Inside story on the World beef outlook
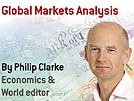
International beef prices have been on an upward trend over the past 12 months, signalling better returns for livestock farmers in the UK and further afield.
What does it mean for beef producers? |
---|
Clearly the UK market has been tight for some time, with total beef supplies lower this year and a further contraction forecast for 2009. But what is happening elsewhere in the world and are current prices sustainable?
Europe
The supply of beef in Europe looks set to continue its downward trend, with the EU Commission forecasting a 1% decline to 7.9m tonnes next year.Unlike the UK, where about half the beef supply comes from suckler herds, continental abattoirs derive a much greater share of their beef from the dairy herd. And, with the number of milking cows continuing to shrink in response to higher milk yields and more people quitting the industry, the availability of cow beef and veal calves will decline.
Conversely, suckler cow numbers have been more stable in recent years, in response to stronger demand for quality product and the continuation of coupled supports in some countries, such as France and Spain. Some member states have also used their “national envelopes” to encourage quality beef production and retain farmers in upland areas.
Despite this, the EU Commission estimates that the EU’s production deficit will grow steadily, from about 500,000t this year to nearer 600,000t in 2010, increasing the dependency on imports.
So long as consumption is maintained as many economies head into recession, EU prices are expected to continue to hold up well.
Watch our video: Philip Clarke on the global beef trade
Asia and Oceania
Australia is the world’s second biggest exporter, after Brazil, and therefore holds the key to much of what goes on in the global market.
The bulk of its trade is with Japan, which demands extremely high animal health standards, though it also exports significant volumes to the USA and South Korea. A smaller quantity also heads to Europe and there is a busy live export market to the Middle East.
Australian beef production has been hit in recent times by the continuing drought, which has limited the availability of cattle. And with feed prices climbing steeply in 2007 and 2008, many Australian feedlots are operating at well below capacity.
Recent estimates by the US department of agriculture suggest that Australian beef production will drop 1% in 2009 to just over 2m tonnes. As a result of this exports are likely to be down 3%, though this may be offset by a weaker Au$, which makes Australian beef more competitive.
New Zealand is the other main exporter in this region, mostly to the USA. Again the USDA is looking at reduced production in 2009, with beef exports expected to be 4% down.
On the demand side, the region still has huge potential, with consumption of beef on the increase in the key population centres of India and China. China is generally self-sufficient in beef, with consumption put at just 4kg/head compared with 18kg/head in the UK. As incomes and population grow, imports of beef could take off.
South America
Brazil is the big one, and again the picture of falling supplies and rising prices has characterised the beef trade in 2008. But the breeding herd is now on the increase and more surplus beef for export will follow.
To a great extent the EU market has been protected from Brazilian beef this year, due to restrictions imposed by Brussels following foot-and-mouth concerns. Trade is expected to be about 70% down on the 496,000t exported in 2007.
But the number of farms approved by the EU Commission for export continues to grow – it now stands at about 500 – and shipments to the EU are expected to grow again, though probably not until the second half of next year.
![]() |
---|
World beef trade flows – click image to enlarge (PDF) |
The weakness of Brazil’s currency – the real – could also boost exports. And while, Russia has absorbed much of the beef diverted from the EU in 2008, that trade could get more difficult as the Russian authorities seek to protect their own producers.
Increased supplies of Brazilian beef to the EU – especially Holland, Italy, Germany and the UK – seem inevitable next year.
The other main player in South America is Argentina. Supplies to the world market this year have dropped 25% as the government in Buenos Aeries has imposed export quotas and export taxes – a move which has prompted numerous farmer demonstrations.
With Argentineans eating their way through a massive 70kg of beef per capita each year, and with the government desperate to keep a lid on inflation, there is little prospect of Argentina returning as a major player to the world market any time soon.
North America
Beef production in the USA tends to be cyclical and, if anything, 2008 should have seen an upturn. But higher feed costs and a contraction of the dairy herd, plus the effects of drought in some key states, have stymied this recovery.
Demand for beef is still strong and, as a result, the USA has remained a net importer of beef, especially live animals from Canada and chilled meat from Australia.
Despite this, the USDA is now starting to see a recovery in its weekly slaughterings and is anticipating strong growth in exports next year, dominated by sales to Canada and Mexico. More top quality cuts will also be destined for Japan and South Korea as those markets open up following previous BSE issues with the USA.
Some analysts have predicted that the USA will become a net exporter of beef again by 2010. But this could be optimistic given the effects of the worldwide financial crisis on demand in certain key markets and the strengthening of the US$.
The bioethanol situation is also important, as this will effect feed prices in the USA, with large quantities of maize going to fuel plants rather than feedlots. The price of feed may be falling just now in response to the bumper world grain harvest, but that may be a short-lived phenomenon.