How infra-red beak trimming for layers works
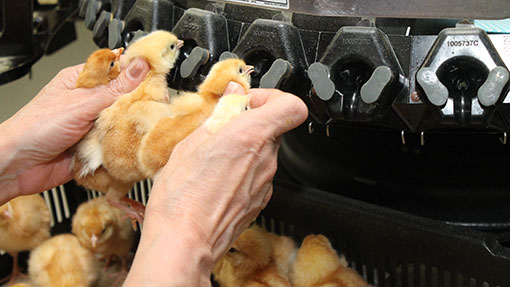
To some people, infrared beak trimming (IRBT) of day-old chicks is a mutilation – an abuse of a living creature that causes pain and disfigurement that is as unnecessary as it is unpleasant.
To others – and that includes the vast majority of the British egg industry that operate at the sharp end (no pun intended) – it is a high-tech solution to a potentially far worse welfare outcome.
The slight, short-term discomfort the chick may feel is nothing compared with the serious physical damage it would suffer should injurious feather pecking and cannibalism break out further down the line. The recent breakdowns in two of the flocks currently involved in the Bristol University trials into non-beak trimming prove the point, they say.
Whatever the arguments, there is no doubt that the IRBT system is a vast improvement on the hot blading that is still widely practiced on the Continent, but has been banned in the UK for several years. It is less intrusive and far more accurate, providing consistent results that the industry can count on.
Hatchery business Joice and Hill, a subsidiary of Hendrix Genetics, has been using IRBT for several years. Like all the other hatcheries in England, it uses machines manufactured by Nova-Tech Engineering, based in Minnesota, USA.
So what does the process actually involve?
The machines are known as Poultry Service Processors (PSPs) and Joice and Hill has five of them, located in a separate room just off the main sexing area. The PSPs perform three main functions: beak trimming, vaccinating and counting.
A box of about 100 female chicks is placed beside each machine and an operator loads them on, four at a time, with the upper part of their bodies supported by a unique rubber mount. The machine does a first count at this stage, keeping a running total of how many chicks have been placed on the PSP.
The first physical process is the infra-red beak treatment itself. Each chick’s beak is pushed forward into a highly reflective cylinder where a halogen bulb emits a single flash. The lens concentrates the beam, which is focused on to the tip of the beak, topside only. Air and water flows into the cylinder to cool the bulb.
One of these chicks has been ‘mutilated’, according to the letter of the law, having been subject to infra-red beak treatment. (It’s the one on the left.)
The infra-red beam penetrates the hard outer horn of the chick’s beak, altering a small area of the underlying dermis and sub-dermal tissue. One to three weeks later, the tissue behind the treated area heals and the beak tip drops off.
The intensity of the beam is fully adjustable and may be increased or decreased to account for the age of the breeder flock and differences in chick size. Typically, chicks from younger flocks receive a less intensive treatment.
The process takes less than a second, after which the machine retrieves the four chicks from the beak treatment position and moves them round clockwise to the vaccination position.
Vaccination involves a single needle coming down from above into the back of the chick’s neck to deliver whatever vaccine the customer requires. Almost invariably this will include a treatment for Marek’s disease.
Each plastic bag of vaccine contains enough for 2,000 doses and an alarm is sounded every 15 minutes to remind staff to agitate the vaccine bag. After 10 bags – or 20,000 treated chicks – it is time to change the needles and also to clean the lenses in the IRBT part. This is done typically five times a day.
A vaccine supervisor also checks the chicks every 20 minutes and after every flock change.
Once vaccinated, the batch of four chicks moves round again and is released down a chute, where they are counted again before being transferred into a fresh chick box. Once there are enough chicks in the container – typically 100, as determined by customer demand and welfare requirements – it is either moved off to the dispatch room, or on to another conveyor for an additional spray vaccination.
Nova-Tech says there are numerous advantages to the PSP system. The head holding feature produces superior repeatability and accuracy, while performing three processes at once reduces handling stress. Treatment procedures are also bloodless, greatly reducing infection, and because IRBT is performed immediately after hatching, biosecurity is enhanced.
Each machine processes on average 12,000 birds a day, and the chicks coming off look little different to those that go on to it, either in appearance or behaviour. The top of their beaks show the slightest discolouration, though this becomes more obvious over the next few days. There is certainly no head shaking, beak rubbing or whole body trembling.
In terms of behaviour, Australian research in 2008 suggests IBRT chicks have a reduced pecking strength, indicating some pain and discomfort, possibly caused by neuromas. But other research – in particular that performed by Glasgow University in 2009 – concluded that this pain is not chronic and has no adverse effect on sensory function.
The cost of beak trimming chicks using this technology is put at about 3-3.5p/bird.
Monitoring and training
While the PSP machine is a pretty sophisticated piece of kit, the monitoring of its performance is just as impressive.
Every action to every chick is fed back via the internet to Nova-Tech Engineering’s headquarters at the MinnWest Technology Campus, Willmar, Minnesota, and the company sends a weekly performance report back to Joice and Hill, summarising how the machines are doing, confirming how many chicks have been treated and any errors that may have occurred.
The report also confirms the beam intensity levels used over the period, the lamp air temperature and the motor current – and advises if anything needs to be recalibrated.
Should a more major problem occur at any point in time, that machine can be switched off remotely from the USA. But on the rare occasions when this might be necessary, for example if a bulb goes, the machine itself will already have given an alarm, with a red flashing light.
A control panel on the wall will of the IRBT room at Joice and Hill also provides staff with a record of how the system is performing and will notify them of any errors, for example a dirty lens or if the head holder is not picking up that there is a chick there.
As well as distance monitoring, Nova-Tech comes over from the USA for a site visit and audit twice a year. Joice and Hill currently holds a silver proficiency certificate – one of the highest accolades . The company also assesses and trains staff in operating the machines.
Nova-Tech facts
Nova-Tech was established in 1992 as a two-man band in Willmar, Minnesota, aimed at “leveraging emerging technology to benefit agriculture”. After rapid growth over the last 19 years, it now holds seven US patents and employs over 100 staff. Its equipment can be found in over 250 hatcheries in more than 30 countries and six continents around the world.
- Nova-Tech was established in 1992 as a two-man band in Willmar, Minnesota, aimed at “leveraging emerging technology to benefit agriculture”. After rapid growth over the last 19 years, it now holds seven US patents and employs over 100 staff. Its equipment can be found in over 250 hatcheries in more than 30 countries and six continents around the world.
Expansion plan for Eye hatchery
Over £1.5m has been invested by Joice and Hill in its hatchery at Eye, Cambridgeshire, over the past year and a half, triggered by the company winning exclusive rights to hatch and distribute all Hendrix Genetics breeds in the UK in 2012.
The company has built an extension and added 12 ChickMaster A12 single stage setters to the 17 Jamesway multi-stage setters, each with a capacity for 64,500 eggs. The next phase will see the removal of the Jamesways, which are now 25 years old, to be replaced by another 10 ChickMasters.
“The Jamesways have served us well, but single-stage setting has several advantages in terms of efficiency and traceability,” says Joice and Hill’s Stephen Turner.
The business is also looking at alternative means of fumigating eggs, before they are put into the setters. “Formaldehyde has already been banned in the USA and we are pretty sure that one day it will be banned here.”
The investment has seen site capacity increase from about 10 million chicks a year to 12 million, and once the new setters are in, it will reach 15 million. The company targets one female chick for every 2.65 eggs set, after allowing for male chicks and mortality.