6 expert tips for reducing dairy costs
As head of business consultancy at the Andersons Centre, Tony Evans is well versed in the latest production efficiencies, and well placed to employ them at the dairy he contract farms with partner Wil Armitage.
Last year the cost of production at Manor Farm, Thrussington, Leicestershire, was 20.22p/litre before rent and finance. This compares with an average of 28-30p/litre.
In the past few months he has reduced costs further, to less than 20p/litre before rent and finance, and he is continuing to look at areas on the farm where savings can be made.
See also: How record-keeping made Norway’s dairy herd world-class
Unless the business makes a £10,000-plus surplus then the farmers only receive a labour fee of £7,500/year as part of the contract agreement, so there’s a real drive to squeeze spending and maximise profitability.
While Mr Evans admits the industry is going through is a hugely challenging time and there is little that can be done to improve returns, he says there are steps that can be taken to reduce farm costs.
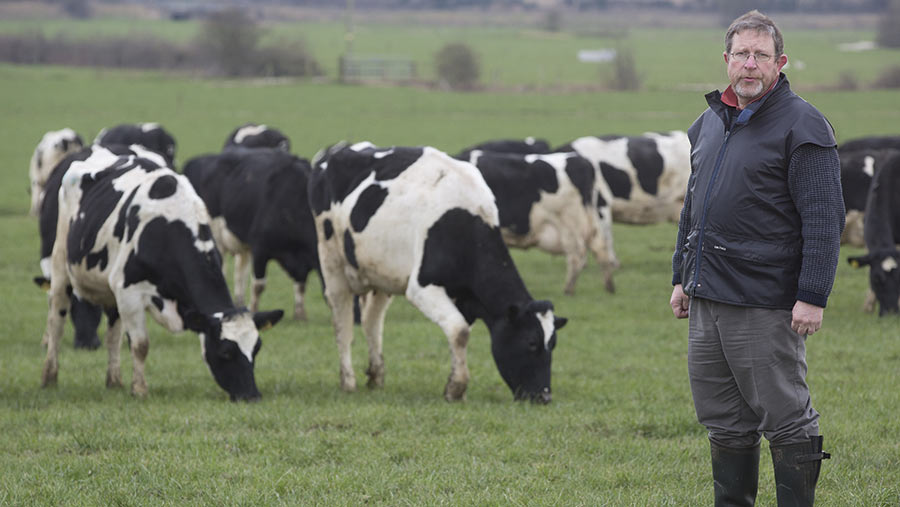
© Tim Scrivener
“The opportunity to reduce expenditure is good, and in our own hands. It is important for farmers to benefit from input prices that have fallen on the back of oil prices and falling demand.”
Farm facts
- Milk sold to Long Clawson
- About 120,000 litres/year processed on farm to produce Peter and Cheryl’s own-brand, award-winning Manor Farm yoghurt
- Tony and Wil own the company Farmrite, and have interests in another three farms
- Cows are milked twice daily through a 24:48 swingover parlour
- Farm totals 158ha: 135ha owned and 23ha rented
- The herd is split into one-third autumn calving and two-thirds spring calving, with cows calving in eight- and 10-week blocks
- Farmrite employs two full-time herdsmen and all major machinery operations are contracted in
In the past year, ammonium nitrate has fallen from £286/t to £218/t and concentrate prices have dropped from £210/t to £170/t, he explains.
Mr Evans estimates dairy farms can save 1.5-3p/litre from reduced inputs, with higher-cost systems benefiting most.
While this presents an opportunity to reduce spend beyond the farmgate, there are plenty of other areas on farm where costs can be reviewed, he says. Here he guides us through six of them.
1. Breeding
Maximise the number of calves born alive per 100 cows and heifers.
“We target one calf born alive to each cow. Reducing waste is the most valuable way to make money and the calves are a starting point.”
For Mr Evans, this also means managing waste to reduce purchased feed costs. Calves are fed whole milk.
If you are on a production limit contract, rather than produce the extra litres for a low return, Mr Evans recommends feeding this to calves and saving money on milk powder.
“But milk has got to be low disease risk,” warns Mr Evans, who adds buying a pasteuriser can reduce disease transmission.
