Should you convert to sand bedding on your dairy?
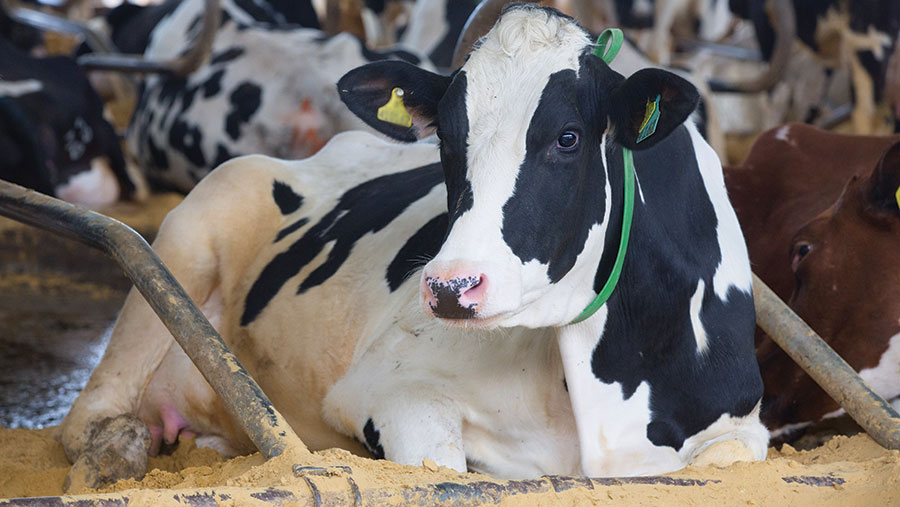
Sand is the gold standard when it comes to cow comfort and udder health, meaning that many farmers are looking at ways to upgrade from mats to sand bedding.
Its inert nature means sand harbours less mastitis causing pathogens, and also helps to keep cows clean and comfortable – all of which combine to aid health and lying times.
See also:Â Slurry separation options compared
Consultant, Andy Dodd from The Farm Consultancy Group, runs through the various factors to consider before converting to sand:
1. Think about slurry handling
Slurry handling is the number one consideration when thinking about moving to sand. On systems with underground channels or slats, sand can cause issues with slurry flow.
It’s worthwhile installing a slurry separator with a sand lane. This will ensure only the liquid enters the slurry store and will remove the need to dig the store out. A slurry separator will cost about £50,000-£60,000.
When putting up a new shed, consider using V channels rather than the standard U-shaped channels where sand can settle.
2. Consider equipment wear and tear
Sand will increase wear and tear on equipment, so be aware that chains and bearings will wear quicker. It could also halve the lifetime of any chain systems in underground channels.
Any automatic scrapers will also have to work harder to scrape slurry with sand. Consider scraping more frequently to reduce pressure or moving to tractor scraping.
3. Consider heel stone height and bed depth
The height of the existing heel stone will dictate how you convert existing cubicles to sand.
Mr Dodd believes 30cm (12”) is the maximum height for a heel stone, with no detrimental effect on foot health seen up to this level.
If the existing heel stone is 23cm (9in) for example, there is room to increase its height. As a result, it may be more cost effective to bolt a 5x10cm (2x4in) plank or angle iron on the back of the bed and fill in the bed with sand.
If the existing heel stone is already at 30cm (12”), the bed will need to be dug down. For example, 20-25cm (8-10in) of concrete could be removed from the bed and then built up with 5-10cm (2-4in) of chalk before 13-15cm (5-6in) of sand is added on top. The chalk provides a free-draining layer and reduces sand requirements.
Mr Dodd views 10-15cm (4-6in) of sand as the optimum sand depth – any more increases the likelihood of sand wastage off the back of the beds.
4. Get cubicle dimensions right
Sand can raise the height of the bed.Â
If the bed is raised 10-15cm (4-6in) for example, the whole cubicle will need to be moved 10-15cm (4-6in) higher.
If cows were lying well on the mats before making changes, make a note of the measurements and replicate them with the sand, but lift the cubicle higher. If you don’t, cows may not lie correctly.
Be sure to use the right measurements for your herd, rather than generic numbers.
5. What’s the pH of your land?
Know the pH of your soils. Sand is alkaline so if you apply alkaline slurry to soils that already have a high pH, you could compromise crop performance.
Target slurry towards more acidic ground or think about how you might export slurry and FYM.
6. Choose the right sand
Be aware of where sand is being sourced. Dredged sand in-particular may be cheaper, but can have a higher bacterial load, which could compromise udder health.
When in doubt, get sand analysed for bacterial load.
Generally, farmers opt for quarry or beach sand. The source chosen will largely depend on geography. Be aware that haulage will add to overall costs.
7. Ensure you manage cubicles well
Cubicle management is just as important on sand as it is with any other bedding material.
Any wet material needs to be forked out daily – if not twice daily – and beds should be topped up two to three times a week.
Level out any dips in the bed, otherwise milk can pool, causing bacteria risk.
Case study: Green Farm
Converting existing cubicles to sand and building a new, deep-bed sand cubicle shed has been one of several factors which have helped improve udder health at Green Farm, Shrewsbury.
Last year, dairy farmer Matthew Thomas decided to convert some of the cubicles in “the worst sheds” to help tackle challenges with somatic cell counts and mastitis.
Farm facts
- 480 cows yielding 12,000 litres a cow a year.
- £13/t – cost of sand, versus about £130/t for sawdust.
- ÂŁ15,000/ year – cost of sand used in the modified cubicle buildings, versus ÂŁ16,800 with sawdust.
- 170,000 cells/ml – winter somatic cell counts after moving to sand.
- 22 mastitis cases/100 cows – seen in January-February after moving to sand, scraping more and milking three times a day, versus 67 cases in May-July on sawdust.
The farm also moved to three times a day milking and increased scraper frequency.
Since then, yields have increased from 35 litres a cow a day to 41 litres, and mastitis cases have almost halved.
In the existing shed, Mr Thomas opted for the simplest and cheapest option, removing the mats and attaching a 10cm (4in) angle iron to the top of the 20cm (8in) curb, creating a 10cm (4in) sand bed. It took two people one day to convert 100 cubicles.
See also: 7 considerations before converting to sand on your dairy
“It was very simple. You can do it with unskilled labour between milkings. It was really profitable as it didn’t cost me in [additional] labour, just in steel,” he says.
In the new shed, he opted for 20cm sand beds with a crushed stone base. He views 10cm as the minimum for cow comfort and believes the new shed is the gold standard.
“In the old shed, I’ve made a two-star shed into a four-star shed and the new shed is five-star,” he says.
Sand has proved cheaper than the sawdust used previously. However, there have been added handling costs. The old shed has tunnels and a slurry tower, which means sand can block up the system.
“It does get blocked, but I’ve found a solution,” he explains. “I’ve put a piece of pipe inside the tunnel and I flush it through with an umbilical pipe every day. That keeps the slurry circulating around and then it’s pumped to the tower.”
A digger is now hired every six months to dig out the tower. Two tractors and spreaders are also hired to spread the solid material. This equates to additional costs of ÂŁ5,000/year.
To justify this, Mr Thomas calculates that cows need to produce 0.25 litres more a cow a day, which they are.
With the combined benefits of udder health and cow comfort, he believes the pros outweigh the cons of sand. “I don’t think it’s going to be an easy product long-term, but it’s great for the cows,” he says.