WIYLS goes inside Duchy College’s £3.6m dairy unit
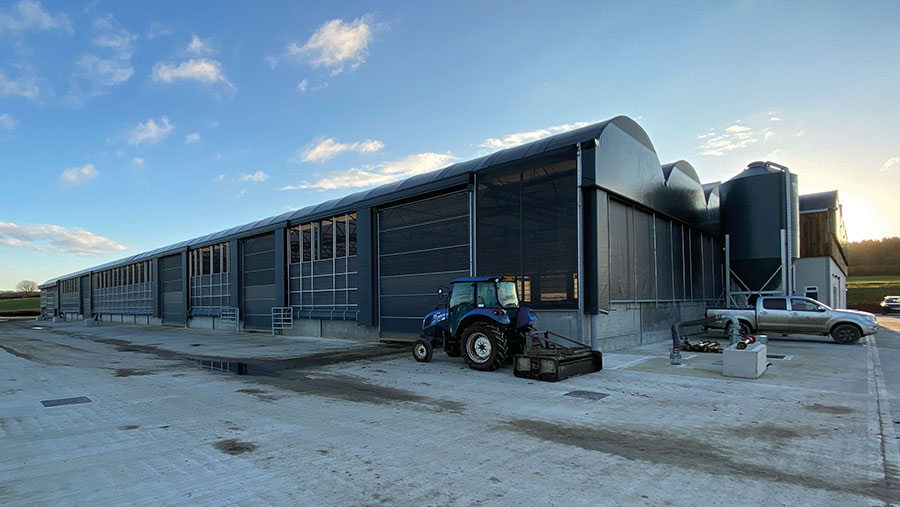
Improved cow comfort and a better feeding regime have boosted milk yields by 2 litres a cow a day at Duchy College, Cornwall.
The “Future Farm” research facility, which houses the farm’s herd of 225 Holstein cows, was finished last autumn and cost £3.6m.
The building contains a 20/40 Boumatic swing-over parlour, cubicles and feed kitchen under one roof. It allows the cattle to be managed as three mini herds to facilitate research into the effect of different diets on criteria including emissions and slurry consistency.
Farm facts
- Boumatic 20/40 swing-over parlour
- Autumn calving herd
- Milking 225 Holstein cows
- Milk sold to Saputo
- Grazed from March to September
- 267ha (659acres)
- Farm rented from the Duchy of Cornwall
See also: WIYLS visits a £300,000 self-build cubicle shed
The state-of-the-art facility will provide a resource for students to undertake practical instruction.
James Coumbe, farms director at Duchy College, gave us a tour of the new set-up.
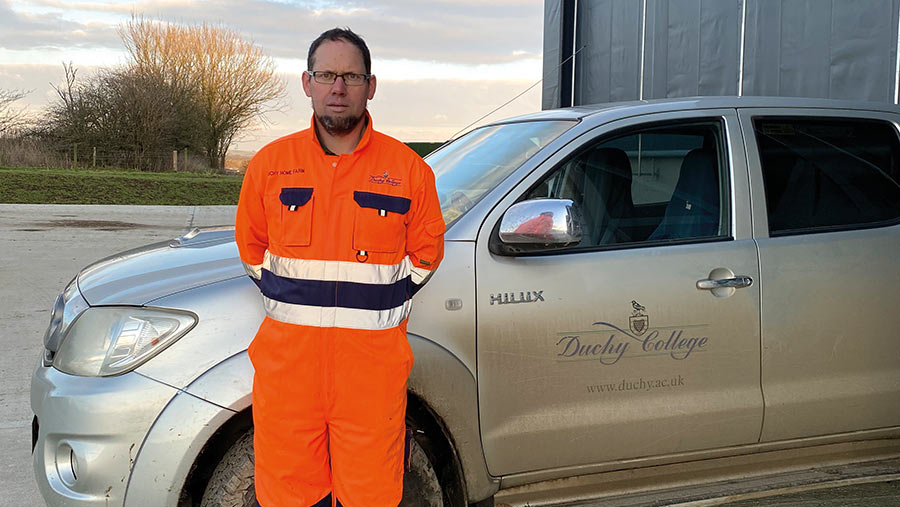
James Coumbe © Ruth Wills
Why did you build the unit?
We wanted to set up a facility where we could research topics which would be important to the industry, such as waste management, diet composition, environmental impacts and welfare.
We hope the build, which has been years in the planning, will benefit the students and the wider dairy industry through knowledge transfer. Although it is a research facility, it is also an operational farm on which students can learn practical skills in livestock management.
The new unit is just a few yards up the road from the old one, so the herd transition was pretty smooth.
What was the initial budget for the project?
The £3.6m construction was part-funded by the European Regional Development Fund, Cornwall Council, the Council for the Isles of Scilly, Cornwall College, the Centre for Innovation Excellence in Livestock (Ciel) and the Department for Education through the Agri-tech Cornwall Project (ACP).
This was a little over budget, but this build was a challenge, not least because it took place over a severely wet winter. There was also the delay and supply chain complexity of working during Covid-19.
This is not a conventional agricultural facility – incorporating equipment and infrastructure to enable cutting-edge research, teaching and knowledge transfer costs more than a normal dairy unit would.
Who designed and built it?
The light, airy nature of the building and the integrated technology were inspired partly by the South West Dairy Development Centre.
The design was put together in collaboration with Michael Goff, a dairy design specialist, and the overall build and construction was managed by Brady Construction Services.