Don’t rear more than what you require, he advises. At Manor Farm, they aim to rear 65 heifer replacements each year (22%).
Last year, 34 autumn calves were born, but the herd only needed 22 so the additional 12 were sold for £270 each.
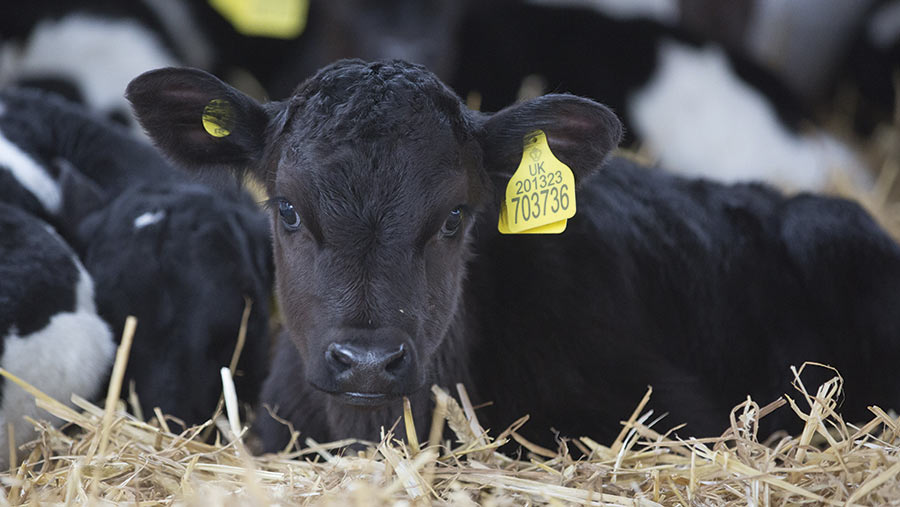
© Tim Scrivener
Consequently, they will save £450 on AI fees and serve for less time to replacements, which will make life simpler and easier for the two key employees.
This, together with changing the rearing policy, has helped to cut heifer-rearing costs by 1.15p/litre.
“We brought all our heifers home from contract rearing because we’ve made our system simpler and this has allowed us to increase our labour productivity.”
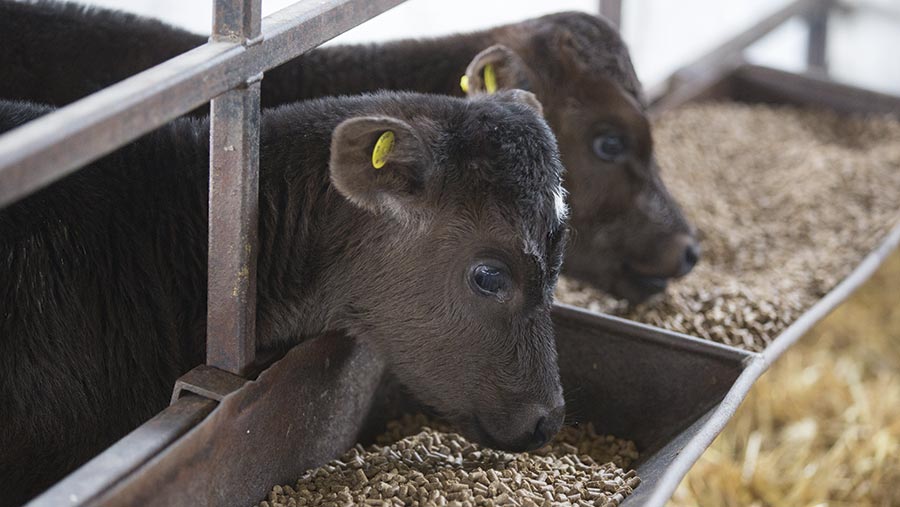
© Tim Scrivener
Now heifers are housed in rented sheds in the winter and are grazed on the home farm during the summer.
2. Calving pattern
Tightening the herd’s calving pattern has freed up staff to do other jobs, such as heifer rearing.
This year, 80% of the spring herd is on target to have calved within a six-week period.
