Mobile grain processor for the 21st century
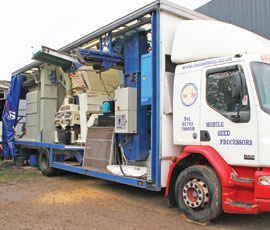
Getting in the mobile processor to clean up your seed may be one of the traditions of harvest, but it’s becoming distinctly hi-tech.
According to Dick Bowler, co-director of Stafford-based ReSo Seeds, as many as 85% of growers use the services of mobile seed processors to clean and treat their grain.
Dick runs a fleet of eight ÂŁ250,000 units which service farms within a 100-mile radius of the company’s Haughton headquarters. Annual seed cleaning and dressing accounts for 8,000t, while grain cleaning adds another 20,000t.
“We assemble all our units ourselves using components we source from various manufacturers,” he explains. “And the staff who put them together are also involved in using them on the farms.”
Three-phase electricity for the whole unit is provided by a diesel-powered generator. Grain is augured to the rear of the unit, then passed through a double-aspirated, twin-screen cleaner.
This removes under- and over-sized grain along with soil, sand, partially threshed heads and a significant percentages of wild oats and sterile brome. A de-awner unit removes the chaff and barley awns.
The grain then moves on to a gravity table, which is able to separate seeds and impurities that have a very slight difference in size and weight.
Next, it passes across a sieve set at a shallow angle while a controlled amount of air is blown up through it. This prevents the lighter grains falling until they reach the end of the sieve area, but is not enough to stop the heavier grains dropping through.
And now comes the tricky bit – how to separate unwanted objects that have an identical size and density as the grain being processed.
For wheat this means having a system that can remove ergot as well as stones. This is difficult because the size and weight of ergot mimics that of wheat or barley grains, making it very difficult to screen using conventional air/sieve systems.
So the third stage in the cleaning sequence is to use a scanning system that identifies ergot and automatically removes it.
Currently fitted to just one of the company’s eight grain-processing lorries, these units require the grain to be channelled down a series of chutes to flatten out the flow so that the colour spectrum projected behind it can be read by a camera. When an ergot is identified, a blast of high-pressure air is triggered to blast it out of the flow of grain.
“It’s a fascinating system which is just so clever,” says Mr Bowler. “The ability to remove ergot enables us to offer a bulk grain cleaning service which helps to keep us working throughout the year – beyond the peak seed cleaning zones.”
When seed is being processed, the grain is taken off the colour spectrometer and provided with a dressing which can be selected by the customer to meet specific local problems.
“Along with a range of dressings to provide seedling protection against disease and pests, we can also apply manganese and other trace elements to avoid problems with early deficiencies,” he explains. “It’s the customer’s choice and one of the benefits of having farm-saved seed.”
If it’s a bulk grain cleaning job – reducing the amount of screenings from malting barley, removing admixture from oilseed rape or the extracting of ergot from wheat, for example – the grain is diverted to a conveyor which offloads it into a trailer. Dressed seed is normally loaded into half or 1t bags.
In terms of costs, Mr Bowler points out that while being less expensive than merchant-supplied seed, the specific cost depends largely on the volume of work required and the distance the lorry has to travel.
“Clearly, travelling a long distance to treat a couple of tonnes of seed is going to be a more expensive job than processing a larger tonnage closer to home,” he says. “We generally charge by the tonne for seed and by the hour when bulk cleaning. The customer also has the farm saved seed royalties to pay, which we collect and pass on to the plant breeder.”