Video: PepsiCo helps growers cut their carbon footprint
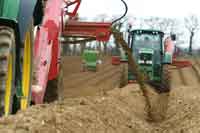
Growers supplying potatoes for Walkers crisps are being issued guidelines on best practice to cut carbon and water use on farm. Mike Abram takes a closer look.
Reducing the carbon footprint of a bag of Walkers crisps has been a target for PepsiCo since 2007, when it first measured the footprint of the while process in conjunction with the Carbon Trust, says Mark Pettigrew, PepsiCo’s agricultural development manager.
A lot of the carbon footprint lay upstream of potato production. For example, transport carbon emissions account for 10%, while cooking and processing a further 24%, but 34% came directly from growing potatoes and sunflowers to make the oil the crisps are cooked in.
That means the firm wants to work closely with its 350 farmers to reduce emissions and water to reduce its impact on the environment.
And it has set a tough target for its potato growers: Halve carbon emissions and water use in five years.
The starting point has been trying to establish a baseline for where carbon emissions occur on farm, and how much water is used. To do that, PepsiCo has invested in the development of tools to measure, record and help cut emissions.
The Cool Farm Tool, developed in conjunction with the University of Aberdeen and Unilever, is an easy-to-use computer software that measures on-farm carbon emissions, Mr Pettigrew says.
An Excel spreadsheet, it requires growers to enter data such as electricity use on farm, pesticide and fertiliser use, and how much diesel has been used by machinery.
Testing using real 2009 farm data from Shropshire grower Robin Griffiths suggested the calculator gave a level of carbon dioxide equivalent emissions similar to those previously found in life-cycle analyses conducted by PE International on two potato farms for PepsiCo.
Feedback from Mr Griffiths also helped make the calculator more farmer-friendly and focused for potato growers, Mr Pettigrew says.
Last season, 24 growers were invited to record their carbon footprints using the model, with the average (without measuring emissions from storage) being 95kg CO2e/t of raw potatoes. But the farms ranged from 60 to 132kg CO2e/t, Mr Pettigrew says.
“We are reviewing the data with all the growers to try to understand why there is the variation. But this allows us to look at operations that have not been separated out before.”
The tool has also been central in helping identify the potential emission savings from best practices compiled by ADAS and Denis Buckley, an independent consultant. Those practices include techniques to optimise fertiliser use, such as taking account of soil nitrogen supply and matching nitrogen use to canopy needs, and maximising yields through good crop protection.
But the two suggestions that could have the biggest impact are maximising yield through variety choice (see box) and minimising energy use per tonne of potatoes. The latter needs growers to record the fuel used for each operation, whether that is planting, spraying or harvesting, or indeed the fuel needed to drive an irrigation pump.
The idea is to build up evidence of energy use by operation to allow future improvement. Based on example data, a 10% improvement in efficiency potentially could save 4kg CO2e/t or 3.6%.
Potential savings through best practice in store have also been highlighted by Adrian Cunnington, of the Potato Council, and Farm Energy’s Tim Pratt, and organised into four categories, according to their ease of implementation and cost.
Low-cost, easy-to-implement measures, such as checking the main duct for leaks and cleaning fans, could be simply achieved by following the Potato Council’s store management guide. Putting into practice all the priority-one measures could reduce energy use by 15%.
Of the measures that require more time, carrying out an energy audit once every five years is important to keep track of changes being made, while best practice will require a high level of investment to re-insulate stores and make a strategic change to energy supply by installing a wind turbine. But energy reductions of up to 57% could be possible.
Both sets of suggestions have been discussed at grower group workshops, says Mr Pettigrew, with the next step being the implementation of a carbon management plan on each farm to focus growers on actions to decrease greenhouse gas emissions.
The plan will give details of the farm’s current carbon footprint from the data gathered by the Cool Farm Tool, where the farm could improve and planned actions to minimise emissions.
Low-carbon fertiliser trials
Fertiliser production accounts for around 26% of the potato production carbon footprint, so Spearhead International, which supplies 60,000t of potatoes to PepsiCo a year, is trialling a low-carbon fertiliser manufactured by Yara.
Containing the same level of nitrogen as conventional fertiliser, it is made in a more efficient way, cutting the carbon used by about 12-15%, says Spearhead’s David Almond.
“And from what we’ve seen so far in trials alongside our standard fertiliser, the yield and quality produced is no different.”
Both Spearhead and PepsiCo hope to increase the use of low-carbon fertiliser next season, but the price does have to be right.
Variety focus
Introducing new higher-yielding varieties that require less nitrogen fertiliser and use water more efficiently is high on PepsiCo’s list of targets to meet its 50 in five target.
The firm has run a variety improvement programme for about 20 years, says Mr Pettigrew, which resulted in Record being replaced by Saturna, Lady Rosetta and Hermes to improve crisp quality, yields and sugar stability in store.
“Now we’ve started our own proprietary variety programme, with the aim of growing 85% of our varieties in five years time.”
The benefit for growers should be a 10% improvement in yields, which will help cut carbon emissions, as well as growing varieties that require less water, nitrogen fertiliser or pesticides.
Carbon reduction priorities
• Maximising yield through variety choice
• Minimising field energy
• Optimising fertiliser use
Storage best practice options
• Cleaning, checking and maintenance of stores
• Carry out energy audit every five years
• Consider re-insulation
Water management priorities
• Irrigation operator training
• Using irrigation scheduling
• Record water use accurately