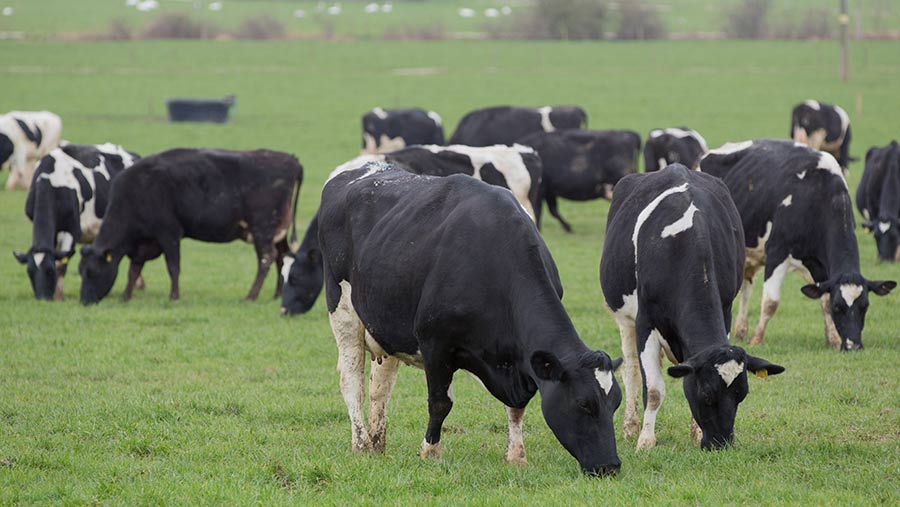
© Tim Scrivener
“Because we have our block much tighter, we can dry off spring calvers early so we are only milking our autumn calvers through the winter.
“That saves us 40 minutes each day because we are milking two rows less,” says Mr Evans.
3. The 10% challenge
Staff at Manor Farm have been set the challenge to reduce costs by 10%. One area where this has worked particularly well is in the parlour.
“We do a hot wash once a day now and we’ve reviewed chemical concentrations,” says Mr Evans. This has reduced daily chemical costs from £7.20/day to £2.78/day.
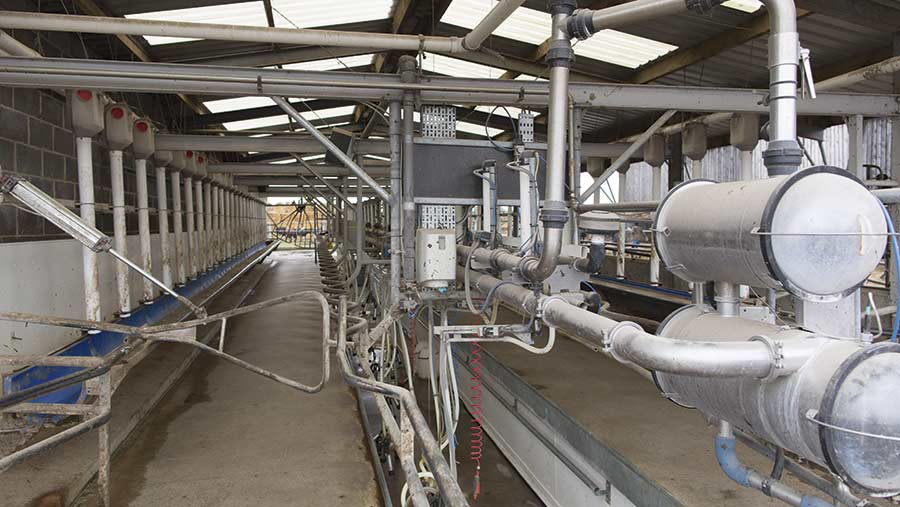
© Tim Scrivener
About the Manor Farm partnership
The 158ha farm is run on a 15-year contract agreement with farm owners Peter and Cheryl Holmes.
Prior to the partnership, Mr and Mrs Holmes milked 180 Friesians, producing an average 4,600 litres a cow a year.
But since the agreement was established eight years ago, cow numbers have expanded to 300 plus youngstock, and the breeding policy has been altered to include Jersey-cross and some New Zealand blood to make the most of the farm’s 75ha grazing platform.
“We [bulk] buy all our chemicals every six months as part of a buying group. Being a member of a well-run buying group saves us about £50 a cow a year.”
This adds up to about £15,000/year, which more than covers the group’s membership fee of £1,200.
