Automated feeder pays its way
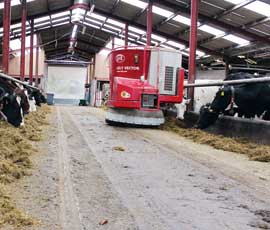
A fully automated cattle-feeding system is saving one dairy farming partnership £170 a month in tractor running costs alone and delivering a consistent ration to the herd.
John Rafferty, who farms with his father, Pat, at Poyntzpass, County Armagh, is trialling the Lely Vector, a robotic feeding system capable of feeding a Total Mixed Ration (TMR).
He is making savings on diesel and tractor running costs and his labour inputs are considerably lower. “The tractor we used for diet feeding is practically redundant, we are saving 250 litres of diesel a month from that alone,” says John Rafferty.
“We used to run the tractor for a couple of hours every single day, but we now use it only occasionally to chop straw.”
According to figures produced by Lely, the daily running costs of the Vector are 22% cheaper when compared to feeding manually from a wagon.
The Raffertys run a 135-cow dairy herd, yielding about 9,500 litres at 4% butterfat and 3.25% protein.
They had installed two milking robots and were keen to try the mixing and feeding robot to complement the automation.
The cows are housed in two sheds and split into four groups – two milking groups of high and low yielders, a pre-calving group and a dry cow group.
How it works
The Vector, which is stored in a purpose-built shed, is self-contained and battery-operated and can feed up to 300 animals. Forage is stored in a compartment known as the ‘feed kitchen’. A grabber mounted on a crane-type construction selects the forage in a pre-programmed order and drops it into the robot.
As the grab fills the vertical mixer, which has a capacity of 600kg, the Vector lightly mixes the ingredients. A concentrates dispenser monitors the feed quantities and small quantities of minerals and additives can be mixed with the concentrates. The machine is then programmed according to the feeding plan.
The mixer and distributor are guided along a pre-programmed route in the feed area, on metal strips set in the ground. Ultrasound sensors work out its location and distance from the barrier.
Aidan Fallon, Lely’s sales manager in Ireland, says the machine needs only a feed passage width of 3.25m. “The robot knows exactly how much feed there is and when it needs to be replenished,” he says. “It distributes feed at regular intervals and pushes the feed up to the barrier so that it is always fresh.”
Mr Fallon says the location is the most important consideration when installing the feed kitchen; it should be close to all the feeding sheds. “The closer the kitchen is to the animals, the shorter the planned route and greater the capacity of the machine,” he says.
Feed efficiency
At Poyntzpass, the machine has been trialled for four months and the Raffertys reckon feed efficiency has increased. Test farms in Holland have seen an average 5% improvement in feed efficiency.
Mr Rafferty says the system proved particularly relevant in a season when good quality forage is in short supply. “We can earmark our quality silages for the best cows. Our 52 highest-yielding cows are achieving a daily yield of 40 litres,” he explains.
“All the cows are adapting well. The more they eat, the more the robot will feed them.”
The ration, formulated by a nutritionist, includes silage, wholecrop, round bale silage, straw, yeast, minerals and an acid buffer.
Mr Rafferty says feeding little and often helps to stabilise pH levels in a cow’s stomach and cow health has improved under the new system. The lactating cows are fed six times during a 24-hour period and the two dry groups – the far-off and the pre-calvers – three times.
He has noticed that feed intake has increased significantly since he installed the Vector. During the early stages of the installation process, the feeding robot’s only work was to push up the feed every four hours and that alone increased feed intake by 6kg. Mr Rafferty believes the availability of fresh feed encourages the cows to eat more.
“The feed is fresh and well mixed and is delivered in consistent portions at regular intervals every day. It has had a positive impact on the herd’s performance and feeding habits.
“Dry matter intake has increased because feed is pushed up regularly and this enables the feeding robot to measure the feed height. The cows are responding by producing more milk and healthwise they are in great shape.”
Labour saving
A major benefit has been the number of hours saved on feeding. Filling the feed kitchen is the only manual task required in the entire feeding process.
The floor of the kitchen is marked out similar to a chessboard with the different forages, moist feeds and roughage placed in specific grids. The loading is planned to make the best use of the floor area and to avoid feed going stale.
The more expensive ingredients, such as vitamins and minerals, are stored in bins with electric augers, while up to 16 different roughage ingredients can be split into separate bays on the shed floor.
The Raffertys first bought a feeder wagon in 1998 and it took John Rafferty 14 hours a week to mix and feed the different rations. “I used to be in the tractor for two hours a day but now it is just twice a week, in the farm loadall, for about an hour and 15 minutes.
“When you feed manually you have to rely on someone coming in every day of the year and you want cows to get the same feed every day. Consistency is important and we find that the cows get that with the robot feeder.”
The Vector is pre-programmed to prepare and distribute the different combinations and volumes of rations and it also pushes up the forage on a regular basis. “I used to have to manually push forward the forage two or three times a day and also last thing at night,” says Mr Rafferty.
“The machine does all of that for us now so I have more time to do other jobs around the farm.”
At an average cost of £110,000, he says the Vector is viable for his system. “We are not being paid to trial the Vector, but we were offered it at a discounted price if we agreed to give feedback on it. In all honesty, it would be viable had we paid the full price, the cost savings really stack up.”
He believes the system could be beneficial to every dairy farm with a TMR system. “This type of technology makes the system so flexible. We are currently in the process of adding another route, which will allow the Vector to feed a batch of beef cattle in another part of the yard.”
The Lely Feed Kitchen – is it right for me?
Cost – £110,000 based on 150-cow herd
KEY CONSIDERATIONS
- The size of the kitchen – this will determine the amount of feed storage space available. Most feed kitchens can store enough feed for up to three days
- The kitchen can be a new build or existing farm sheds can be used to cut costs. The ‘gantry crane’, one of three different types of crane structures, is on wheels and can be used in existing sheds
- The structure of the kitchen will be determined by Lely engineers depending on what type of crane is used and the steel structure needed
COST BENEFITS OF INSTALLING VECTOR COMPARED TO FEEDER WAGON
Feeder wagon £15.72/day based on capital cost of £35,000
Three hours a day feeding at £15/hour – £45
Cost of diesel at £10/hour – £30
Total cost a day – £90.72
Vector – £49.40/day based on capital cost of £110,000 for 150 cows (this will vary up and down depending on the number of cows in system)
One hour a day managing the ‘feed kitchen’ at £15/hour – £15
Energy costs – £6.75/day
Total cost a day – £71.15
Farm details – Poyntzpass Farm
- 180 acres farmed including a 150-acre grazing platform
- Aim to produce 4,000 litres of milk from forage
- Herd calves from October to February
- Cows are milked through the robot three times a day
- Average lactation of 170 days
- Replacement heifers are all bred from sexed semen
Solar-powered feeder automatically doles out cake