Farming Families – The Awdes of Cumbria
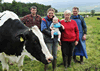
There can’t be many farming families that have gone through such turbulent times as the Awdes, yet they have never wavered in their commitment to milk production, or doubted their ability to live and work in harmony with each other.
Today, the Awde family milk 400 dairy cows in a new, purpose-built set-up that many other producers can only dream about. Trevor and Frances share the farmhouse with daughter, Lynsey (25), who manages the herd, and son, Francis (27), who takes care of field operations and cattle feeding. Meanwhile, nephew Matthew Mackay (23) has worked at Broadmeadows since leaving agricultural college.
The farm has not always run so smoothly. A series of events around 2001 has been instrumental in shaping its future.
The first catastrophe was foot-and-mouth disease, which wiped out all the livestock and left the business with virtually no income for almost a year. Prior to the disease outbreak, the farm carried 250 milkers, 50 suckler cows and 1000 ewes.
Next came the tragic death of son David, who was killed by a truck as he walked back to the farm after a night out. David had been responsible for most of the machinery work and the running of the small contracting business.
Around the same time, the family was served notice to quit the non-hereditary tenancy of the farm, which is near Penrith in Cumbria. They already owned 323ha (800 acres), and opted to put their foot-and-mouth disease compensation money towards buying the rest of the property, which now totals 485ha (1200 acres). They also decided to specialise in milk production, and increase the size of the herd.
While all family members are flexible in their attitude to work, there is a fairly clear division of labour. Francis and Matthew manage the 200 acres of arable land and the grass between them, as well as the cattle feeding. They have also retained some of the contract work, mostly silage making and drilling.
Trevor usually milks with his daughter and full-time cowman, Chris Cork. Frances, who used to have responsibility for the calves, now concentrates mainly on looking after her family.
Last Christmas, Lynsey gave birth to a baby boy, whom she named David in remembrance of her brother. Lynsey rarely misses a milking and has overall responsibility for the cows, as well as the farm paperwork.
“I don’t mind managing the accounts, it’s a job that fell to me when my grandad died,” says Lynsey. “Nobody outside the family would have such a vested interest in the business. It was a bit of a struggle when I computerised all the records, but now the system is up and running, it’s fairly easy to deal with.”
Every Monday, Wednesday and Friday, Lynsey’s uncle, Alan Awde, comes to lend a hand. His contribution is invaluable, and consists mostly of pushing young David’s pram around the farm. He has become an expert at bottle-feeding, although he draws the line at changing nappies, laughs Lynsey.
The family’s preference for self-sufficiency also extends to its eating habits. All their beef is home-produced. Dairy cows that are not used for breeding replacements are put to the Aberdeen Angus bull, with calves finished at 26-28 months. The beef herd is usually outwintered on one of the five separate blocks of land that make up the farm’s acreage.
There are also a couple of sows, and a small flock of geese. Recently, four pedigree Aberdeen Angus cows have been purchased, with the aim of producing a good-quality stock bull for the future.
Although some farming families in the region chose not to re-stock following foot-and-mouth, going out of milk was never a serious option for the Awdes.
“The farm felt very strange without livestock, and none of us were happy,” says Lynsey. “We were very keen to re-stock, but it took a little longer because we had to wait before being allowed to import cows from Holland. We had a pedigree Dutch herd before, and that type of animal suits our system better than any other.”
Lynsey takes enormous pride in her dairy cows and it is obvious that their welfare is a priority. The buildings are in immaculate condition, and the 50-point rotary parlour is spotless – and it’s here where young David’s pram is generally parked while Lynsey is milking.
Other signs of her high level of stockmanship range from the non-slip rubber matting in the parlour, to the tip-over water troughs, which are emptied and thoroughly cleaned out once a month. The passages are much wider than average, designed to give the two groups of cows plenty of freedom to move around, and to reduce bullying.
“Dad thinks we should perhaps be milking 500 cows,” says Lynsey. “We have the capacity, but I don’t want have to compromise on welfare because the herd is too large to manage effectively. Maybe we will expand further in the future, but that would probably mean employing another member of staff.
“At the moment, I think the number is just about right. There are always three of us on hand during milking. We don’t rush to get finished, because we consider it a good time to observe the cows and make sure they are all performing to the best of their ability.
“It would be nice to think that young David will be milking with me in 15 years’ time, but we’ll have to wait and see. Dairy cows require huge commitment, and there’s no point in trying to influence him if it turns out that his heart isn’t in it.”
The dairy herd has been on a mixed-ration feeding system for some years, with concentrates offered as a top-up in the parlour. Recently, the concentrate element has been removed, in an effort to save on feed costs. The move has not been entirely successful.
“The cows were averaging 12,500kg but, without concentrates, yields dropped to 10,500-11,000. We are thinking of installing out-of-parlour feeders, which would give us control of individual diets and hopefully push yields back up,” says Lynsey.
Calving is all year round, and milk is stored in a 32,000kg silo before being picked up by Meadow Foods. The cows are fed for butterfat, which averages 4.3%, while proteins are around 3.23%. Over the past six months, the rolling average milk price has fluctuated between 26p and 28.5p/litre.
When asked whether any one person has overall control of the family business, all heads turn towards Trevor. Although he is pleased that his children are keen to work with him, he was determined to allow them to make their own career choices. This is largely because he left school with the idea of becoming a joiner, but was eventually put under pressure to work on the farm, which has been managed by his family since the end of the Second World War.
“The fact that my children want to keep the farm going for the next generation keeps me motivated,” says Trevor. “I wanted them to have good working conditions, and that was one reason why I went ahead with the development.
“Young people of their generation don’t seem to respond to parental pressure like I did. I think I made the right decision by leaving them to make up their minds for themselves.”
Lynsey describes her father as a progressive businessman, and says he is more of a risk-taker than her grandad, Fred. Trevor has his own ideas on the subject.
“Like many farming families in the area, foot-and-mouth made us think hard about our business and the direction we wanted to go in,” he says. “In my father’s day, it wouldn’t have been possible to borrow the money for such a major project, even though farming was probably more profitable back then.”
Trevor used some of his spare time when the farm was stockless to evaluate the farm’s regular expenditure. The review led to him placing his custom with a different bank and changing his accountant and his solicitor.
“That was something my father would never had done, but these days loyalty sometimes comes at a high price,” says Trevor. “When margins are tight, it pays to look for savings on inputs, and that means shopping around.”
Trevor admits to having some sleepless nights while the new cattle housing was being erected, especially when costs rose 30% above the original budget. The final bill, to be paid off over 15 years, amounted to an investment of £3500-£4000/cow.
“I did wonder if we were doing the right thing, but of course by that stage it was impossible to turn back. We have laid the foundations for a business that should still be around for future generations to enjoy. It does mean working long hours, but it’s not really such a bad life,” he concludes.