Don’t bale out on good returns
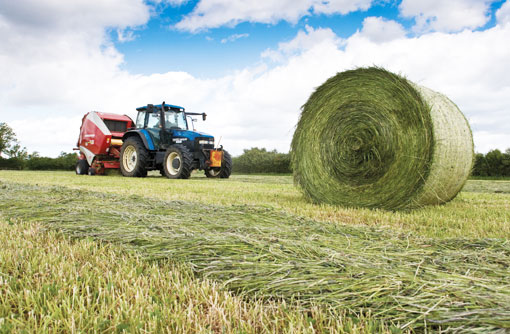
Livestock farmers could see significant returns from improved big bale silage quality by looking more closely at cutting times and wrap management, Aly Balsom reports.
Big bale silage producers could be losing £3.50 a bale by failing to meet best practice requirements in the field and at the bale stack.
According to silage expert and director of Silage Solutions, Dave Davies, with a cost of production of 12p/kg of dry matter (DM) for every big bale produced, this equates to a cost of £3.50 when 15% losses in DM are seen.
Rhun Fychan from Aberystwyth University says although there will always be losses in any system there is scope to reduce them substantially by following best practice.
“By reducing losses from 15% down to 10% farmers could see a minimum saving of £1.17 a bale without taking into account the quality of the feed or the implications of feeding mouldy silage to stock and the health issues involved.”
With this in mind Dr Davies runs through six key steps to producing top-quality big bales:
1) When to cut
• Whether you’re cutting silage for clamping on baling, cutting date is crucial to produce quality silage.
• For most livestock, grass should be cut before the stem starts to thicken and the seed head starts to emerge.
• Monitor yields on different fields to assess which may benefit from a late summer/early autumn re-seed.
• For sheep, finishers, growers and milking cows, farmers should be aiming to produce a silage of more than 70D.
• For a 72D silage, grass will need to be cut at 4,500kg DM/ha.
• A high-quality silage will reduce the need for concentrate feeding.
2) Cutting height
• In ideal conditions with good cover in the bottom of the sward, silage should be cut down to 5cm.
• When the sward is open, consider cutting to 7.5-10cm.
• Producers experiencing drought may be tempted to cut silage as close to the ground as possible to maximise yields, however doing so will have the opposite effect.
Cutting too low will:
• Reduce yields across the season as recovery time will be slower.
• Increase the risk of soil contamination and result in poorer fermentation which will actually lower the quality of silage to feed.
3) Additives
• An additive will be beneficial when aiming to produce high-quality silage.
• There are two types of additive, one that improves fermentation or an additive to improve fermentation and aerobic stability. In big bales you should only need one to improve fermentation.
• Aerobic stability should be controlled through bale and wrap management.
4) Wilt times
• Grass should be spread as wide and quickly as possible after cutting to increase the rate of drying.
• Raking will speed up wilt.
• Using a conditioner mower and spreading the crop out the back will increase water evaporation rates and reduce the need to rake as much.
• Wilt times should be targeted for the dry matter you are trying to achieve.
• A wilt time of one day to 36 hours is needed for a 30% DM silage.
• For 50% DM, grass should be wilted for two to two and a half days.
5) Baling
• Grass should be rowed up in even box shape rows so grass enters the bale more evenly, creating square corners.
• It’s important to get a good solid bale with as much in it as possible.
• The net on the bales should come right to the edges, if not over the sides – this is important to prevent pockets of air from forming when the bale is wrapped.
• A bale of chopped silage will be 20% heavier than one that is not chopped, producing less bales with the same silage but less wrap.
• Producers could see a £80 saving/100 bales in wrapping, stacking and carting costs alone by chopping silage – actual savings from additional improvements in quality are likely to be higher.
• When moles are a problem, consider baling these areas separately to prevent a larger number of bales from becoming contaminated.
6) Wrapping
• Four layers of wrap is a minimum.
• Six layers will significantly improve silage quality.
• Wrap away from the field at the storage site where possible to reduce the chance of the film being punctured.
• Where wrapping in the field is unavoidable, do all you can to prevent damage to the wrapper – six layers will help protect bales.
Case study: Stephen Jukes, Gables Farm, Barnby-in-the-Willows, Newark
Careful handling and attention to small details – that’s the key to ensuring the production of top quality big baled silage, according to Nottinghamshire dairy producer, Stephen Jukes.
“There’s no point putting the effort into making bales if you’re just producing waste,” he says.
S W and P E Jukes have been producing big bales since the process was first introduced and now make about 600-800 grass and grass/red clover mix silage bales for the 100 cow British Friesian herd every year.
Years of experience have highlighted the wrapping and carting process as crucial to making the best silage possible.
“We cart the bales green from the field and wrap on a concrete base. After wrapping they’re then tipped off onto a roll of carpet to prevent the wrap from being punctured,” says Mr Jukes.
“Wrapping away from the field is also important as wrapping in the field can cause punctures – particularly from hard red clover stalks.”
Wrapped bales are also moved using a homemade squeeze grab, rather than forks to prevent damage. “When we used a spike we used to spend a lot of time patching bales – cradling the bales prevents this,” he says.
Grass is also chopped as it is baled, with six layers of wrap applied. “We’ve experimented with and without chopping and chopping is definitely better – silage is better quality when the bales are opened up and cows don’t sort the ration as much.”
Mr Jukes also believes the extra costs of applying six layers of wrap are outweighed by the improved quality.
Are we really getting the most from our big bale silage?
Results from the National Baled Silage Farm Survey conducted by the Silage Advisory Centre across 80 farms and 55,000 bales in England and Wales found many producers could be failing to meet minimum standards needed to get the most from baled silage.
Rhun Fychan, researcher at Aberystwyth University, talks us through the results.
SURVEY FACTS: Nearly 20% of farmers that said they were aiming to apply four layers of bale wrap failed to do so. 50% of farmers who thought they were applying six layers of wrap were applying less
EXPERT OPINION: Four layers of film is the minimum requirement for bales. Follow guidelines attached to the film wrap reel and count the number of revolutions of the wrapper to ensure you are meeting your minimum standards. Generally 16 revolutions are needed to apply four layers and 24 revolutions for six layers- but don’t take this for granted and check with the manufacturer. Also, when using a contractor discuss requirements before they arrive on farm. Applying six layers of wrap rather than four will bring considerable quality benefits in terms of improved ME and sugars.
SURVEY FACT: 60% of bales with just four layers of wrap had mould present compared to 34% of bales with six layers (see graph).
EXPERT OPINION: The cost of applying additional layers is fully justified by the improvements seen. Applying six layers can give a five to six fold reduction in mould versus four. Although applying less than four layers may save 10-20p a bale the cost implications in terms of compromised silage quality and animal health are considerably more.
SURVEY FACT: 50% of farms had never had baled silage analysed
EXPERT OPINION: Sampling is a cost saving exercise considering the savings in concentrate and winter ration costs that could be made from understanding silage quality. Samples should be taken from 3-5 bales from each cut to get a sufficient representation of quality.
SURVEY FACT: More than half of producers wrapped bales in the field
EXPERT OPINION: It is advised bales are wrapped away from the field at the storage site to minimise damage. When wrapped bales are tipped on to grass stubble or transported on rough trailer beds there is a higher risk of film being punctured. This will increase chances of oxygen penetration, promote mould growth and reduce quality. In worse case scenario, mould could even cause livestock deaths. When wrapping bales in the field is the only option, apply more layers, and do not risk bird damage by leaving bales in the field – move on the day of wrapping. And at the storage site, ensure bales are covered with a net to protect from bird damage and ensure any hardcore base does not contain sharp objects.