Switch to self-feed silage system helps cut dairy costs
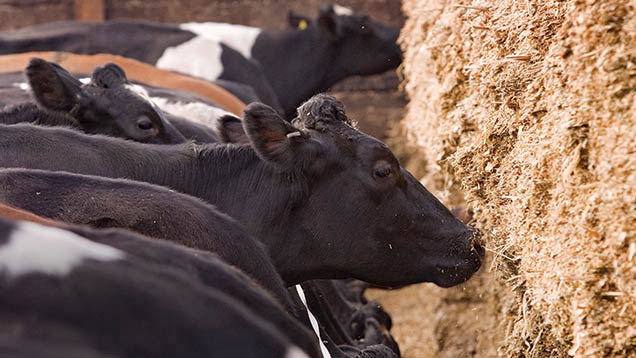
A North Yorkshire dairy farmer has gone back to self-feed silage and reckons it is saving the business £350/week in fuel and labour costs compared with the previous system.
The 380-cow organic Friesian Leasbeck herd, run by the Howarth family at Leas Farm, Pickering, now has round-the-clock access to a 50m-wide silage face. The clamp – 50x40m – stands on a newly constructed concrete pad.
The free-standing clamp, which contains the farm’s annual three silage cuts, has no walls or roof. Big bales of silage are used to give some stability along the sides.
See also: Guide to choosing and using silage additives
Cost
Cows are fed silage to appetite with daily intakes of about 10-15kg of dry matter.
Mr Howarth says the self-feed system is reducing both labour and fuel costs.
“When we were feeding bales it was costing us one man for two hours a day – at £25/hour. So that is £50/day or £350/week. We only have a short winter here, but over 20 weeks that is a saving of £7,000.
Farm facts
- Organic British Friesian herd
- Yielding 6,000 litres at 4.2% butterfat and 3.5% protein with 4,000 litres produced from forage
- Target lifetime yields of 50,000 litres
- Herd is paddock-grazed, with grass measured weekly
- Cows are run as one group and fed to yield in the parlour
“It has allowed us to keep a lid on costs while still increasing cow numbers and running a straightforward system.
“We used to use a feeder wagon, but when we started to expand the herd we felt the additional cost needed in machinery wasn’t justified.
“We can now continue to increase cow numbers to about 400 without a further significant investment,” he adds.
Feed barrier
The silage face provides six inches of feed space a cow for 300 milkers. The herd’s first calvers are run separately and given trough-fed silage.
An electric fence – which is moved up two to three inches a day – is the only barrier controlling how much forage the cows can eat and allows them to reach up to 2m in height up the front of the feed face.
“We were previously feeding big-bale silage, but as herd numbers increased it was becoming too costly in terms of labour and fuel,” says Sam Howarth.
“So two years ago we decided to switch to a self-feed system and constructed the concrete pad alongside the cubicle house. Although the concrete area cost £50,000, it was a job that needed doing anyway,” he says.
The first year the clamp had no side supports, but big bales now give it some shoulders, allowing more grass to be ensiled.
“We have created a flexible system with no extra feeding work at weekends. We can also allow cows to feed from either end of the clamp,” adds Mr Howarth.
How the clamp works
Silage is removed from the top of the clamp as the cows work their way through the forage during the winter. “The clamp is stacked a little higher than 2m, so we take some off the top and feed that to youngstock.”
Cows walk over from the cubicle house to access the silage clamp, but Mr Howarth says there is never a rush when the electric fence has been moved.
“When we had the feeder wagon the cows heard it revving up and when you opened the gate there was a mad rush to the feed barrier. Now there is never any panic to get to the feed face when we have moved the fence and there is no jostling.”
Mr Howarth says it has also benefitted staff welfare as cows are more contented. “Staff welfare is as important as cow welfare,” he says.
Spoilage
There has been no spoilage problems at the feed face, and Mr Howarth reckons there is less waste than if a grab was used to take silage from the clamp.
He adds: “Cows are taking silage in small amounts all the time and so the face is eaten back very evenly and cleanly. If we were taking it off with a grab we would not be going back to that same part of the face for several days and that is when spoilage happens, unless you have a narrow clamp.”
Silage is based on four- to five-year leys of perennial ryegrass with red clover, aiming to produce 10-12t of dry matter a hectare from three cuts.
Ensiling procedure
Newly clamped silage is covered with a layer of “cling film” and topped with a purpose-made silage cover.
“We put a lot of time and effort into ensiling the grass and always have an extra tractor rolling the clamp. Sheeting the grass down is done very precisely.”
This year there has been more second cut at the front of the clamp, but the plan for next year is to fill the clamp from the other end.
“That will mean we can feed more first-cut silage in the early part of the autumn and winter and that is what is so good about this system – we have total flexibility,” he says.