Optimising air flow for layers
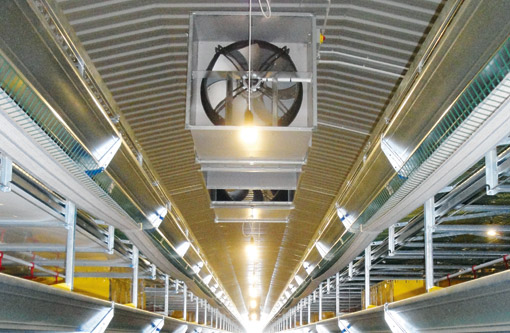
Ventilation is recognised as a key factor in getting the best from broilers, but can be overlooked when it comes to egg production. Rhian Price reports from one egg farm which has invested in new systems
With the price of feed showing signs of climbing again, substantial savings can be made by maintaining minimum ventilation rates and optimising the temperature in layer sheds, according to environmental management advisor Draper Ventilation.
“Inside poultry sheds heat rises off birds into the roof space, which means there can be as much as a 15C difference in temperature between the roof and the floor,” says the company’s business development manager, Ian Griffin.
The loss of heat can impact heavily on a business, as when birds are cold they eat more to maintain their body temperature. However, the increase in food intake doesn’t equate to higher egg production, Mr Griffin explains.
The energy saving specialist has come up with an innovative solution to tackle cost challenges. It has designed a ventilation system to minimise heat loss, which in turn lowers excess feed consumption.
An air handling unit, which is installed in the roof space, works by re-circulating rising heat back throughout the shed to provide uniform, warm conditions.
“The unit comprises of an air mixing chamber and two fans which sit on either side of the chamber,” explains Mr Griffin. “It introduces fresh air through a roof cowl with automated valves and mixes it with the warmer internal air which dries and heats the moist outside air.”
The air is then circulated around the shed by fans in large circular patterns, which ensures the birds on the bottom tier are equally as warm as the ones on the top.
The unit is fully computerised and the automated valves precisely control the process.
“A measuring fan evaluates the amount of air coming into the shed and the information is fed back to the computer which instructs the automated valves on how far they can open,” says Paul Draper, managing director of Draper Ventilation.
The minimum ventilation system, which works under positive pressure, keeps conditions fresh and dry all year around and temperatures can be maintained within 1C of set temperature, even on the coldest night.
If the temperature inside the shed reaches more than 21C, a system of cross-ventilation kicks in. The extraction fans located along one side of the shed come on in steps to slowly acclimatise the birds and reduce the temperature.
“Equipment transitions inside the shed are as gentle as possible to reduce the stress on the birds,” says Mr Griffin.
The extraction fans create a negative pressure of 40pa (pascals), which draws outside air into the shed through specially-designed inlet louvres. The inlets are aerofoil-shaped which enables them to jet air across the roof of the shed at 6m/sec.
“The main ventilation system kicks in to act as a cooling effect,” explains Mr Griffin. “It is extremely important to get the velocity right, because if you don’t, you won’t get the airflow from the top tier to the bottom.”
Peter Hewlett, PJR Farms, Rodley, Gloucestershire
Peter Hewlett first trialled the Draper ventilation system in one of his free-range sheds housing 6,000 birds in the winter of 2010.
Comparative performance data revealed the ventilation system lowered feed costs per egg by approximately 19%. The laying rate also increased by 3%.
Mr Hewlett, who supplies many of his eggs under his own brand Local Yolks to a plethora of pubs and restaurants in Gloucestershire, was so impressed with the system that he has since rolled it out to the other free-range house, as well as fitting it in his newly-constructed 18,000 colony unit.
“I couldn’t believe how dry and friable the litter was,” Mr Hewlett said. “You have only got to be stood in the middle of the shed to feel the gentle, uniform air movement.”
Inside the multi-age colony shed, litter is carried outside on belts, where it is stored and used as a fertiliser on the crops. Mr Hewlett said the ventilation system ensures his manure is always dry, reducing handling costs.
The atmosphere inside free-range sheds is notably harder to control in comparison to other systems.
However, the installation of the ventilation system inside both free-range sheds has reduced ammonia levels considerably. Previously Mr Hewlett said he was using a couple of bales of straw each week to dry the litter. But now he says he only uses a few bales of shavings at the start of production, which has reduced bedding costs and labour time significantly.