Advice on converting farm buildings for pig B&B
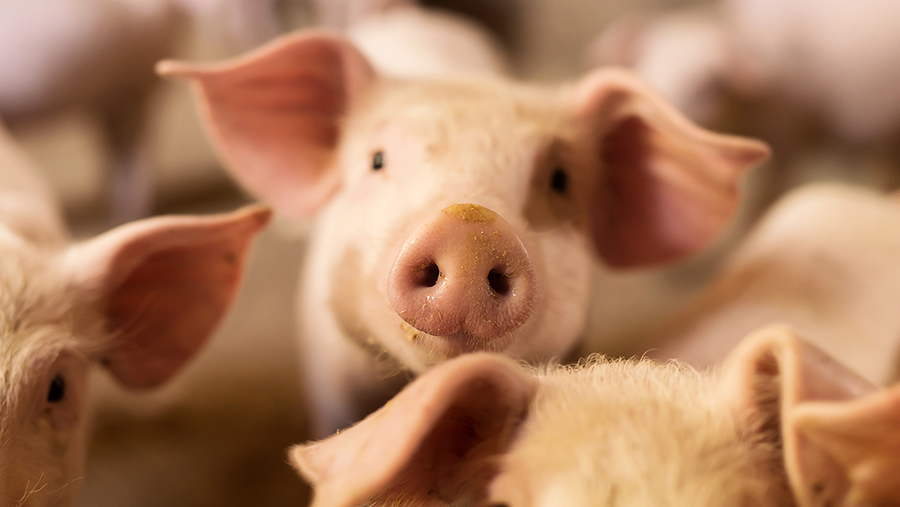
New-build sheds on greenfield sites have been a popular choice for farmers setting up a bed and breakfast pig enterprise, with short payback periods, new-build bonuses, and a good return on investment.
However, with the price of steel, wood, and concrete escalating over the past 18 months since the start of the Covid pandemic, conversion options are proving more cost-effective.
“Before Covid, you would be looking at a payback of four to five years on a new build, but with current prices for materials that would be 10-15 years,” says Mark Jagger of BQP.
See also:Â Advice on setting up a b&b agreement
He says the cost a pig place on a new-build greenfield site has risen from ÂŁ265 a pig to ÂŁ320 due to the rise in material costs.
“New builds are likely going to slow until the price of materials come down. Conversions of farm buildings are what farmers are going to be looking at,” he predicts.
What to do if you think you have a building that could be used for contract rearing pigs
- Speak to a contract pig-rearing company such as BQP
- Arrange an initial site visit
- Visit existing B&B pigs farms to look at their setups
- Arrange a detailed site visit with the pig company and discuss the best options for the building
- Get the plans drawn up and get quotes for the cost of the project
- Put together a business plan
- Arrange finance
- Organise straw supply and muck removal
Mr Jagger says he has seen many existing buildings successfully converted for growing pigs. Examples include poultry houses, cattle sheds, dairy collection yards, potato stores, and sheep sheds.
“If you have clear-span buildings or old buildings, do not assume they can’t take pigs. Don’t discard anything. It is rare we come across a building we cannot adjust.”
He says the biggest thing that will limit a conversion is the size of a building, with buildings required to hold a minimum of 500 pigs.Â
Conversion costsÂ
Typical costs for a shed conversion are about ÂŁ200 a pig place. This covers:Â
- New concrete floor
- Internal pens
- Feeders and drinkers
- Waterline and system.
Although there is still a significant outlay for producers when converting an existing building, the good news is these conversions can be eligible for a build bonus payment with BQP, providing the building is converted in line with its requirements.
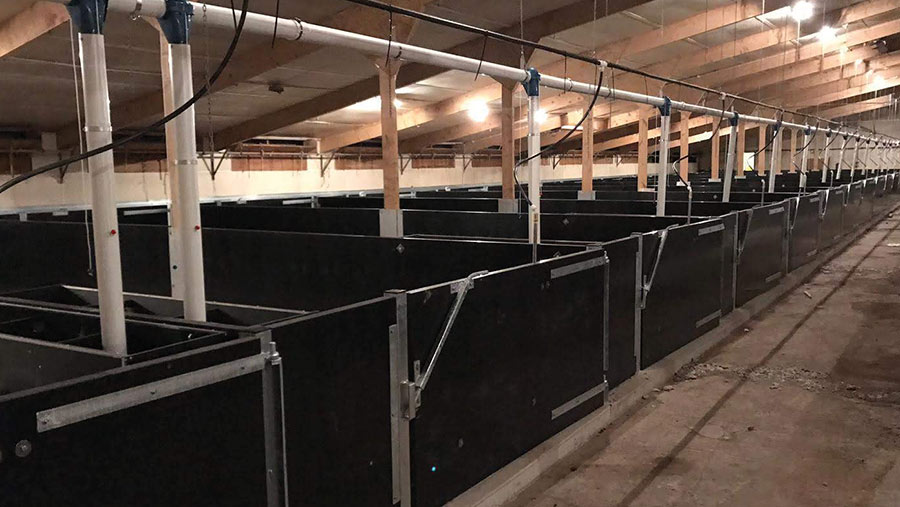
© BQP
“If a farmer converts a building and invests in a bespoke layout for the pigs to suit that building, then BQP will support the project with a similar enhanced payment structure to the new-build offer and, in many cases, the full new-build support offer can be achieved,” adds Mr Jagger.
