What’s in Your Livestock Shed? visits a state-of-the-art £1.3m dairy unit
Andrew and Julie Thomas and their son, Richard, wanted a building that first and foremost provided a stress-free environment from their housed pedigree herd of high-yielding Holsteins.
This they have achieved this with a ClearSpan dairy unit with cubicles designed specifically for their large cows and with exceptional ventilation and plenty of light.
See also: Read more What’s in Your Livestock Shed? articles
“Light and air are free, so we wanted to make full use of those,’’ says Andrew.
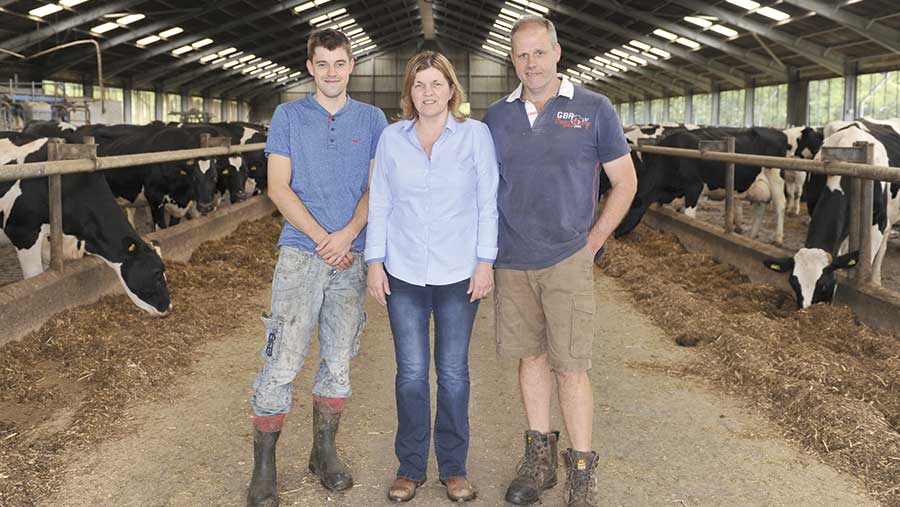
Richard, Julie and Andrew Thomas © Debbie James
Enabling expansion
It has enabled cow numbers to be increased to 430 and, with another 100 heifers due to enter the herd in the next 12 months, they plan to cull heavily for mastitis and fertility.
The Thomas family are now on course to milk 500 cows within a year.
“The thought behind the shed was that if push came to shove and we didn’t have outside labour, we could manage by ourselves,” explains Julie.
Cows were first milked and housed in the new facilities in February 2013.
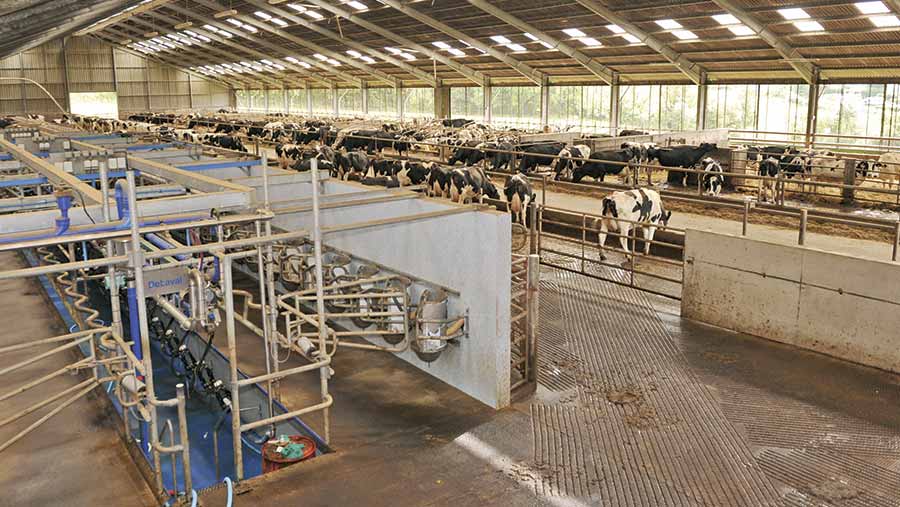
© Debbie James
Shed setup
The building incorporates cow cubicle accommodation for 370 cows, a 30/60 herringbone parlour, collecting yard, cow-handling facilities, calf pens, an office and a machinery room.
