Feed compounder researching ways to reduce energy cost of poultry feed
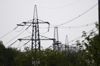
Research and investment is helping a feed compounder to offset some of the rising energy costs in the feed supply chain. Jimmy Birchmore explains how
Poultrymeat producers will need to receive an additional 1p/kg for their chicken to offset the increased energy costs in feed manufacture. Therefore, feed suppliers have a responsibility to ensure these increases are minimised by leading the way in researching supply chain efficiencies.
“ABN’s annual energy costs now amount to over £11m for electricity, gas and road fuel, following price increases of 63%, 54% and 29%, respectively over the last two years,” says the firm’s managing director Alan Murphy, “And of course, the company has needed to generate additional working capital to meet these cost rises.”
Such significant cost increases, experienced throughout the poultry industry, have met with a determined response from ABN. Capital investment, training and consideration of alternative fuels are all examples of the firm’s initiatives to minimise the impact on the supply chain, but research and development is at the heart of its long-term strategy.
“We are investing in inverter controls on 46 large motors across seven of our nine mills,” says Mr Murphy. “The inverters, which adjust the motor speed according to demand, will save enough energy to give full pay-back on capital spend after two years.
“Five of our sites will also see installation of reverse osmosis water plants, which generate higher quality steam for our pelleting operations. Measuring the cost per tonne of steam raised for each site also helps to keep us focused on spend,” he adds.
ABN views monitoring as essential to identify areas for energy saving. Half-hourly data for energy use is monitored when plants are shut down, with the aim to switch off mills when they are not in use and, where possible, priority is placed on high usage items such as boilers, compressors and lights.
The firm is looking to introduce alternative fuels by replacing gas oil with LPG on three of its sites and its plans to reduce transport fuel usage are already in full progress. “Ninety per cent of our finished feed is transported by our own team of 250 drivers, who have all completed our training programme designed to reduce vehicle idling and encourage more defensive driving,” continues Mr Murphy.
“We are now recruiting a full-time driver assessor to help monitor fuel usage on an ongoing basis and a vehicle tracking system has been fitted on all our vehicles to monitor fuel consumption.”
Feed form can also help, as highlighted by a major project initiated by poultry nutritionist Rob ten Doeschate, which led to recent changes in the grist size of raw material in the firm’s broiler feed.
“The aim was to investigate how altering the size of the raw material particles might improve broiler growth performance,” says Dr ten Doeschate. “The mills vary the way raw material is ground and our scientific trials have proven that, when a more coarsely ground raw material is used to make the pellet, bird performance is better – and easily offsets the sometimes slightly lower pellet quality.”
He explains that: “The coarser grist was found to help improve gizzard function and gut health, leading to greater feed digestibility for growing birds. This leads to improved growth performance and litter quality.
“There are direct cost savings to be made because less feed is required for the same output and, as a result, the transport costs of raw material and finished feed are reduced,” concludes Dr ten Doeschate.
Similarly, extensive scientific trials with layer feeds over recent years have investigated levels of dietary energy, amino acids and linoleic acids – all aiming to enhance understanding of laying hens’ nutritional requirements and continue to develop better diets for changing modern production systems and genotypes. The result is that new feed formulations have been developed to help producers achieve the best possible feed conversions.
Cost cutting
- Inverters cut fan motor power use
- Tight monitoring of power use
- Drivers taught to drive more defensively
- Coarser feed improves bird efficiency
Benefits of switching to coarser ground feed in pellets | |
Factor |
Change |
Liveweight at 35 days |
2.9% improvement |
Water:feed ratio |
7% reduction in water consumed/g of feed consumed |
Feed conversion ratio |
No significant difference |