Willow diversification secures beef farm’s future
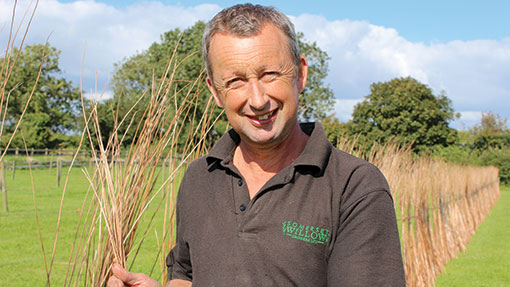
Forming a business partnership and fulfilling the modern customer’s delivery demands has helped secure a bright future for one Somerset farmer’s diversification into willow, as Aly Balsom reports.
It may have started as an add-on to his beef enterprise, but Richard Robert’s willow growing venture has proved so successful he’s now inclined to relabel himself a willow farmer instead of a beef producer.
Somerset Willow Growers now farms 16ha (40 acres) of the crop, processing 50t of weaving willow a year for sale through their website and as part of a business partnership.
The move towards the enterprise has been part of a drive to farm more sympathetically with the environment following the family’s move out of dairying in 1999. With all of the farm’s land on King’s Sedgemoor, Richard and his father quickly realised intensive dairy production didn’t fit well on land that flooded regularly.
With much of the grassland put in an Environmentally Sensitive Area Scheme (ESA), it made sense to keep some beef cattle. At the same time, Richard started thinking about other options. With the farm located in Westonzoyland in the heart of the British willow growing industry on the Somerset Levels, this seemed an obvious choice.
“My first thought was to develop a market for coloured bark willows, so in 2001 I planted 32 different varieties on a one acre patch. I then approached retailers, but I quickly learned they liked to source everything from one supplier,” says Richard. “I heard somewhere that 80% of farm diversifications fail because they don’t have a market and I didn’t have one so I failed.”
However, shortly afterwards, Richard was approached by a local weaver who was struggling to source material.
Although the Somerset Levels are renowned for growing the crop, over the years the industry has declined dramatically following the introduction of modern materials like plastic. Now there are just a handful of growers on the levels who are the only producers of commercial weaving willow in Great Britain.
Darrell Hill from The Somerset Willow Company was struggling to source product for his 25 weavers at his site in Bridgwater, which created a ready-made market and business partnership for Richard.
Did you know?
- New willow cuttings are planted at 17,500 cuttings an acre.
- Once established, a bed can last 30 years
- The main processing technique involves boiling willow for eight hours so the bark can be stripped.
- Willow is harvested between November and March on the Somerset Levels.
- About 1,200ha (3,000 acres) of willow used to be grown on the Somerset Levels, now it’s under 120ha (300 acres).
“Darrell had the industry knowledge, but didn’t know how to farm or have the equipment or premises to grow willow so it worked well as a partnership,” he says.
The two quickly drew up a contract and formed Somerset Willow Growers with each taking a 50% share.
“The idea was for me to produce a level supply of willow for The Somerset Willow Company to make into things such as hot air balloon baskets, coffins and hampers, and Somerset Willow Growers would sell willow to hobbyists via a website,” Richard explains.
The revenue that The Somerset Willow Growers makes comes equally from Somerset Willow Company, online sales and telephone sales.
The pair decided to design the business around creating a level supply of material for customers throughout the year. “Willow production is traditionally quite seasonal. It’s cut in the winter, processed in the summer and then runs out in the autumn. We knew when we started that customers wanted next-day delivery for 12 months of the year so that’s what we decided to do,” Richard says.
To meet this demand, the business had to invest in temperature-controlled storage where the ready-made product could be stored as a dry product, ready for shipment.
To start with, they took on 8ha (20 acres) of established willow bed from a neighbouring farmer who was gradually retiring. Over the years, this area has gradually increased and Richard has also established 4 acres of new beds using cuttings, bringing the total area to 16ha (40 acres).
“We produce a seed-bed a lot like you would with maize, apply farmyard manure, plough and work down. We then use a planter to put in the cuttings which are about 10mm thick and 300mm long,” Richard says.
Cuttings are planted in May and in the first year reach about 1.2m-1.5m tall with 3-4 willow “rods” shooting up from each cutting. This develops into a stump with 20-30 rods growing out of it.
“In the first year, we got 6t from 1.5ha (4 acres) and 18t in the third year. Every time you harvest, you cut it virtually to the ground,” explains Richard.
The main harvest season is from November to March. It’s crucial the plant is cut when it’s dormant, as once it has “woken up” if can be difficult to store without it heating up.
During harvest, a team of nine work to cut and gather the crop. Two home-made self-propelled machines cut the crop, which is automatically bundled and tied in 10kg bundles and manually picked up.
Beds are then trimmed in the last week of April using a rotary topper. This is crucial because if the plant was left until the next winter, the willow would become too tall and thick for weaving. Ideally, it needs to be 8-10mm thick and primarily 1.8m-2.1m tall.
To reduce risk, Richard staggers the date when fields are trimmed. This means he’ll have different crops at different stages so there will always be something to harvest even in a poor year. Trimming in April also provides a good opportunity for weed control.
“One week after trimming, we spray with a weak dose of herbicide to check the weeds before the willow shoots. You can’t spray during the growing season as it kills the willow,” says Richard.
After harvest, each willow bundle is sorted as each plant will produce rods of different lengths. Weeds and rushes are sifted out by hand and rods grouped in piles of varying length from 0.9-2.4m high.
About 25% of the crop is processed straight from harvest with about 18,000 bundles stored in an open barn and allowed to dry naturally for processing later.
At processing, willow is boiled for eight hours to soften so the bark can be stripped off. After stripping, the willow is then dried naturally in bunches outside. These will then be sorted to remove any imperfect rods, weighed and bundled. Anything not going to Darrell for weaving will then go into temperature-controlled storage.
Different processing techniques are used to produce willow of varying natural colours. For example, standing the bottom 15cm of bundles of freshly cut willow in water and not boiling it is part of the process for producing natural white wood.
The business is constantly thinking about different marketing options and has started dying some white willow different colours and producing “starter kits”. To spread risk further, they have also diversified into exotic weaving materials such as rattan, sea grass and bamboo imported from Indonesia and China.
Contrary to common belief, the plants don’t like lots of water and are particularly adverse to standing water. Because the 2012 floods occurred during the main growing season, the willow was repeatedly killed off, causing the plant to send out side branches. As a result, the team had to take four million secateur cuts post-harvest to cut off the shoots and that year they made a small loss. Because the flooding in 2013 was after the growing season, it meant the team couldn’t get on the ground to harvest until later. It was then that having stores came into play, allowing the business to still meet demand.
Richard says advertising and marketing is essential and was particularly crucial during the flooding to communicate they were still taking orders.
“You have to advertise. It’s a lot better than beef as you can set your own price based on cost. We’re doing about 20% profit on turnover,” he says.