Streamlining harvest operations helps cut costs
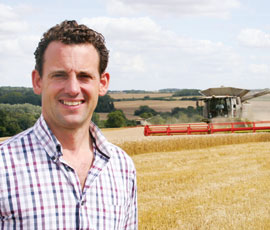
A radical reorganisation of harvesting operations for a large arable farming estate in Suffolk aims to trim costs by 5%, make managing the process easier and minimise its impact on the local community.
Until last year, the 4,480ha of crops grown on the Thurlow Estate was divided into three individual farm units. But the retirement of one of three managers overseeing day-to-day operations presented the opportunity to amalgamate and organise things on a bigger scale.
“We have land in three distinct blocks, but none more than eight miles away from our central wheat store, so the estate is quite compact for its size,” says farms director Andrew Crossley. “Instead of each farm unit harvesting with a combine, three tractors and trailers plus occasional HGVs, we’ve run all three combines together with chaser bins and lorries hauling grain.”
The same approach is being used for post-harvest cultivations for the first time following a 400-lot farm sale run by Cheffins earlier this year. That event dispersed nine tractors from 180-310hp, three self-propelled sprayers and the same number of telehandlers, along with trailers, 3-4m cultivators and 6m drills to make way for a new fleet operating on 40m tramlines.
Now, three Case IH STX Quadtracs work together on primary cultivations with 6m Simba SLD tine and disc cultivators, hitting one block of land at a time to prepare plenty of ground for secondary cultivations and sowing to be managed in the same way.
A pair of hired John Deere 8360RT tracked tractors prepare seed-beds using a 10m Simba Cultipress tillage tool each; two 8m Väderstad Rapid disc seeders and an 8m Horsch Sprinter tine drill provide a choice of coulter types to suit different crops, soil types and conditions.
“Having machines working together rather than scattered about makes it so much easier to rationalise and organise everything,” says Mr Crossley. “The operators can travel to fields in one vehicle, they can help each other with moves if necessary, and a fuel bowser can be sent to just one place too.”
For harvest operations, the combine drivers have had to gel as a team having previously worked independently; the one who has worked the fields before takes the lead to capitalise on their experience of field layouts and potential hazards.
To give capacity a lift over the wheeled Lexion 600s used previously, the harvest team has run Claas Lexion 770s on tracks this year. Equipped with GPS Pilot steering, yield mapping, telemetry and the Cemos interactive settings system, the operators have been through a bit of a learning curve, getting to grips with the technology while working in the same field without getting in each other’s way.
“Having machines working together rather than scattered about makes it so much easier to rationalise and organise everything.”
Andrew Crossley
“In theory, one combine should peel off and cut the headlands for the next field while the other two are finishing off so they can come in and start cutting out their own blocks,” explains Mr Crossley. “It doesn’t always work out that way – it depends on the location of the next field and the transfer point for loading the lorries; but I think it’s best to let the drivers work it out together without too much interference.”
Circular routes between fields and the 23,000t wheat store at the heart of the estate are planned to avoid outgoing and incoming lorries meeting head on along narrow lanes. A contractor has created new tracks and existing tracks have been improved where access was poor.
“We wanted to be sure lorries could come in empty at one end and go out full at the other,” says Mr Crossley. “There’s a lot more work to do to make the system sing, but the money we spend on these tracks will also improve access and travel speeds for equipment and bowser backup for spraying, drilling and fertiliser spreading, so all operations benefit.”
But why use lorries when the estate already had a serviceable fleet of trailers?
“Lorries are designed to haul big loads on the road, tractors are not,” Mr Crossley replies. “The main objective was to simplify transportation and reduce costs, but we’re also conscious of the estate’s place in the local community and wanted to move our crops into store as safely and with as little impact as possible.”
Conventional trailers continue to play a part, taking oilseed rape to the two 3,000t stores used for the crop and hauling about 4,000t of grain into the main store from close fields that can be reached without travelling on the road.
The estate withheld from sale its five best Richard Western trailers equipped with rollover sheets, hydraulic tailgates and commercial axles; these have been upgraded with larger flotation tyres and will have air braking for 2013.
Trailers are kept on standby in the area to take off the occasional load when the new haulage system has not quite gone to plan.
But otherwise this task is solely in the hands of three 40cu m Richard Western GR30 chaser bins and a fleet of between two and five lorries (more likely seven in a higher-yielding year) supplied by Coopers Transport, Braintree.
“Flexibility is another advantage of using lorries because we only draw down as many as are needed on a particular day, whereas with trailers you’ve got them, plus a tractor and driver, whether you need them or not,” Mr Crossley points out. “Coopers have a pretty good idea what we’ll need two or three days ahead, but we confirm that only the day before and they haven’t let us down once.”
Drivers were given a pre-harvest tour of the estate to familiarise themselves with loading sites and routes, and two-way radios so they can communicate with the harvest team.
Inevitably, there were still some teething troubles with drivers unsure where to go, but mostly things have gone smoothly as the drivers have got used to where the land holdings are and how the harvesting team functions.
In the field, the 30t capacity of the chaser bins provides a lorry load in one go; mostly, they receive grain from each of the combines in turn, so it is important for correct sequencing that no more than two of the Lexions need emptying at the same time.
This approach can involve a fair bit of running about as the bins move from one combine to the next; it’s helpful if the combine operators do not get too far apart when cutting out their own blocks to keep out of each other’s way.
The impact of the big bins on the soil is mitigated by encouraging drivers to use tramlines and tracks where possible and by the generous running gear – triple axles carrying 800/45 R 26.5 Vredestein Flotation Pro radial tyres.
Hauling these leviathans is not for the faint hearted or the reckless. With 30t of grain added to the 9.25t mass of the bin and 10t of Case IH Magnum, the operator is in charge of a 50t combination with a lot of inertia, so air brakes are essential. One full-time operator takes the lead here, alongside two returning harvest students; next year, they could have live combine grain tank data via telemetry.
“This is a very responsible and skilled job,” Mr Crossley emphasises. “Apart from the safety considerations it’s important that the bin is filled accurately to put a full load on the lorry.”
To make that easier, remote cameras were installed in the bin and on the spout mid-season so the drivers can see the final stages of filling and transfer – otherwise, they have to do it by instinct or outside guidance.
“Ideally, we want the combine driver to concentrate on his job and not have lorry drivers needing to climb their trailers to oversee loading,” he adds.
As further lessons are learned this year, more tweaks and refinements will no doubt be made. There are already plans to increase block cropping, which will consolidate the oilseed rape from seven locations to four. Another job is to establish a lorry loading point for every half dozen fields or so and make sure there is sufficient hard standing in places where yards or concrete beet pads are unavailable for lorries to get in, turn and get out again with ease.
“It’s taken a lot of thought and planning, and also a fair bit of investment offset by halving our tractor fleet, selling a lot of machines and reducing harvest seasonal labour from nine to four people,” says Mr Crossley.
Keep up with the latest farm machinery news