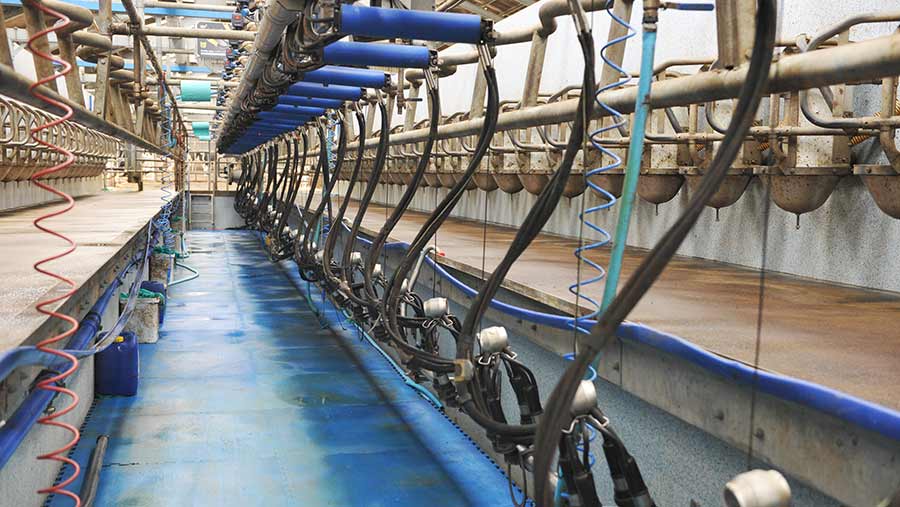
© Debbie James
The milking parlour has in-parlour feeders. Floor surfaces and walls can be easily cleaned using harvested rainwater.
There are handling facilities alongside the parlour and unobstructed passages allow for easy movement of cows. The slatted floor collecting yard is incorporated within the housing.
To avoid the need for additional space in the shed, a 28,000-litre vertical milk silo has been installed on the exterior of the building.
The use of energy-saving pumps, rainwater capture, three-phase motors and the efficient management of slurry – which all contribute to save energy – made the parlour a clear winner of the 2017 Royal Welsh Agricultural Society’s Farm Buildings and Works Competition.
Capacity for storing slurry for five months of the year means it doesn’t need to be spread until the spring and at the furthest point on the land, farmed slurry is pumped for two miles.
“We are fortunate that every piece of ground we rent is an ex-dairy farm and they all have slurry storage, so we have ample space,” says Julie.
Four cuts of silage are taken, together with 49ha of maize, which is incorporated 50:50 in the ration together with minerals, alcacarb, 0.75kg chopped straw, 2kg maize distillers’, 1kg soya, 3kg sugar beet and 3kg barley.
How did you design the unit?
We saw similar buildings in Holland and Scotland. The roof pitch of these was much higher than what you would see in standard cubicle housing – ventilation was very important.
We sourced some good information on this online. And we commissioned the same architect who designed many Scottish dairy sheds to draw up our plans.
We all had an input into the design. Julie was a keen advocate of slats to reduce labour and Andrew insisted on a high pitch roof with open sides.
How was it constructed and by whom?
A local contractor, Meredith Davies, oversaw all the excavation and concrete work and he managed the whole project.
Mark Wookey supplied a lot of the materials, such as the slats and the automatic ventilation curtains. We can’t praise both men highly enough.
What was your initial budget and did you stick to it?
The total cost was just short of £1.3m; more or less what we had budgeted for. We were fortunate to receive a £50,000 Glastir capital grant for the underground slurry store.
Tell us about the shed’s specifications.
The building is 320ft long and 134ft wide with cubicle stalls for 370 cows.
The building has a galvanised steel portal frame with a 22.5deg roof pitch. There are overhanging eaves and corrugated fibre cement roof sheets on galvanised Z-purlins.
