Robust operations policy maximises wind and solar returns
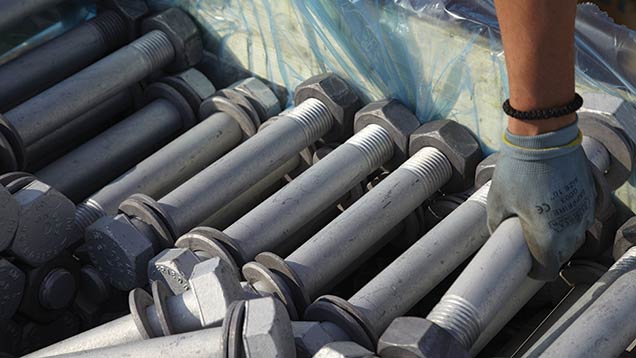
There are many different types of operation and maintenance (O&M) contracts and warranties on offer across the renewables sector.
While poring through the small print may seem tedious, good operation and maintenance of any wind or solar installation ensures returns from the original investment are maximised, says Strutt & Parker partner and senior engineer Kieran Crowe.
See also: Renewables get the foundations right
“As with any piece of equipment, prevention of problems is always better than cure, particularly with something like a wind turbine which is very mechanical. Solar PV is far simpler, but even so, inverters need maintaining and panels need looking after to get optimum output,” he says
Monitor performance
Accurate performance monitoring is the starting point for any good O&M policy, as this allows potential operational issues to be identified early, says Mr Crowe.
Most systems generate a wealth of data, so it is well worth contracting out monitoring to a third party in exchange for a relatively small annual fee – typically around £200 for a 50kW rooftop solar array, he says.
They are able to filter and interpret the data and send an alert via email or text when there is a concern. “Many people like to monitor systems themselves, which is fine, but don’t forget it’s a long-term commitment and there isn’t always time.”
A regular site visit by an engineer for scheduled maintenance is a simple yet useful part of any O&M contract as it allows potential issues to be identified that may not necessarily be picked up by data analysis alone, adds Gareth Goodall of consultant New Stream Renewables.
“Choosing an O&M provider is about finding a balance between keeping costs down and getting the best performance from your asset.”
Choosing a maintenance package
Shopping around for O&M providers can be well worth the effort, even though manufacturers or installers often insist they are best placed to maintain a particular installation, says Mr Goodall.
O&M questions to ask
- What is included – monitoring, maintenance, breakdowns, replacement parts?
- Anything not covered?
- How long is the contract?
- Cost? Is it fixed, linked to inflation, or likely to rise further?
- Is there an annual site visit or is an engineer only called in the event of a problem?
- Are parts and labour included?
- Is there a callout fee?
- What is the average response time and availability guarantee in the event of a breakdown?
- Do they have the necessary insurance and health & safety expertise – especially for working at height on turbines or rooftop solar?
- Check the company’s track record/references?
“There are many good independent [engineers] out there, often local to the area, so if you’re managing O&M yourself then recommendations and referrals are invaluable.”
O&M contracts are typically available for one, two, or five years and cost generally falls the longer the term, says Mr Crowe. “Two years is fairly common for solar, while wind O&M contracts are often nearer two to five years.”
Monitoring is the relatively inexpensive part, often charged at an annual rate of £200-400/electricity meter installed. “Service thereafter is the biggest cost and varies significantly depending on what’s included.”
For solar arrays up to 250kW, maintenance contracts (excluding replacement parts) typically cost £700-£1,000/year, while the standard range for wind turbines is 1.5-2% of the capital project cost, also excluding replacement parts, he says.
Continuous monitoring and annual maintenance is a must for wind turbines due to the number of moving parts and potential for problems, particularly the gearbox, he says.
A parts replacement policy may be worthwhile for wind, but is unlikely to have a great benefit on small solar PV systems, Mr Crowe continues. “Standard manufacturer warranties generally provide a decent level of replacement cover, typically at least five years for inverters and 10 years for panels.”
Before signing up to any additional O&M commitment, landowners need to be clear on exactly what is covered by the warranty, the warranty period and to ensure they have a certificate to prove start and end dates, he notes.
“The warranty period starts when the kit leaves the manufacturers shelf, not when it’s installed. It’s also worth making sure you have contact details for who to claim from in the event of a problem, whether a manufacturer or distributor, not just the installers details.”
The choice of O&M contract often depends on the level of risk the landowner wishes to take, although lenders tend to prefer an all-inclusive approach to secure the investment, says Diane Popa, head of UK sales at turbine manufacturer Vergnet.
“All-inclusive contracts cover the whole range of on-site and remote interventions and performance guarantees. Performance guarantees provide direct motivation for the O&M provider to maintain optimum turbine performance.
“Basic contracts on the other hand, offer a limited service, often excluding performance guarantees, and with additional services worked out on a cost-plus basis.”