Australian farmer leads robotic spray revolution
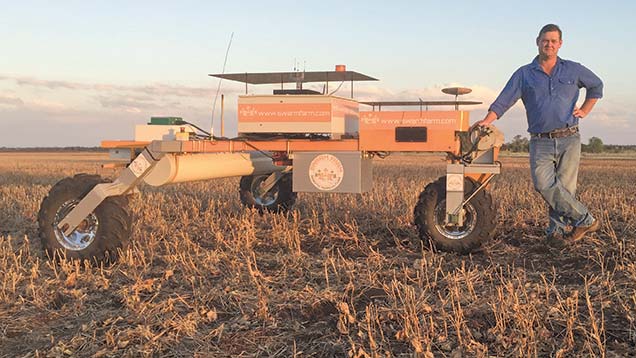
Legions of small robots trundling across fields killing weeds with lasers sounds like science fiction, but the reality is getting closer.
Queensland farmer Andrew Bate has spent the last six years developing a prototype robotic weeder that he hopes to trial commercially on his 8,100ha farm operation later this year.
His start-up company, SwarmFarm, has been working with the University of Sydney’s Australian Centre for Field Robotics (ACFR) and Queensland University Technology to pioneer the system, which Mr Bate believes offers a more efficient way of growing crops using simple lightweight machines.
“A lot of people think of robots as complicated machines with lots of moving parts and complex electrical systems, but our vision is for simple robots that do simple tasks very well.”
See also: Agronomists essential to get the most out of robots
Weighing around 200kg, the robots are considerably lighter than modern machinery at 10-15t, reducing compaction and allowing a wider window for field operations. They are also more nimble, allowing treatment of individual plants, rather than a broad-acre approach, he says.
“Saving labour is not the driving force. It’s about achieving optimum crop growth and doing it more efficiently.”
Indeed, it was Mr Bate’s frustration at falling productivity, a plateau in agricultural technology and worsening problems with herbicide-resistant weeds that prompted him to look for a novel solution.
Field applications
The field robot is being developed for targeted herbicide application, although it could be used for other low-power field operations, such as spraying and spreading fertiliser, Mr Bate says.
Alternative systems to kill weeds, such as microwaves, steam, or mechanical instruments to pull them out could follow.
“It is the ability of robots to slow down, stop at individual plants and treat them down to leaf level that really makes the difference. Robots will allow absolute accuracy and precision operations to be done with the same repeatable accuracy in the field.”
They are not designed for high horsepower-heavy jobs, such as ploughing, planting or deep cultivations, he notes. “We are not trying to automate what we are already doing. I believe the concept of a driverless tractor is already obsolete.”
3D View
The control system uses stereo (dual) cameras to generate a 3D view of the surroundings to detect obstacles and track crop rows.
GPS is used, but is not relied on as the main navigation, Mr Bate says. “Crop rows are often not exactly straight so the robot needs to adapt and follow the rows with the stereo camera system.”
Other navigation sensors are fitted that cross-check against each other to improve reliability and provide a back-up in case one sensor fails or gives an erroneous reading.
Power is from an electric drive with high-efficiency lithium-ion batteries delivering a six-hour working time per charge. A diesel-powered prototype is also planned.
Specialist WEEDit detection technology is used to identify and spot spray weeds and the robot has a 200-litre tank on board.
Multi-robot co-ordination software is used to calculate the best way to cover fields and sends each robot to work a specific area. “It is adaptable so that if one robot breaks down or is slower due to heavy weed infestations, the other robots re-plan their assigned area, so all robots finish the field at the same time and no areas are missed.”
Robots can detect obstacles such as trees, rocks, humans, other machines or animals in the field, driving around them to keep going.
Practical challenges
Mr Bate says dust is the main issue as it limits camera vision. However, alternative sensors, such as radar, would help overcome this.
The six-hour battery life is another limitation. Solar-powered robots are possible; however, large panels atop a lightweight vehicle could be unstable in windy conditions, he says.
Solar-powered robots are also limited to low-power fieldwork and can only work during daylight. “A better option may be to use a fixed solar array on the edge of the field to charge batteries, and have the robots dock with an automated battery swap-out system when they run low on power.”
Timescale
Mr Bate is refining the system to make the software and hardware reliable in the field.
The docking and refilling system was successfully tested in February proving autonomous refilling of herbicide on to the robot, allowing 24/7 operation.
He expects Australian farmers to be first to adopt the technology due to the lack of subsidy support, constant drought risk and exposure to world markets forcing farmers to find new ways of improving efficiency.
“In the next 12 months there will be early stage robots operating commercially in fields in Australia. There will only be a few early adopters using them and it will be several years before robots are ready to be fully commercialised to the stage that farmers can buy them.”