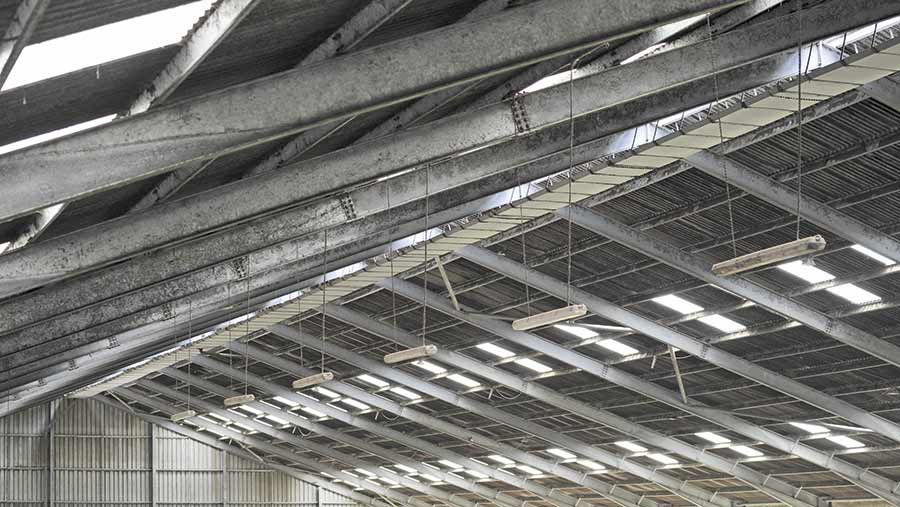
© Debbie James
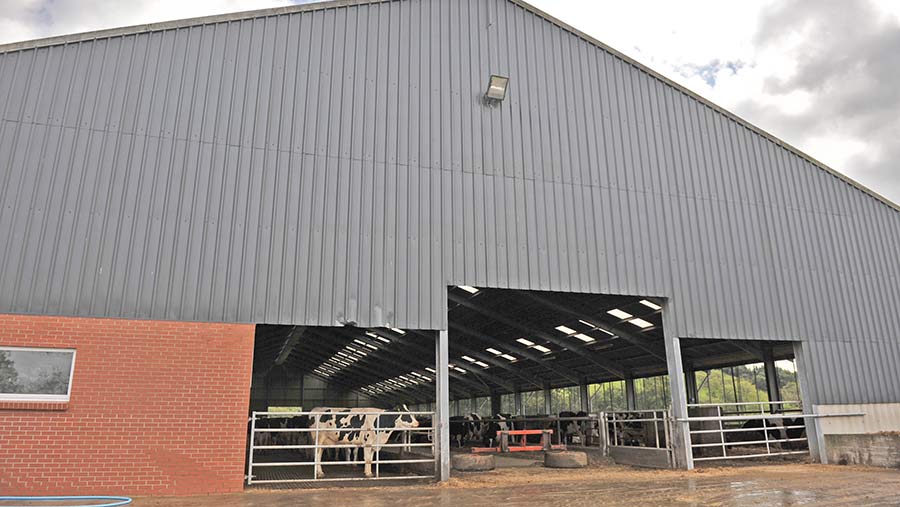
© Debbie James
The cubicle building layout is arranged with rows of head-to-head cubicles and another row of single cubicles repeated each side of a central feeding passage, which runs the full length of the building.
Slurry is stored in slatted, below-ground chambers under all circulation areas between cubicles, including the collecting yard area. The chambers have the capacity to hold up to five months’ slurry.
Slurry is mixed with externally located slurry guzzlers operating on Economy 7 electricity (a type of electricity tariff that has a different price/ kWh based on your time of use).
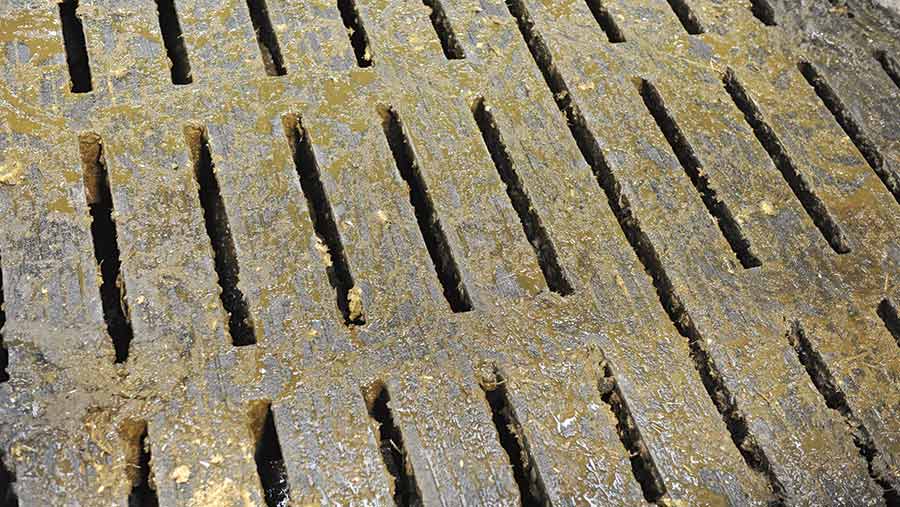
© Debbie James
What’s your favourite feature?
The cubicles, supplied by Wilsons Agriculture, are large – 4.2ft wide and 10ft long – which is ideal for our type of cow.
They are open fronted with no barriers at the front, so there is plenty of lunge room so cows aren’t at risk of hock damage.
They have a high occupancy level. If the cows are not eating, they are laying down. Cows are bedded on deep sawdust.
