Metal fuel tanks make a comeback
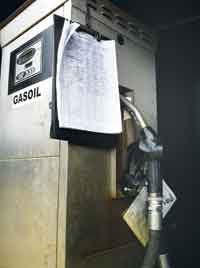
Often forgotten at the edge of the yard, fuel tanks rarely get any attention. Yet they’re vital to the smooth running of any farm, explains Emily Padfield
For Great Tew Estate, near Chipping Norton, Oxfordshire, the construction of a new grain store and machinery shed provided the perfect opportunity to overhaul the estate’s antiquated fuel storage system.
Previously, the estate had storage for a total of 20,000 litres in three single-skinned steel tanks with block wall bunding plus one 2000-litre tank for the drier. All were gravity fed, explains estate manager, Colin Woodward.
“One of the first objectives was to gain access to the 1p/litre savings that could be had from ordering fuel by the 36,000-litre artic load. So a 40,000 litre tank was a priority.”
It was also important to keep tabs on fuel use for each of the separate enterprises on the estate, which includes farm, quarry, shoot and property.
In the end, the decision was made to opt for two fully bunded steel tanks to current PPG2 regs; a 40,000 litre tank for the new grain drier and a 45,000-litre split tank for both red and derv diesel, supplied by Ledbury Welding and Engineering.
This 45,000-litre, fully-bunded fuel store holds both red and DERV diesel and had added features like electronic metering and overflow protection.
The new grain facility, run in partnership with Glencore, includes a 35,000t capacity grain store with a Svegma 60t/hr continuous flow drier. This serves not only the 800ha (2000 acres) of cropping on the estate but Glencore customers too.
“We did look at one tank that would be able to service drier, tractor and transport fuels. But because we use a specialist fuel for the drier that isn’t suitable for vehicles, we had to have two different tanks.”
The drier alone last year used in excess of 100,000 litres of diesel whereas the tank used for fuelling tractors and quarry equipment used in the region of 150,000 litres.
Now, only designated users with a key fob have access to the derv fuel tank, something Mr Woodward is keen to replicate for the red diesel tank, too. “It’s currently possible to allocate each litre to each separate enterprise. Fuel monitoring needn’t be overly complicated, you can opt for simple fuel-per-hour software.”
The fully bunded tanks are made of 5mm mild steel plate with a 150mm gap and a second 5mm layer of steel. The whole thing is protected by ex-motorway armco barriers to protect from any inadvertant knocks.
Another priority was security. “We were keen not to have padlocks – they’re too easy to get the bolt cutters round and can get rusty.” The new setup has a roller shutter door with pin locks that go straight through the shutter,” says Mr Woodward. All pumps, gauges and displays are integrated into the tank in a lit compartment at the front, secured also by the roller shutter.
It’s also fitted with an overflow warning system, whereby a probe in the tank triggers both an alarm and a flashing light should levels begin to rise to near the top. If it does overflow, fuel then goes into the bunded area.
It’s essential to have a constant-reading electronic gauge, says Ledbury’s sales manager Rob Young. “Having the overflow alarm may seem to be belt and braces, but it takes away the risk of overfilling.”
The red diesel tank is fitted with a Hytek 70litre/min pump and a 7.5m retractable hose reel. “It’s necessary to match the hose reel to the pump capacity,” explains Mr Young. “It’s no good if it can only deliver 20 litres/min. Each gets as standard 10 micron Cim-Tek fuel filters.”