Cell grazing improves liveweight production from grass
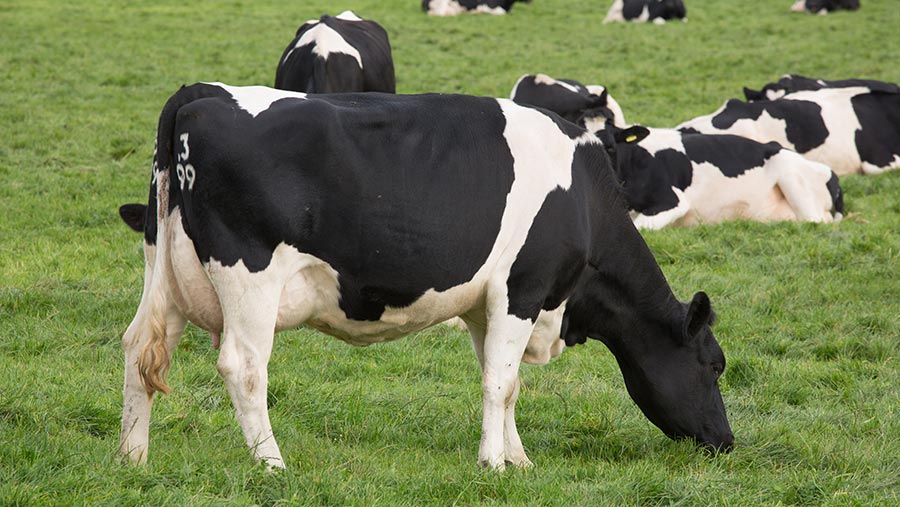
Cornish young farmer and engineer James Daniel believes UK farmers can grow more grass than their New Zealand counterparts by harnessing rotational grazing strategies.
Following a six-month stint working in Rangitikei, New Zealand, two years ago, where he ran the farm of technograzing founder Harry Wier, Mr Daniel brought the philosophy back to the UK and set up Precision Grazing.
He believes technograzing – an intensive form of rotational grazing using defined cells – is the answer for farmers looking to sustainably increase production while lowering costs.
James Daniel’s role
- Surveys, designs and installs the systems on farm
- Farm data is entered into a pasture-based modelling program called Farmax, which calculates the energy requirement of the animals and models it against predicted available energy (grass DM/ha x grass ME)
- This helps determine the stocking rate, rotation length and target kg LW production for each system
- Weekly plate meter measurements and monthly pasture quality samples are taken, normally by the client, with stock generally weighed at eight-week intervals
- Measurement data is interpreted by Mr Daniel, who, for a monthly fee, provides a weekly grazing management plan.
“We don’t know grass like the Kiwis. We grow more of it. The grass-growing potential in the UK, particularly in Wales and the South West, is brilliant,” explains Mr Daniel.
See also: Grassland management revival boosts sheep output
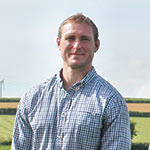
James Daniel
“New Zealand has higher average temperatures, but this means they run out of moisture in the summer and that really limits their annual pasture production.
“Here in the UK we are generally summer safe. In general, our production is limited by a lack of grazing management.”
Mr Daniel designs and installs grazing systems to suit clients’ requirements and provides training and specific management options to ensure performance targets are achieved.
How the fields are set up
- Semi-permanent electric fences are used to construct lanes that are then sub-divided into cells as required using temporary, electric fencing
- Lane fences consist of fibreglass posts and high-tensile wire that incorporates a special spring arrangement, allowing it to be pegged down for stock or machinery to pass over the top. It also means if stock comes into contact with the fence it absorbs the impact rather than breaking
- Portable water troughs are moved easily by hand between cells. These are connected via hydrants to the water through 25mm MDPE pipes that run above the ground next to every second lane.
The potential of the technograzing model for the UK is currently being investigated through trial work supported by the AHDB Farm Innovation Grant Scheme 2016.
Mr Daniel is managing the trial, which started in March 2016 on three farms in the South West and will conclude in November. A report on the trial will be made available through AHDB’s Better Returns programme.
We spoke to three farmers who are practising technograzing to find out what benefits it has brought them.