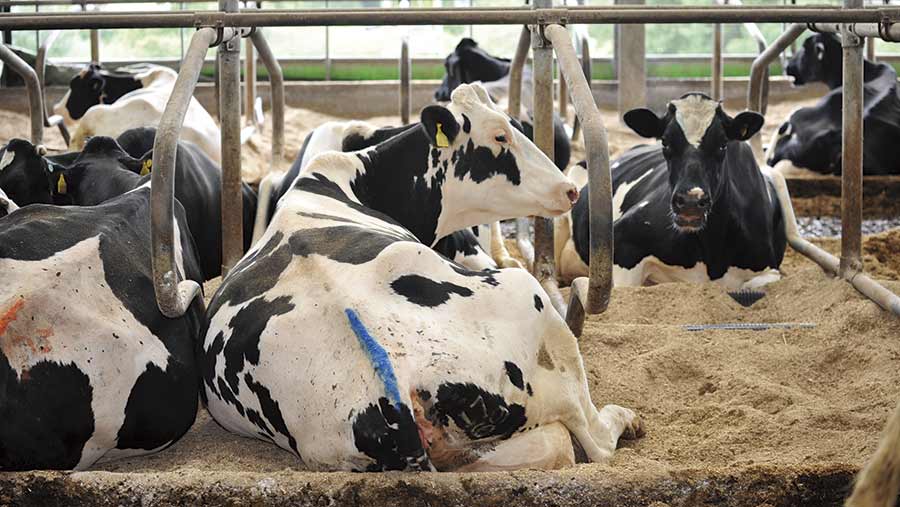
© Debbie James
What’s been your best buy and why?
A. The sensor-controlled ventilation screens. These are on both sides of the shed and are backed with fixed mesh screening and run down to the level of the cubicle beds.
These, combined with a continuous open ridge – with a rainwater capture tray beneath, provides excellent ventilation, resulting in an open, light and airy environment for the cows.
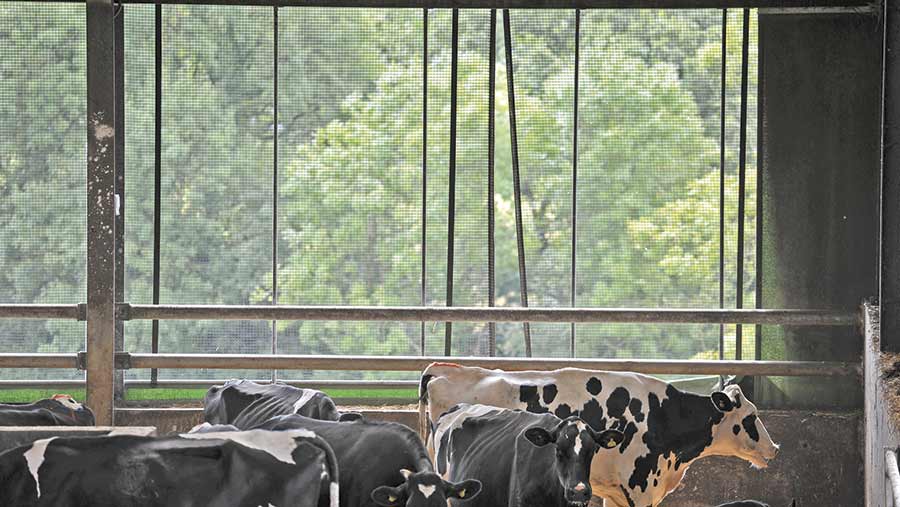
© Debbie James
What couldn’t you live without?
The slatted floor. Scraping is a mundane job – why on earth would you do it unless you had to? The granite slats came ready grooved. We imported these from Belgium.
Farm facts
- 253ha farmed – an even split of owned and rented land
- 10,000 litres annual average cow yield
- 3.89% butterfat and 3.22% protein
- Twice a day milking
- Milk sold to Muller
- Cows fully-housed year round
- Two full-time workers
What would you do differently if you were to build it again?
We would have installed a rotary or rapid-exit parlour.
It would have cost us another £300,000 or so to put in a rotary, so as it was, we had a very good 30/60 herringbone for £120,000.
It is a very cost-effective parlour to milk a lot of cows, but it is tiring on the legs.
Perhaps in 10 years we will be milking more cows and we might change it.
In defence of a herringbone though, it allows you to give more attention to the cows in the parlour, which means we don’t need to walk around the shed checking them afterwards.
We are in the process of installing an automatic cluster dipping and flushing system, because we have had issues with mastitis. But we will still use the old sprayers to pre-spray.
Has any design aspect helped ease management or improve animal performance?
We haven’t seen any improvement in performance, but it is much better from a labour point of view and the standard of comfort means we have happier cows.
What next?
We have planning permission for a new shed on the site adjoining the cubicle building and we will start work on that this spring.
We currently loose house dry cows and heifers in an empty silage pit, which is not ideal, although they do well in there. They will be housed in the new shed.
We have applied for a sustainable production grant to help towards the cost.