC Notes DX tanks offer more efficient cooling than IB tanks, but only run when milking. IB tanks use cheap-rate electric. Ice builders provideseparate cold water supply to PHE. Can maximise use of cheap-rate electricity. Pre-cooling with a PHE uses mains/borehole water in firststage of milk cooling (no electricity required). HRU uses waste heat from refrigeration system used in milk cooling to pre-heat waterbefore going into water heater (not suitable where plate heat exchanger is used). VSD vacuum pumps automatically vary speed while milking,but are not suitable for all pumps – check with your dairy engineer |
Table 2 – Milk production energy efficiency benchmarking | |||
Power efficiency | Average | Low | High |
Electricity | |||
kW hours a cow a year | 423 | 231 | 811 |
kW hours/litre of milk | 0.06 | 0.03 | 0.09 |
% day electricity | 62% | 11% | 98% |
Cost ÂŁ/cow | 42 | 23 | 85 |
Cost p/litre | 0.6 | 0.2 | 1.1 |
Power and diesel | |||
Horsepower/cow | 3.0 | 1.1 | 7.9 |
Diesel, litres a cow a year | 99 | 20 | 258 |
Diesel cost p/litre/year | 0.8 | 0.17 | 2.22 |
Source: The Dairy Group |