Tell us about the specifications
The building is 84m long, 55m wide, and 6m to the eaves. The feed kitchen with the Trioliet automatic feeder is 20x20m and 6m to the eaves.

© Ruth Wills
The five silage pits comprise two at 14.3m, two at 9.5m and one at 11m, and they are all 11m long.
What is your favourite feature?
I like that everything is under one roof; in our previous system I was going in and out, getting drenched in the rain. It can also be staffed with minimum labour.
The ID Agro building allows a lot of natural light in through the synthetic sheeting on the side and roof. The ventilation system links to humidity, rainfall and temperature sensors which monitor the weather.
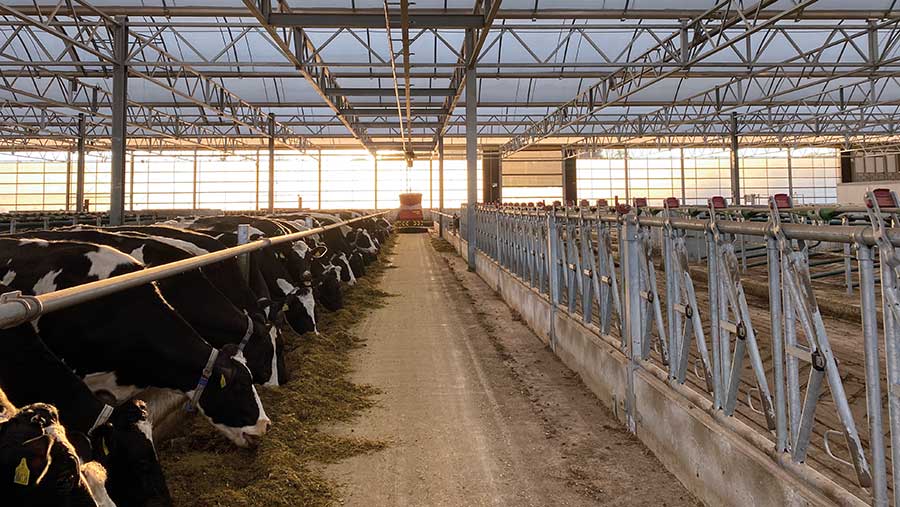
© Ruth Wills
Automatic Cowcare scrapers clean the passageways and a Storth slurry handling system deals with the slurry.
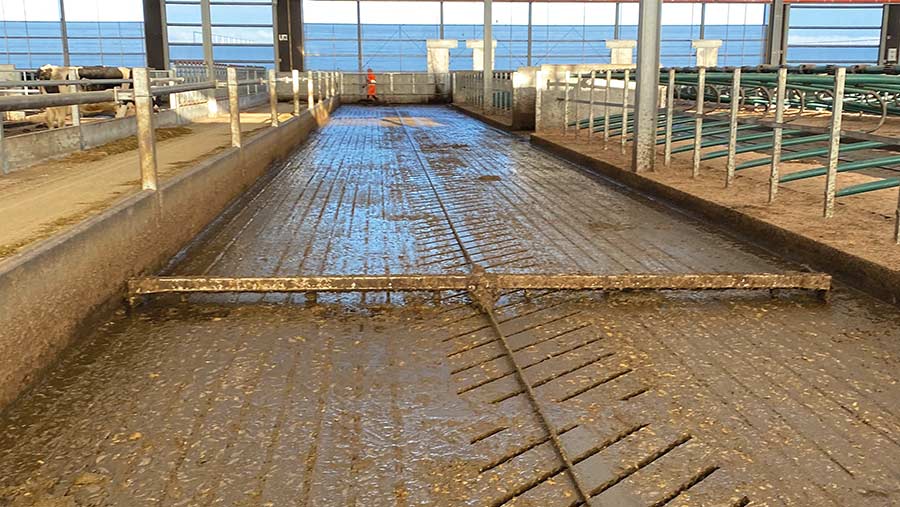
© Ruth Wills
The cows have Easyfix cubicles and mattresses and the Trioliet T40 automatic feeding system feeds them five times a day at present.
All of the automatic systems are great, but it has taken time to get them synchronised so that, for example, the automatic scrapers are not running while the cows are being fed.
Best buy and why?
The silage clamps are a massive step forward and they make management of our forage stocks much easier and more efficient.
We have individual silage clamps for each product, whereas previously we just had one, which was a bit of a jigsaw puzzle of different forages. When we came to filling the clamps in 2020, we realised what a pleasure it was to have them.
What couldn’t you live without?
The milk meters and feed-to-yield system in the parlour are great, as well as the automatic cluster removers which prevent overmilking. The automatic plant washing saves time and brings consistency to the parlour routine.
How has it helped ease management or improve cow performance?
The Trioliet automatic feeding system allows us to feed the cows a total mixed ration five times a day, little and often. The cows constantly have access to fresh food and they are in a light and airy environment.
Although we haven’t been in very long we did see an increase in milk production of 2 litres a cow a day in the first six weeks, to 34 litres a cow a day..
The new facilities are also much more user-friendly for staff, creating a more enjoyable working environment.
In addition, it has improved slurry storage and the ability to manage dirty water.
Slurry for each cow group is kept separate to be spread on individual fields – allowing us to record the impact of different management regimes on greenhouse gas emissions, water quality, impacts on flora and fauna and soil quality.
What future changes would you make?
One future plan is to roof over our silage clamps and slurry stores, to ensure clean water isn’t adding to our waste. We are also looking at potentially collecting gas from the slurry store, for use as on-farm power or heat, or to sell as fuel.