Top tips for clean water in poultry production
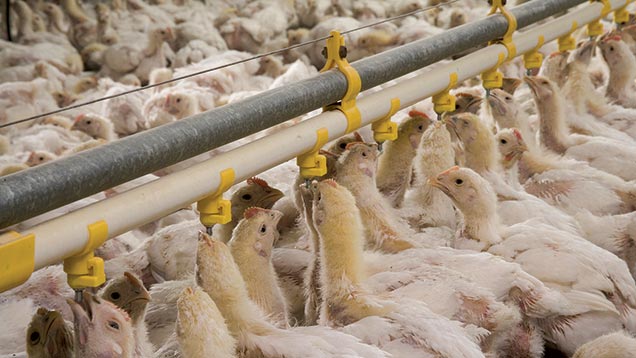
Close attention to every single detail is the key to ensuring both broilers and layers get a good supply of healthy water, free of bugs and available on demand.
According to Susan Watkins from the division of agriculture at the University of Arkansas, water issues are frequently behind a whole range of problems affecting flocks’ performance.
There are two broad areas to consider, she suggests – health challenges and water availability. “If we are witnessing health symptoms, then we suspect contamination, whether it is microbial, something arising naturally in the water, or even something we are adding.
“But if there are no obvious health symptoms, then we have to suspect water consumption issues – they don’t have enough, there are restriction points, or they don’t like it.”
Health challenges
Water is the perfect carrier for bugs, says Dr Watkins. Visually clear water may still be laden with bacteria, viruses, protozoa and roundworms.
“Poultry drinking systems make it easy for microbial contamination – the water is slow moving, it gets warm, it has many nooks and turns, and it contains the things that the organisms need to grow, like iron, manganese and sulphur.”
Top sanitisation tips
- Do a total bacterial plate count to identify contaminants
- Use the right concentration and exposure time of product
- Clean everything, including storage tanks and distribution lines
- Follow cleaning with a sanitiser that birds can drink
- Swab the water lines regularly to monitor
- Sanitise between flocks
According to Dr Watkins, the key for success with water quality is a good sanitisation programme. “There are some wonderful products out there, but it is essential that you use them right.”
Product concentration and, in particular, exposure time are critical. For example, tests by the University of Arkansas using a 3% bleach solution found that, even after four hours, there were still bacteria in the water at almost 1,000 cfu/litre, and this had come down little after 24 hours.
Monitoring is also crucial, both pre- and post-cleaning, to provide proof of effectiveness.
“I see a lot of weaknesses where people say they are doing something, but there is no verification of it. How many times do our medicators malfunction? How many time do we miss it and we get problems? Those microbes are out there and they’re waiting, so make sure you keep that sanitation pressure on and make sure you verify that it is there.”
But however good the system or product, biofilms will always present a challenge, harbouring things like E coli, streptococcus and pseudomonas. “They are just so durable. They were here on this earth before humans arrived, and they’ll be here after we’ve gone.”
Cleaning products
Chlorine has been a “friend” for many years, says Dr Watkins, and is a great sanitiser. But getting the pH level of the water is critical.
“The way chlorine dissolves into water, it’s either going to be the acid form or the ion form that dominates. If the pH is below 7, then the acid form dominates. But if the pH gets above 7, we’re going to have more of the ion form. It is the acid form that is the strong sanitiser.”
But even getting pH right does not guarantee success, says Dr Watkins, pointing to emerging problems of bacterial resistance. She suggests it may be time to introduce product rotation. “Just as we would not stay on one coccidiosis programme, we need to think in the same way about our water sanitation programme.”
In the USA, more broiler growers are turning to hydrogen peroxide as a daily sanitiser. Delivered at 25-50ppm residual in drinking water, good results have been achieved, without putting the birds off drinking. Stabilised products give the best results, says Dr Watkins.
Chlorine dioxide is also gaining popularity, produced by taking sodium chloride activated with an acid. The product has a number of advantages, including that it is pH insensitive and is more selective than hydrogen peroxide, targeting pathogens even at low dose rates. But it has to be activated properly, requiring correct pH levels and enough contact time.
Water systems
As well as choosing the right product, poultry producers should pay close attention to their water delivery.
“It is crucial to understand your entire water system, so do an inventory. Exactly how many drinkers do you have? How long is the system? What are the distribution lines made out of? What repairs have been done? Do you have any dead end lines? How far is the distribution from the source to the barns? You can clean the in-shed lines all day long, but until you clean the distribution lines your problems will come back over and over again.”
Dr Watkins also stresses the importance of routinely checking injectors. “Don’t just run a gallon of water through to see it’s OK. You’ve got to run twenty to thirty gallons through, to allow the injector to get up and running and ensure you’re getting the proper dosage to those birds.”
Water quantity
Research by the University of Arkansas shows that, compared with 10 years ago, broilers are now drinking 38% more water in the first seven days of life, and 16% by the time they reach slaughterweight – equivalent to 15 gallons more water.
Impact of water temperature on broiler weights (g) | |||
---|---|---|---|
Temperature | Day 1 | Day 7 | Day 14 |
4.4C | 46.5 | 187 | 501 |
21.1C | 47.4 | 188 | 501 |
37.8C | 46.7 | 167 | 463 |
By day 14, birds drinking the warmest water were 38g lighter |
Ensuring they get enough is key. “You must be sure you are not creating restriction points.”
Water lines must be of a suitable diameter to deliver the required volume at peak demand times, otherwise birds will fail to put on sufficient weight, will have higher mortality and, for layers and broiler breeders, reduced egg numbers.
If pressure reducers are in place, these must be checked to ensure they are not becoming clogged.
It is also good practice to regularly monitor drinker flow rates. Use of chlorination products has been known to harden the regulator seals, resulting in a failure to regulate pressure.
And then it is necessary to ensure the drinking water is being delivered at the right temperature. Day-old chicks are happy enough with cool water, and even room temperature water, but will shy away from warm water, seriously affecting weight gain. (See table above)
“Water can make or break an operation,” says Dr Watkins. “There are many different factors involved and understanding each is essential so we can quickly determine when we are going awry and fix it before it becomes a chronic problem that’s costing producers a lot of money.”