Beating bacteria in water systems
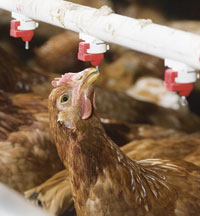
Effective cleaning of tanks, water pipes and drinking systems, to break down the biofilm of bacteria, mould and other substrates that exist, is essential to optimise bird performance in poultry houses.
Biofilms can often be seen on the inside of water pipes as a slime layer and can become a self-perpetuating source of pathogenic infection, says Murray Hyden of poultry supply company Kiotechagil.
They can also lead to leaky water nipples inside the house, which in turn causes wet litter and increased ammonia production, resulting in reduced performance and liveability.
“Water contaminated with microorganisms, algae, dust, and rust is all too common and has a direct impact on poultry performance” says Mr Hyden. “In serious cases, poor water quality can have a greater negative impact than poor feed quality.”
Despite the common perception that water quality in the UK is of a high standard, this is not always the case. For example, it is estimated that more than 40% of privately-owned supplies are contaminated with coliform bacteria, which can enter the water from a variety of sources, including sewerage, animal waste of dead animals.
Iron bacteria are also a major nuisance in many well-water supplies, forming a reddish-brown slime that coats the inside of pipes, fouls pumps and clogs drinkers.
And cyanobacteria, or blue green algae, can produce toxins in drinking water – though sometimes the treatment can have a worse effect than the toxins themselves.
Other algae can produce compounds which cause offensive flavours in poultrymeat and, of course, water contamination can taint water supplies, resulting in the birds refusing to drink.
Dissolved nutrients
Mr Hyden points out that an additional contributing factor to the presence of bacteria or algae is the amount of dissolved nutrients – specifically phosphorus and nitrogen, which promote growth through a biological process known as eutrophication.
In addition, nutrients leach into the water from rust and corrosion of tanks and pipes on older farms, some of which may not have been cleaned properly for years.
But the bacteria and algae that produce biofilms can be very difficult to kill. Common disinfectants and sanitisers cannot penetrate or degrade the cell wall, and the layers of slime provide additional protection from disinfection.
Mr Hyden therefore suggests that the only good way to get rid of these problems is to effectively “shock” water lines with a good sanitising agent between flocks.
Shocking the system
The aim of a water-system shock treatment is to expose all interior surfaces to a sanitising agent for a long enough time to reduce the surface tension of the biofilm, dissolve mineral deposits that have accumulated, and kill potential vegetative bacteria and algae.
“Basically, we need to destroy the biofilm, clean and disinfect the tanks, lines and drinkers and provide ongoing protection to ensure that a biofilm does not return,” Mr Hyden advises.
Simple flushing with water is not enough. It is necessary to add some form of organic acid to water lines prior to flushing.
Acid treatments are the best option to break the biofilm, while chlorine is best to prevent it from returning.
Mr Hyden points out that all acidifiers are not the same. For example, citric acid is an organic acid commonly used by poultry producers for acidifying their water. However, citric acid does not have good antimicrobial activity.
His advice is to use a buffered acid product, such as SALKIL Liquid, to clear biofilms in commercial poultry houses prior to disinfection with a chlorine-based disinfectant.
“Water maybe essential for life, but it is easily contaminated and provides an opportunity for all types of life forms,” says Mr Hyden.
An effective cleaning system:
1. Flush the drinking lines with water, using a high pressure flush to remove loose sediment.
2. Use a strong buffered acid product at maximum strength to achieve the necessary concentration. Wear necessary protective clothing.
3. Ensure that there is sufficient water volume to flush the lines completely.
4. Flush the water lines, dosing pumps, valves and tanks with the selected product and use a broom to sweep the nipple drinkers in order to get the cleaning product down into the drinkers.
5. Allow lines to soak for a minimum 60 minutes; overnight is better.
6. Flush with clean water to remove loosened biofilm, debris and remaining acids.
7. When all acid residues have gone – charge the drinking lines with fresh water. Then treat the water with a chlorine-based disinfectant either in the tanks directly or via a dosing line depending on the equipment available.
8. Check the last drinker in the line for the presence of chlorine using simple test strips. If no chlorine is found, increase the inclusion rate.