Managing moisture is vital to your premiums
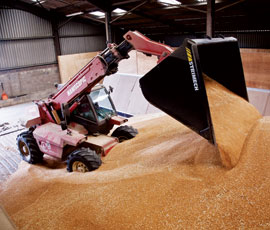
The store is clean and trailers are ready. Combines have started to roll between the showers and suddenly there are heaps of wet grain and the dryer can’t cope.
Successfully managing this moist grain and oilseed is vital in preventing spoilage by fungi and mites, leading to the loss of vital premiums.
The key is prioritising grain destined for the food and drink sector, namely milling wheat and malting barley.
“Know your market and handle grain accordingly, says Rob Sanderson, Openfield’s head of Central Storage. “Test and then dry crops quickly to preserve quality.”
The aim is to reduce the moisture content to less than 14.5% and the grain temperature to 10C or less to prevent mould growth, mycotoxin formation and taint.
Wheat and barley coming in at or above 18% moisture should be dried immediately. Grain below 18% can be stored temporarily and dried within the safe time.
The safe time depends on grain temperature, so reducing the temperature can help growers buy some time. This is because at temperatures greater than 15C, the risk of mite and insect populations increases.
Cooling
“When storing grain temporarily, where it is not normally stored, getting air through the heap is imperative,” says Ian Clayton-Bailey, sales director for Martin Lishman.
Grain aeration spears are an effective tool when it comes to getting some air through the heap and cooling grain. “Using a spear will at least get air through the grain and hold it stable until you can get it through the drier,” adds Mr Clayton-Bailey.
Growers using continuous flow driers (CFD) to reduce grain moisture by 4-5% will inevitably make the grain hot. Many CFDs have a cooling option to bring the grain temperature down after drying, but this can slow down dryer output.
“Our solution would be to use pedestal dryers to cool the grain after drying, thus maximising the output from the CFD,” says Mr Clayton-Bailey.
Drying floors
Where growers are using drying floors there are several ways to boost their efficiency. Monitoring relative humidity (RH) is one way, as it affects the ability of the air to dry the grain, he says.
Damp air will not increase grain moisture, but can reduce drying system efficiency if it enters the grain. If ambient air is drier than the stored crop then it can dry it.
So by measuring ambient relative humidity and grain moisture content, growers can decide whether fans can dry the grain using ambient air or whether some heat is needed.
Another way to improve drying floor efficiency is using automatic controls. An automatically adjustable fan takes into account air temperature and relative humidity so that the best opportunities are not missed.
“Energy is expensive so using an automatic fan controller will also make the best use of air temperature and relative humidity,” says Mr Clayton-Bailey.
Growers must be mindful of grain depth when filling their stores during a wet harvest, because manufacturers gear their fan size to store capacity.
“So to avoid exceeding the fans’ capacity you must make allowances when drying grain above 20%,” says Mr Clayton-Bailey.
“For example if the grain walling is 2.8m deep you will need to reduce the height by 0.5m for every percentage point above 20%. Failure to do this will result in poor airflow and slow the drying process. Depth of grain is dependent on air flow – where there is poor aeration don’t store it so deep. It is imperative to get air through it while waiting to dry the grain, says Mr Clayton-Bailey.
Rapeseed has a much higher resistance to airflow than cereals. If using an aeration system designed for conventional cereal storage it is necessary to reduce the bed depth by 50-70% if storing rape.
Oilseed rape storage failures could prove costly
With oilseed rape prices exceeding ÂŁ380/t, there is much to lose in getting rapeseed storage wrong. Richard Elsdon, technical manager at United Oilseeds, offers some tips.
Rob Sanderson’s top tips for storage
- Identify premium crops, dry and cool accordingly
- Test and dry premium crops quickly after combining to preserve quality, particularly milling wheat and malting barley
- Just as important for feed crops
- If using a continuous flow dryer, use a pedestal fan to get temperature down rather than the dryer
- A good benchmark is less than 15C and 15% moisture
- Check crops regularly
- Monitor temperature and track moistures coming off the dryer
- On ventilated floors, monitor regularly to ensure moisture is falling
- Best indicator is your nose – if you smell something sweet you have a problem
- If you have good Hagbergs, keep heat low to preserve quality
- For malting barley, the maximum safe burner temperature is 65C with a maximum grain temperature of 40C
If the crop is very wet, above 15%, it’s capable of heating up overnight.
This heat is generated by micro-organisms using the oil as an energy source and it will reduce the overall oil content of the crop and reduce its value. If left at a high temperature, the oilseed will become rancid – which is an expensive problem to resolve.
Both these can be avoided by drying and then cooling the crop immediately after it’s combined.
But guard against complacency. There’s often a temptation to assume that once the dry crop comes off the drier, it’s now safe. However there may still be an issue.
Even the most effective dryer cannot lower the temperature of the outgoing crop below about 2-3C above the ambient temperature of the day it’s dried. For example, if the temperature is 23C, the crop is likely to register 25-26C once dried.
The next consideration is the long-term cooling of the crop. Some growers assume that hot August temperatures make cooling impossible. Not so.
Even in August, the overnight temperature will drop to 14-16C, enabling some cooling to take place. Admittedly, the temperatures soon rise again during the day and this is when a differential thermostat should be deployed.
A differential thermostat simply compares the temperature 30cm below the surface of the heap of crop (the hottest point) with the ambient air temperature outside the store and controls the cooling fan as appropriate.
When the outside temperature is below that inside the crop (often 3C) the cooling fan automatically switches on until cooled. As the differential thermometer measures the temperature difference at very short intervals, it can grab cool air whenever it’s available throughout the night.
However, manual checking is essential to ensure the system is working and that air is passing evenly throughout the entire crop.
Walking a stored crop weekly and recording the temperatures across the bin is good practice. This can be done with high-tech probes wired back to a central recording computer or by inserting a 15mm copper pipe, with the lower end crimped over, into which a thermometer is inserted.
For ease of extraction, tie some string to the end of the thermometer long enough to lie on the surface outside the pipe. Pull out the thermometer and record the temperature. Then lower the thermometer back to the bottom of the pipe and leave it there until the following week.
You’ll need several thermometers to gauge temperature across the heap accurately, but they should last several seasons and will provide you with an essential indication of what’s happening inside your stored crop. If you have a temperature probe, use that instead, but always record in the same area each time.
Walking the crop has one more advantage. We all know that dry oilseed rape is difficult to walk over as your feet tend to sink in to it – usually by up to 15cm. Should you discover an area of the crop where your feet don’t sink in or penetrate, then you have a problem that requires investigation.
It may be a dust cone, an area of high admixture or where localised heating has occurred.