Improved storage brings efficiency
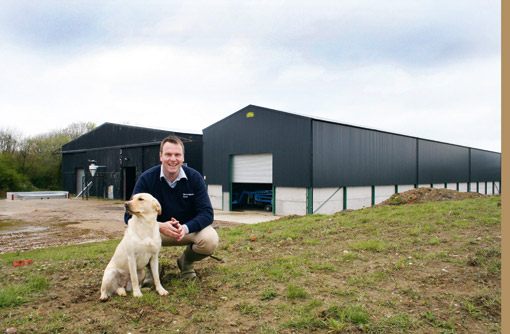
Nice as it is to build a new grain store to improve facilities for drying and storing crops, making the best of what’s already available can overcome deficiencies at considerably less cost. That was the option open to Joe Scott, farm manager for The Co-operative Farms, when he was given the task of managing Rockingham Castle Farms in Leicestershire 18 months ago. “I discovered there was no grain dryer, which meant combining could only be done when crops were dry enough in the field,” he recalls. “And with grain and oilseed rape kept in two stores some distance apart, the telehandler was often in the wrong place for loading lorries.” His solution, financed jointly by The Co-operative Farms and Rockingham Castle Farm, was to upgrade one of the existing stores with a dryer and conveyor filling system, and add a multi-purpose building alongside for crop and machinery storage with workshop facilities. This will not only make best use of combining capacity and in-store crop management, but also consolidate operations from three locations across the 1,200ha estate into one, and release the second storage building for alternative use. The focus of the project is not the prettiest of buildings at present, but with a new insulated roof, freshly-laid concrete aprons and a lick of paint, the former hangar on an airfield once used to train Wellington Bomber crews will make a tidy facility. “It’s a big, solid building, 75m long by 40m wide,” says Mr Scott. “Even with space taken up by the new dryer and a 300t wet grain area formed by free-standing grain walls, we can store up to 7,500t of wheat in here.” Rapeseed and/or grain as required will go into the new building just completed alongside; it’s 20m wide, but just as long and as tall as the hangar, for pleasing aesthetics as much as anything. Roller shutter doors at each end ensure flexible use of the space. Instead of being tipped, shovelled and pushed up into the hangar store, crops are now received by a trench intake conveyor as the first element of an 80t/hour Kongskilde handling system calculated to have enough capacity to cope with incoming grain at harvest. “Although we’re running two combines capable of cutting 120-140t/hour in ideal conditions, we won’t be drying much grain when they’re running at peak output,” Mr Scott points out. “And with 500t a day drying capacity, we’ll soon catch up with drying the damper grain cut in the mornings and evenings.” Besides, one of the harvesters will at times be used on two other farms managed by Mr Scott, at Ashby St Ledgers in Warwickshire and another in Rutland. Increased block cropping will help keep the two machines working efficiently. “The plan is to run them together through the oilseed rape across all three farms, ending up at our Ashby unit where they can move on to the milling wheat we grow there,” Mr Scott explains. “They’ll then split to tackle the feed wheat here at Rockingham and on the other two units separately, before coming together again to finish the job here.” Grain entering the store passes through an in-line aspirated cleaner before being elevated to either the GrainTek Tornado 4-30 continuous flow dryer or to a Kongskilde BCB 80-belt conveyor and taken straight into storage. Suspended beneath the ridge and running the full length of the building, the conveyor has a remote control motorised tripper to discharge grain to either side. Extensions being added this year will throw grain down the centre of each half of the store to make levelling off easier. “We decided to sacrifice some storage space by putting the dryer inside the building, even though height constraints mean it’s squat and wide, sitting on a 7.2m subframe,” notes Mr Scott. “But security can be an issue here and I like the idea of this investment being protected from the weather.” The touch-screen panel that provides fingertip management of the entire handling and drying system is an ultra-modern touch in the elderly building. Its colour display is produced by GrainTek’s electronics arm in Scotland and can be accessed remotely for fault diagnostics and software updates. Tapping individual numerical displays enables quick setting changes to be made and automated sequence start-ups for the dryer and handling equipment need nothing more than a light touch on the functions menu. GrainTek’s Tornado mixed flow dryer, produced by a team with extensive Law-Denis experience, features an insulated hot air plenum and drying column to minimise heat loss. Power consumption is optimised by using a variable speed fan, with scope to prevent lifting off light crops and provide fast cooling for maximum output. “Past experience of the back-up service that GrainTek provides made it obvious who to consult for the store upgrade,” says Mr Scott. “It worked well for the short time it was available to us last year Ð but I’m really looking forward to getting the full benefit of all the work we’re doing to make harvest a more efficient and productive process. “Mind you,” he adds. “I’d love a harvest where we don’t actually use the dryer very much.”