Q&A on technograzing
What is technograzing?
Technograzing is a cell-based, rotational grazing system. The infrastructure allows the accurate allocation of feed and large numbers of animals to be regularly moved with minimal labour.
Who invented it?
It was developed in New Zealand by farmer Harry Wier. In 1969, while at Massey University, Mr Weir was inspired by a grazing experiment run by Ray Brougham using Friesian bulls that consistently produced 1,000kg DW/ha/year .
Mr Wier set about replicating this experiment on a commercial scale at the family farm. He struggled to create his vision using conventional fencing materials, so began manufacturing his own.
In 1987 he and his wife Chloe formed Kiwitech International and they gave their first technograzing training course in 1993.
Is it suitable for me?
If you want to increase production a hectare by growing and using more pasture, then yes.
Increasing stocking rates allows more animals to be kept on surplus land that can then be released for other enterprises. But it is important the increase in production is planned for, as simply growing more pasture is not profitable unless it is used.
What are the benefits?
Improved soil organic matter, better pasture composition/sward longevity, even manure distribution, extended grazing season and increased farm output (kg liveweight/ha).
It also provides infrastructure to enable cultural control methods to be used to reduce worm burden – for example, longer rotation lengths (>60 days) and mixed-species grazing (sheep and cattle).
How much does it cost?
Cost/hectare depends on the type of stock (sheep, cattle or both), the amount of sub-division, topography and access to water (suitable pressure).
As an example, to design and install a 8ha single-wire cattle system consisting of four lanes on gentle contour, providing the infrastructure to divide land into 100 0.08ha cells (with water) would cost about £470/ha (excluding water supply connection and electric fence energiser).
What fields does it suit?
Generally, the quickest return on investment is seen when installed in south-facing fields with productive swards.
However, the system can also help improve the quality of less-productive ground. Larger, rectangular fields have the lowest cost/hectare, but the model can be adapted to fit multiple small fields.
Case study 1
Andrew Jones, Higher Trevallett Farm, Launceston, Cornwall
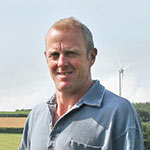
Andrew Jones © Rhian Price/RBI
Increased competition in sourcing store animals to supply his approved finishing unit (AFU) led mixed farmer Andrew Jones to review his practices.
Currently he sources TB-restricted heifers and steers from market aged 18-24 months and finishes them in an intensive system using grass silage and home-mix concentrate for a quick, five-month turnaround.
However, as margins get ever tighter, Mr Jones has been looking for ways in which he can source and grow younger cattle to supply his unit without incurring high feed costs.
Farm facts
- Finishes 500+ cattle a year
- Farms 223ha
- Contract-rears 370 dairy heifers
- Grows 53ha spring barley and 40ha of fodder beet
“We needed a system that gives us an option to buy lighter animals that are less in demand and rear them in a productive, low-cost system ready for the shed,” he explains.
As part of the AHDB trial he began grazing 42 400kg Continental- and native-cross heifers and steers aged between 16-22 months on a 4.77ha technograzing system in March, with animals stocked at 6LU/ha on permanent pasture.
The area is sub-divided into four lanes and is designed to allow a maximum of 64 cells to be created. On average the cattle have been following a 32-day rotation by providing four cells (0.3ha) every two days.
Technograzing system
- Grass quality: 11.6ME and 21% crude protein (average)
- Soil type: Clay loam
- Average stocking rate 6LU/ha
- Average daily liveweight gain: 0.83kg/day
- Total production/hectare (1 March to 31 August): 826kg LW
Cattle were trained for three to four days to use the electric fence in a dedicated field that had a single wire electric perimeter fence erected inside a secure boundary fence.
The aim is for cattle to move to a new cell every two days in summer, entering at pre-grazing covers of 3,600kg DM/ha and leaving residuals of 1,400-1,500kg DM/ha.
The set-up cost £461/ha (including design, installation and capital equipment), but he estimates the system will provide nearly 100% return on investment within the first year as a result of increased liveweight (LW)/ha production.
From March to end August, on average, cattle grew at 0.83kg LW/day, with production reaching 826kg LW/ha. The target for 2016 is 1,200kg LW/ha.