This bonus equates to ÂŁ4.50 a pig on top of the standard payment for the first 13 batches.
The process of conversion
Once a farmer has decided to convert a building, a farm visit is required to come up with an agreed plan for conversion.
BQP works with the farm to draw up the plans. It will even help get quotes for the project through pig construction specialists Quality Equipment or the farmer can cost up using local suppliers themselves.
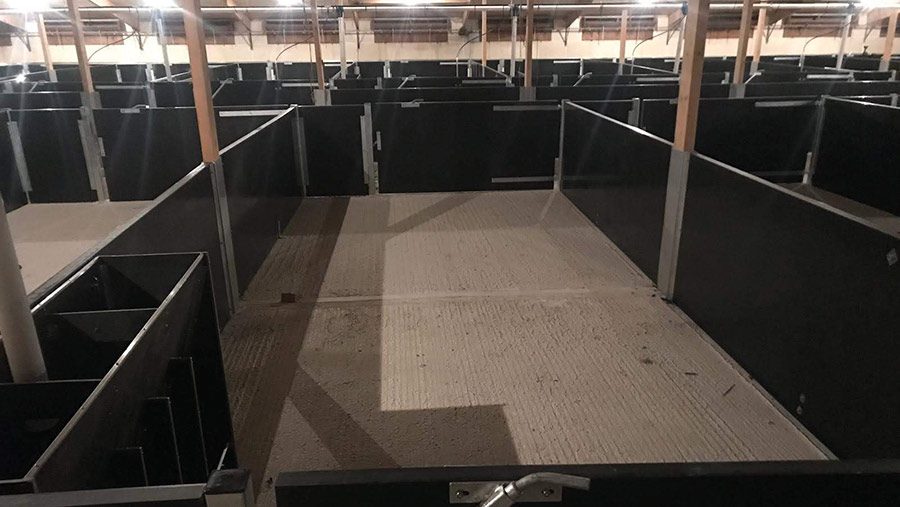
© BQP
If it is a new build, then planning permission will be required. Mr Jagger has helped many farmers through the planning approval process.
BQP will also work with the farmer to draw up a business plan. This details the farmer’s financial outlay and projected earnings. This can then be presented to the bank or lender to help secure finances.Â
Once the finance has been arranged, the only other things to consider are where the farm will source straw and dispose of pig muck.
Case study: Eric Davies, Stockport, Greater Manchester
Former poultry producer Eric Davies, from Millbrow near Stockport, decided to convert a 46x24m poultry shed to pig accommodation in September 2019 and has not looked back.
He was originally rearing day-old chicks before moving into broiler production.Â
“The company we were supplying our point-of-lay hens to reshuffled and weren’t collecting from our area anymore.
“We then switched to broilers, but the shed was only able to house 30,000 birds and we were unable to make it pay.
“The shed had laid empty for a couple of years, which was when I decided to contact BQP and enquire about rearing pigs,” says Mr Davies.
Mr Davies felt the timber-built shed wasn’t suitable for rearing cattle, which is why he opted for rearing pigs from weaning to finish.
He worked with BQP and Quality Equipment to design the layout of the building. It took Quality Equipment just three weeks to transform the shed into a 1,200-pig unit and cost ÂŁ92,000 plus VAT.
“We split the shed in two at the start, so we ended up with two 12m-wide sheds. This fits the pens better as we have 15 pens down each side.”
The pens are all made from plastic with a concrete laying area. Although the floor was concrete at the outset, Mr Davies invested in more concrete to create a 10cm raised area in each of the pens.
“The raised area is the bed and feeding area and the lower is the dunging area. It helps make it easier when bedding up and scraping out,” he says.
The building contains two passageways, which he can drive down with a quad bike and trailer to bed the pigs up. It also allows him to easily scrape out the dunging area each day.
Despite the significant upfront investment, he was rewarded with a new-build bonus on top of his baseline price.Â
He expects it will take him about 10 years to pay back the refit cost. “It could be paid off quicker, but the pigs are giving us a nice living,” says Mr Davies.
“Rearing pigs on contract is the way forward. Yes, there was the initial outlay, but we have had help every step of the way and BQP is on hand for advice whenever we need it,” he adds.