Save CIPC with sensible sprout suppressant use
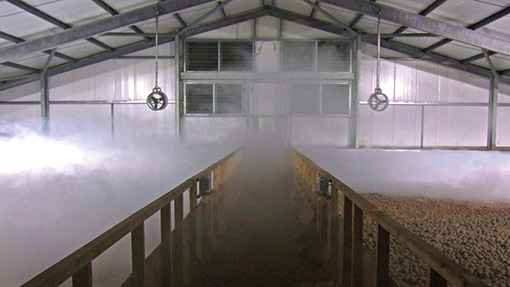
Potato sprout suppressant chlorpropham (CIPC) has long been under scrutiny, with a wide range of human health concerns prompting tighter use.
Earlier this summer, the Potato Industry CIPC Stewardship Group announced even tougher rules for growers, with a clear subtext – “use it wisely, or lose it”.
The latest pressure stemmed from a further exceedance of the maximum residue level (MRL) in a box store of crop intended for the fish-and-chip shop trade. While alternative strategies are being developed alongside lower doses of CIPC, a ban would cause real problems.
“Any exceedance now could trigger CIPC’s withdrawal from use, which would have a profound effect on our industry,” says NFU horticulture adviser Lee Abbey.
Stewardship group
The Potato Industry CIPC Stewardship Group includes all CIPC approval holders (Aceto Agricultural Chemicals Corporation, Certis, DormFresh and United Phosphorus), AHDB Potato Council, Potato Processors Association, Fresh Potato Suppliers Association, National Association of Agricultural Contractors (NAAC), National Farmers Union (NFU), Red Tractor Farm Assurance, Sutton Bridge CSR and Cranfield University.
See also: Cover crops to control potato cyst nematodes
“If you use CIPC, check and adhere to the statutory conditions of use and, now more than ever, it is critical that users follow best practice.”
About half of all stored crops are treated with CIPC, since failure to control sprouts usually leads to rejection, especially in processing crops.
But stores are a case of “islands of excellence in a sea of mediocrity”, warns Potato Council director Rob Clayton. “When we travel around the country, we find an industry blissfully sleepwalking into situations that put our mainstay sprout suppressants at risk.
“We find growers content to sacrifice airflows – and CIPC effectiveness – to squeeze 1,100t into a 1,000t store.” That must change, and quickly, he insists.
Statutory changes
Red Tractor
New Red Tractor farm assurance criteria mean CIPC can only be used in stores that have been pre-audited for factors affecting distribution and performance, including location, structural integrity, relative crop volume and uniformity of temperature control. Use of a non-Basis adviser is now a critical failure point. Application equipment must be inspected and certified annually.
The total CIPC dose permitted has been slashed to 30g/t for fresh and 58g/t for processing potatoes (including fish-and-chip shop supplies), explains Pamela Foster of Aceto Agricultural Chemicals Corporation.
Furthermore, the maximum individual dose has been cut to 18g/t and the minimum interval between application and sale for consumption or processing is now 14 days.
CIPC approval holders, as part of their stewardship process, requested the changes. They also strongly recommend just one application in low-temperature stores (5C or less), which should be made before the store temperature drops below 7C.
Other best practice measures in the “Be CIPC Compliant” campaign are set to become statutory requirements on product labels, says Adrian Briddon, secretary of the Potato Industry CIPC Stewardship Group. Much of it was incorporated into Red Tractor standards earlier this year (see panel).
CIPC best practice
- Adhere to new guidelines
- Demonstrate least use
- Complete Red Tractor checklist before treatment
- Apply early to clean crops with set skin
- Treat before sprouts visible
- Store by variety/dormancy
- Use Basis adviser recommendation after in-store crop inspection
- NAAC-approved application
- Recirculate store air for six to twelve hours before application to ensure even temperature
- Bypass fridge coils during application
- Avoid application to part-filled stores and part treatment of full stores
- Do not apply in windy conditions
- Don’t be too eager to reapply
- Avoid cross-contamination of stores used for non-potato crops
- See www.cipccompliant.co.uk
Ensuring even CIPC application is key to avoid residue “hotspots” and deliver effective sprout control throughout the store, so follow-up treatment is less necessary.
That is relatively easy in bulk stores. “About half of GB tonnage is held in bulk stores with inverters fitted,” says Mr Briddon.
“The inverters slow fans to allow CIPC fog to be circulated throughout the store during application. This reduces over- and under-application, ensuring sprout control is good and that residues are below the MRL.” Inverters cost about £3/t over 10 years, but energy savings should recoup that.
Box store focus
Box stores are more challenging. “Most box stores are of the overhead throw type, and without corrective action, there is an increased risk of higher residue levels occurring. CIPC should be applied via an enclosed duct [plenum] to prevent fog rising into the store headspace,” says Mr Briddon.
At the Storage 2020 conference earlier this year, Paul Coleman, technical director at Greenvale AP, showed some low-cost approaches.
Installing an air divider sheet prevents air short-circuiting back to the fridge system; inverters cut fan speed and suck air (and CIPC) through boxes, with sponges placed in alternate box openings at either end of the store to achieve a forced airflow through every box. Residue checks in a demo store showed more even CIPC distribution than in an adjacent passive store, where samples from four top boxes exceeded the MRL.
After a hot, bright summer, crops are expected to be particularly prone to early sprouting, so early and effective CIPC application will be vital.
‘If we lost CIPC it would be a disaster’
Adam Palmer farms 1,620ha of mainly black fen soils in partnership with his family, operating from Stowbridge Farm at Streatham, near Cambridge. His prime responsibility is the potatoes, and with 12,000t of Piper, Agria and Markies stored at 8-10C as late as June for the chip shop trade, CIPC’s future must be preserved, he says.
Purpose-built box stores are optimised for air circulation, but adding variable-speed fans with inverters to slow airflow and improve distribution three years ago helped halve CIPC use from 14g/t to 7g/t for every treatment. “Inverters use less electricity and reduce dehydration, so they pay for themselves in a year, before any CIPC saving,” he says.
Storing clean crops in quality boxes and keeping a steady temperature helps, as does separating varieties. “Markies need less suppression than Piper, so we don’t want them being treated in the same store when they don’t need it.”
Mr Palmer monitors crops closely for the first signs of eyes opening before reapplication. “Some people apply CIPC routinely, every 30 days. I prefer to watch the crop and only treat when needed.”
CIPC alternatives don’t look too promising, he adds. “Alone they don’t seem to do the job – more research is clearly needed. But if we lost CIPC it would be a disaster.”
Andrew Chennells farms in partnership with brothers Michael and Patrick as GH Chennells (Farms) in Lincolnshire. The 1,800ha arable operation is a member of Leaf and grows processing potatoes for crisping. As part of a Potato Council project, the Farmers Weekly Green Energy Award finalist reduced CIPC applications in bulk stores by up to 50% by running fans at 15% during application.