Mr Jones says his greatest concerns when he began cell grazing were how the cattle would adapt to the system and the potential extra labour involved.
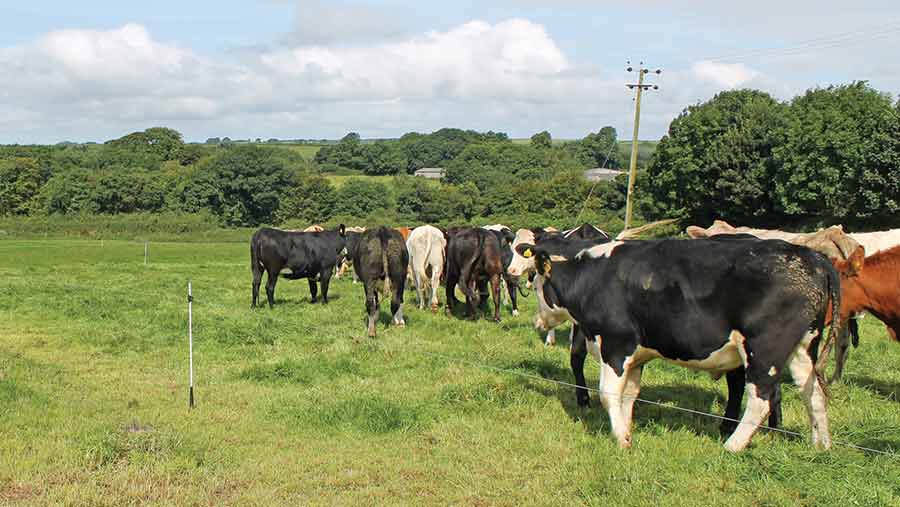
© Rhian-Price/RBI
However, five months in and he has been very pleased with the results.
“It is amazing how content the cattle are. It took about three movements to get them used to crossing over the fences and now shifting only takes 10 seconds. You can literally see the grass growing behind them.”
Case study 2
Nick Jasper, Bradstone Manor Farm, Tavistock
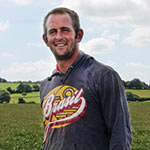
Nick Jasper ©Rhian Price
Technograzing is allowing sheep farmer Nick Jasper to lift production from forage by maximising the production potential of his grassland.
Mr Jasper first saw the system being used in New Zealand and thought it would be a good fit to help him use his largest fields more effectively.
He has been involved in the trial since May.A system was installed in one 12ha field that was sown in autumn 2015 with a mix containing Aber diploid grasses, white clover and tonic plantain.
The area is divided into four 2.5ha lanes and one 2ha holding paddock, providing a possible 120 cells.
Farm facts
- 677 Romney ewes and 200 ewe lambs
- Farms 202ha
- Grows 40ha spring barley, 6ha of fodder beet, 6ha maize
Flocks are contained using three fences – a back fence, front fence and safety break. When it is time to move cells (generally every two days) the front fence is pinned down and animals cross over, grazing up to the safety break, which then becomes the front fence.
The back fence is then collected and placed as the safety break, ready for the next shift.
Mr Daniel says this method is much more productive and adaptable than operating a fixed number of cells and allows grazing area to be changed to suit demand.
It also requires less capital equipment, reducing costs.
A single flock of 240 ewes and lambs were introduced to the system six weeks after lambing.
Stocking rates were initially 20 ewes/ha (2.2LU/ha) rising to 36 ewes/ha as the lambs consumed more grass.
Ewes and lambs grazed 0.85ha every two days, which enabled a 26-day rotation. Entry target covers were 2,700kg DM/ha, with sheep exiting at 1,400kg DM/ha.
The grass growth has been “unreal”, says Mr Jasper, who adds that grass grew 80kg DM/ha/day on average from May until August.
In 2016, the field has so far only received one application of a slow-release nitrogen fertiliser in March. Successive grazing rotations have seen dramatic increases in grass plant tillering, increasing ground cover by 30%.
After weaning, the heaviest 220 male Romney lambs were grazed ahead of 150 dry hoggets for one rotation.