The farm also put in a borehole eight years ago, which has seen their water bill drop from £12,000/year to £800/year, and they have moved from once-a-month milk recording to every other month, bringing the bill down by £90/month.
4. Feed
In-parlour feeding has been cut back 10% from 4kg a head a day to 3.6kg a head a day without negatively affecting yields, with the herd remaining on target to produce 6,000 litres this season at 8.5% solids.
Mr Evans believes minerals can be a “rip-off area” and says when it comes to their inclusion in rations, decisions should be taken based on facts.
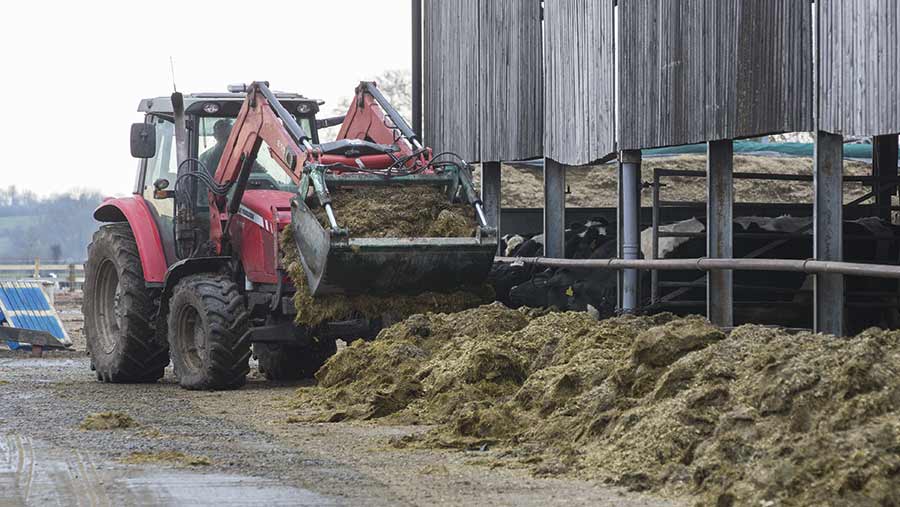
© Tim Scrivener
“Only feed for deficiency,” says Mr Evans, who has this year budgeted just £700 for minerals and, for dry cows, is looking to use only magnesium chloride in their water.
“So far we’ve had nearly 80% calve and we have used no more than three boluses and little calcium,” he adds.
5. Medicine use
While no corners are being cut that could jeopardise cow health, every effort is being made to reduce vet bills at Manor Farm.
Last year, vet and medicine costs were reduced by 21% to £35 a cow. One of the biggest money savers has been dry cow therapy.
Tony’s top tips for reducing your cost of production
- Find out how your cost of production can be reduced by looking over your accounts for the past three years and comparing them against comparable costs from AHDB and your discussion group
- Wherever possible go on visits to farms that will declare their hand – then listen, learn and have an open mind
- Challenge yourself to reduce your costs by at least 10% while the marketplace has moved by at least the same amount
“Historically we took a belt-and-braces approach and used antibiotics and a teat sealant. But now we are only using a sealant on cows with cell counts consistently lower than 180,000/ml.”
This year, just 40% of the herd received antibiotics at drying off, and at a cost of £7.50 a cow this has saved the farm £1,425.
“We are still vaccinating so we are not cutting any corners on animal health.”
The herd is fully vaccinated against BVD, IBR and lepto, but the focus has been on cutting back on small things and having faith in the ability of the stockmen.
“Generally we ask ourselves: why are we calling the vet? We don’t have any third party on the farm. We do our own foot-trimming, freeze branding and AI.”
So far, the vet bill for calving in February was just £46, and Mr Evans says that’s mainly down to the ability of herdsmen Lee and Matt, as well as Wil’s stockmanship guidelines and coaching.
6. Grazing v housing
At Manor Farm they are putting in 300m of concrete sleepers at a cost of £24/m to extend the grazing season.
