Nozzle classifying catches up with spray technology
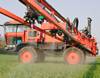
It is 25 years since British Crop Protection Council introduced the current classification system for sprayer nozzles. Since then the system, which classifies nozzles according to droplet size – very fine, fine, medium, coarse and very coarse – has remained unchanged, yet spraying technology and nozzle design have moved on immensely.
But things are set to change within the next three years, according to Paul Miller from TAG’s Silsoe Spray Applications Unit. A LINK project as part of The Sustainable Arable LINK programme, scheduled to start this autumn, will aim to reclassify nozzles to take account of the differences in efficacy and drift between all types – new and old.
“The BCPC system has worked really well in the past while we were dealing with conventional nozzles that were essentially using the same principles to generate the same forms of spray,” says Prof Miller. “But the emergence of twin fluid designs such as Airtec and AirJet nozzles and a few years later, air induction nozzles, means we really need to give farmers better guidance on when they can use these types of nozzles.”
The existing HGCA nozzle selection chart (available at www.hgca.com) goes some way to doing this, and for the first time this year, it has recognised that not all air induction nozzles are the same by including separate columns for “finer” and “coarser” droplet size distributions from air induction nozzles, he says. “It’s a step in the right direction, but the new classification really needs to build on this.”
So where’s the problem?
Classifying nozzles on the basis of droplet size is a simple method that can provide a rough indication of the likely efficacy and drift risk for conventional nozzle designs, says Prof Miller. “Fine sprays mean you’ll probably get good coverage, but drift may be an issue, while coarse sprays probably reduce drift, but give poorer coverage. Medium sprays are probably good for most things.”
But it is not always the case, he warns. Air induction nozzles – which account for 25-50% of the market – produce large droplets that include an air bubble within the droplets. This means they will behave differently to similar sized droplets from a conventional nozzle, he explains. “They will travel more slowly, have less inertia and effectively have a shock absorber built in them. You don’t always get the efficacy penalty associated with large diameter conventional coarse sprays – particularly from growth stage 31 in cereals and onwards.”
How will the system change?
The new classification system will take more account of the differences in efficacy and drift, for all droplet sizes and types, Prof Miller says. “For example, we may end up with a system that classifies nozzles using terms like ‘medium spray – medium drift risk’, or ‘medium spray – low drift risk’.”
This will be based on laboratory and wind tunnel testing at facilities such as TAG’s Application Unit at Silsoe, backed up by field trials, he notes. “We’ve got to find a way of giving farmers all the information in a way that’s not too confusing. Clever spray operators are probably asking a lot of these questions already, but for others, it will make them think more.”
The project will also focus on the characteristics of other nozzle types, such as spinning discs and some cone nozzles, which can produce significantly different droplet size distributions from conventional nozzles. “All this makes the system more robust and helps farmers choose what’s most appropriate.”
Getting the best out of nozzles
Matching nozzle choice to the appropriate chemical, growth stage, water volume, forward speed and boom height are crucial, Prof Miller says. “If you’re a cereal farmer, then from growth stage 32 onwards, it’s likely that air induction nozzles are going to be a good choice for many spray applications.”
By late spring, it is mainly fungicides that will be applied, so air induction nozzles will work well, he says. But for small targets, such as applying herbicides to grass weeds in the autumn or early spring, then a finer spray and better coverage are needed and these are best delivered by conventional flat fan nozzles, he suggests. The application of some pre-emergence herbicides may also need a finer spray, although this needs more investigation, he says.
He advises growers to avoid using air induction nozzles at too low a pressure, unless the nozzle is specifically designed to do so – such as some extended range/variable pressure types. “Most air induction or flat fan nozzles run at 2-4 bar. Don’t operate them too close to the bottom of the pressure limit – if you do, you won’t get a uniform distribution under the boom.”
The new classification system will account for the different drift characteristics and droplet size distributions from extended range/variable pressure nozzles, particularly in comparison with conventional designs, Prof Miller notes.
NOZZLE CLASSIFICATION |
---|
|