Routine parlour tests and upkeep will pay dividends
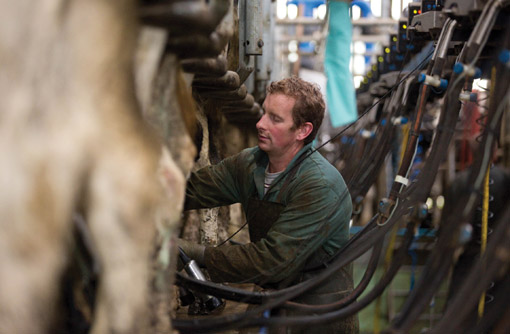
You are in the parlour with milking in full swing. The radio is on, the machine is working and cows are making the usual background noise. Against that environment how can you tell if pulsation is out and, if it is, which units are affected?
In a typical parlour, when just one pulsator is operating incorrectly then 9% of the herd will be incorrectly milked every single milking, or each cow risks being incorrectly milked once every five days.
Yet many farmers are prepared to risk cow health and performance by failing to maintain the machine properly by, for example, fitting lower quality spare parts, mixing liner types or deciding to save money by not investing in a milking machine test.
Maintenance and routine testing
Before cutting any costs, farmers need to ask themselves if cows might be affected and what the impact might be.
Failure to keep the milking plant operating effectively can have a big impact on cows, so routine testing and maintenance should be seen as an investment.
Our experience is that in most cases performance can be rectified by adjusting the machine rather than having to spend money. And when investment is required it is usually on a low scale and far less than the cost of not correcting the fault.
The Promar Milking Machine Testing service carries out more than 2,500 tests a year with a mixture of static tests, which take place between milkings, and dynamic tests, which involve testing the plant during a milking and also assessing the milking routine.
It is the largest independent milking machine testing service in the UK and recent analysis shows the frequency with which common problems occur (see table left).
The problem with shortcuts
It is staggering how often we see parlours where shortcuts have been taken. For example, where mixed diameter milk tubes have been fitted or a mix of milk liner types used because of availability or price.
These can all affect performance, but unless the machine is tested and matched, the problems will not be apparent until issues with cell counts and teat damage surface.
Problems can also arise when the configuration of the parlour is changed to increase efficiency, for example where a new vacuum pump is fitted or where the bore of pipework is increased.
“If just one pulsator is operating incorrectly then 9% of the herd will be incorrectly milked every single milking.”
The dynamics of milking involve the machine, the operator and the cows. Change any one of them and it is possible that problems might result. Regular testing and maintenance with the correct spare parts is essential to maximise the working life of the machine and the cows.
Teat end vacuum
One of the most common problems found in dynamic testing is incorrect teat end vacuum. While a static test tells you the vacuum level at the gauge, it tells you nothing about what vacuum levels are where it really matters, at the teat end.
The teat end vacuum level is responsible for extracting the milk. In all parlours there is a fall in vacuum between the vacuum gauge and the teat end, so the vacuum gauge is not a reliable indicator of what the cow is experiencing.
Ideally the teat end vacuum should be no more than 40kpa. When teat-end vacuum is too high it will cause erosion, leading to an increased risk of mastitis and irritation to the cow. Cows will become harder to milk and milking will take longer. When teat-end vacuum is too low then you may see an increase in unit slippage and extended milking times.
Every time the unit slips on the teat, air is drawn in at the side and this can drive bacteria from the teat surface back into the teat opening, increasing the risk of infection.
It also extends milking times and overall teat exposure to vacuum.
Problems often occur whenever a milking plant is changed in any way. For example, imagine you are milking in an old parlour where the teat-end vacuum was 35kpa and you then change the parlour configuration and as a result the teat end vacuum increases to 45kps. The impact will be increased pain and discomfort, teat-end damage and possibly an increase in cows trying to kick the units off, but the vacuum gauge would read the same.
The only way to assess teat-end vacuum and ensure the parlour is set up correctly is to have a dynamic milking machine test carried out.
Good milking routine is vital in preventing teat-end damage irrespective of how well the machine performs. When cows are not prepared correctly you can get a period when the machine is attached and there is no milk flow. The full vacuum is then applied to the teat end, causing irritation and damage in the same way as over-milking.
Automatic Cup Removers
A common finding in dynamic tests is that automatic cup removers (ACRs) stay on too long leading to over-milking. Many ACRs in the UK were initially designed to remove the unit when the flow rate fell below 200ml/minute. While this is fine for a cow yielding up to 7,000 litres, it is too low for a 10,000-litre cow where ideally the cluster needs removing once flow rate falls below 450ml/min. A unit staying on too long may result in teat-end damage and can extend milking times unnecessarily.
We have recently seen parlours where some of the ACRs have been replaced and the new ones are operating at a higher flow rate leading to inconsistency in milking routines. Simple adjustments soon correct this problem.
Compared with the cost of increased mastitis and extended milking times, the investment in a milking machine test combined with the use of approved parts designed for the particular parlour is a small price to pay.
Improving efficiency
Chris Corbett, Rectory Farm, Banbury
Improved milking efficiency and teat condition were the outcomes of a dynamic milking machine test at Rectory Farm, Epwell, Banbury, where the 280 cow herd is milked three times a day.
The 10,500-litre averaging herd are milked through a 28:28 low line parlour, which had been extended from a 20:20 a year ago.
With the move to three times milking we needed to increase cow flow and so extended the parlour, explains producer Chris Corbett.
“We now have two people covering every milking with a total team of five milkers,”
Mr Corbett has a static test carried out every year by his local dairy engineer and the parlour has always passed the test, but he agreed to have a dynamic test carried out as part of the DairyCo mastitis plan.
“We knew the plant seemed to be set up correctly, but the dynamic test would tell us more about how it actually operated and the interaction between the parlour, the cows and the milking team,” he says.
The test was carried out by Promar parlour consultant Rosina Monk and as a result several changes have been made. The biggest alteration has been modifications to the clusters. The milking claws have been replaced to ensure better positioning of the cluster on the udder and a V-shaped pipe hook has been fitted to each unit to help better support the weight of the cluster.
“By better positioning the claw we are getting more even milking and this, combined with changing to a different type of liner, has helped reduce slippage,” Mr Corbett explains.
“We were replacing all liners every 2,400 milkings so this was not an extra cost as we just changed makes at the next routine change.
“The dynamic test told us a lot more about how we were milking the cows and while the routine and the mechanics of the parlour were good, we have been able to make changes to improve the efficiency of milking, which would not have been shown up any other way.”
Overall improvements have resulted in reduced slippage and increasingly better teat-end condition, which has been marked in newly calved heifers.