Technograzing system
- Grass quality: 12.3ME and 24% crude protein (average)
- Soil type: sandy loam
- Average stocking rate: 2.78LU/ha
- Average DLWG: 0.21kg/day
- Total production/hectare (20 May to 31 August): 600kg LW
“By adopting the leader-follower system we were achieving great grass use without compromising our lamb growth rates. If we held the lambs in one place for longer they wouldn’t be eating as good a quality grass. The ewes cleaned up and left a perfect residual,” says Mr Jasper.
240 store lambs with average weight of 35kg were then brought into the system. Mr Daniel used Farmax to help model the number of lambs the system could support based on forecasted grass growth.
He believes one key benefit of the technograzing system is the reduction in labour associated with checking stock.
“I can pull in the field and travel directly to the animals rather than having to cover the whole area. Also, every two days I watch every single animal walk past me as they cross the fence. This makes it easier to detect early signs of lameness or mastitis. This time saving by far outweighs erecting break fences.”
Case study 3
Alwyn Hughes, Pengelli Farm, near Caernarfon
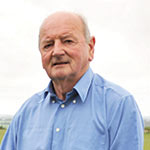
Alwyn Phillips © Olivia Cooper
Switching to rotational grazing from a set-stocking system has allowed Alwyn Phillips to increase his stocking rate by 25%.
Mr Phillips, who runs two performance-recorded pedigree flocks of Texels and Poll Dorsets near Caernarfon, has increased ewe numbers from 400 to 500 since adopting cell grazing.
Farming Connect Focus Farmer Mr Phillips has been recording his flock on grass since 1980 and turned to cell grazing in a bid to improve his growth rates from grass.
“My Texels have one of the highest muscle EBV in the breed – the top 1% for muscle is 3.49mm and my best rams are 7.15mm – but I cannot compete with the 20-week weight EBV for growth against lambs on continuous creep feed. To improve my lamb growth, I knew I had to improve my grassland management.”
“My ram customers value this grass-based approach, because they are producing prime lambs off grass as well. There is a perception that it is a lot of extra work, but once the sheep are trained it is really very simple, provided you have a well-designed system.’’
Rotational grazing has been installed on four fields covering 24ha at Pengelli Farm. The area was divided into 24 1ha cells.
The aim is to turn ewes into grazing covers of 2,000kg DM/ha and exit at 1,400-1,500kg DM/ha, but because it has been such an exceptional growing season, Mr Phillips has been turning sheep in at 2,500kg DM/ha.
Set-up costs
- £341.79/ha and included 2,500m of Kiwitech semi-permanent electric fencing and 1,200m of water pipe
- Increased number of ewes will return an additional gross margin of £8,700, not taking into account additional benefits such as increased lamb growth rates and improved pasture composition, so the system will pay for itself in under two years
The rotational grazing system at Pengelli is stocked at 4lu/ha (eight ewes/acre), with the peak stocking rate exceeding 6lu/ha (12 ewes/acre) in July, when 8ha was taken out of the rotation for silage.
The sale of finished lambs will reduce the stocking rate to 2.5lu/ha (five ewes/acre) by November in preparation for the winter rotation of deferred grazing and silage.
“Expanding the flock by 100 ewes would have required an extra 8ha of land under Mr Phillips’ traditional grazing system.
“Assuming an area of this size was available locally to rent, this would substantially increase his costs. Instead, he has made a capital investment in infrastructure that will add value to his land,’’ says Mr Daniel.
Grass is measured weekly by Mr Phillips and Farming Connect’s Gethin Davies. Results are sent to Mr Daniel, who analyses the figures and respond within 24 hours with a management plan.
Not only does the system allow Mr Phillips to grow more grass with a high concentration of clover, but it also reduces fertiliser inputs.
He applied 50kg/acre on all paddocks in May and a further 75kg to the 8ha of silage ground in June.
Mr Phillips runs up to five different groups of sheep at any one time, which he says demonstrates that rotational grazing is as suitable for complicated systems as simple ones.
“We manage it so that the priority groups get the best grazing – for example, the weaned lambs will graze ahead of the dry ewes.”
Mr Phillips now aims to establish a rotational grazing system for his herd of 40 mostly pedigree Limousin beef cattle.
Drone video
Watch the drone video of cattle and sheep precision grazing.