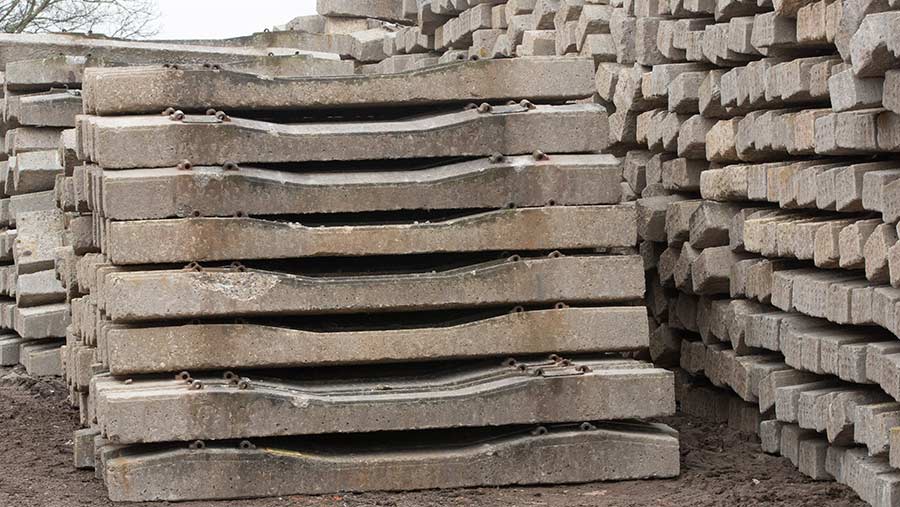
© Tim Scrivener
Mr Evans reckons it is an investment well worth making because it means he can halve his feed and bedding costs, with expenses falling from £2.70 a cow a day when cows are indoors to £1.34 a cow a day once they are out at grass.
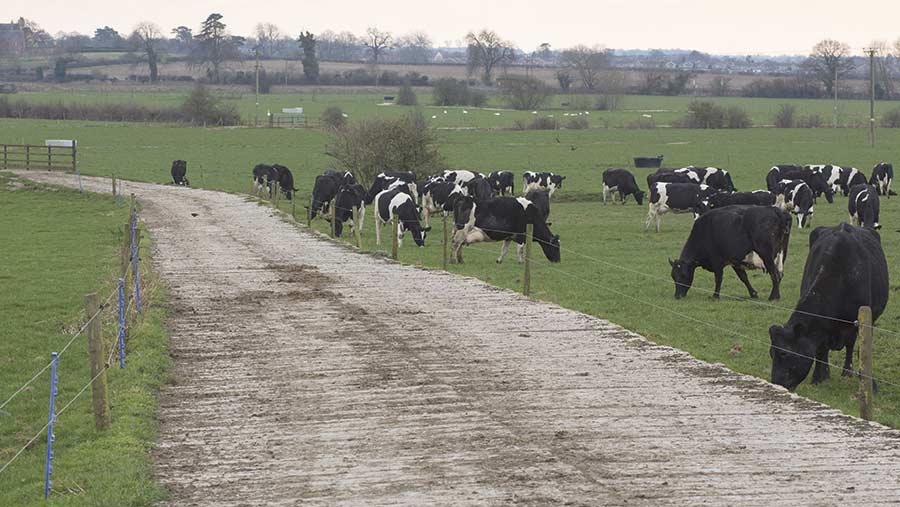
© Tim Scrivener
“The biggest challenge is to minimise winter length. A lot of costs fall away when the cows are outdoors.”
Several seasons ago, the farm switched from using EnviroBed to top up their rubber mats at a cost of £75/t to a gypsum-based product costing £19.50/t.
He says the key to saving money is shopping around to see what offers are available.
In numbers: The contract farming agreement
- ROC paid at the end of each financial year, to the value of £4,500, to Tony and Wil for the supply of all machinery.
- ROC each year for Peter and Cheryl on the £350,000 they invested at the start of the contract to renew the dairy facilities—this is written off over the 14 years of the agreement
- ROC on the £395,000 for Peter and Cheryl on the livestock, which they supply.
- £296/ha (£120/acre) “first charge” on the land and buildings supplied by Cheryl and Peter, plus a rent for the house that one of the Farmrite employee lives in.
- 50:50 split on the first £20,000 of the divisible surplus, with the remainder divided 80:20 in Tony and Wil’s favour. Last year’s divisible surplus was approaching £75,000 (4p/litre).