4 ways poultry technology can help tackle rising costs
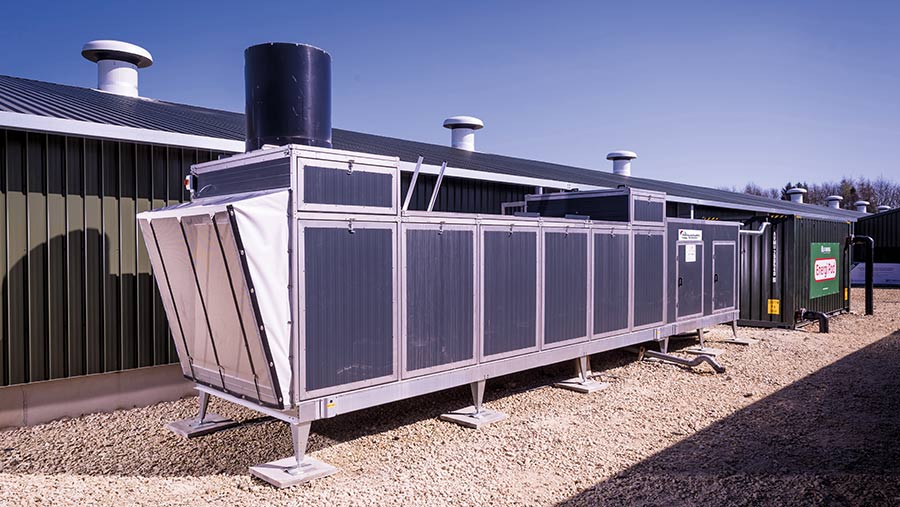
Poultry producers are enduring crippling costs and are desperate to see some of the risk move up the supply chain as they attempt to engage with retailers. So what can they do address costs in the meantime?
While there are no easy answers to improving returns for the poultry sector, technological developments that could contribute to cost cutting continue apace.
Experts speaking at the recent Pig & Poultry Fair highlighted the following four areas where these advances have the potential to benefit a producer’s bottom line.
See also: 13 things every poultry farmer can do to save energy
1. Reduce reliance on gas
A heat exchanger could cut gas consumption by 55%. The heat exchanger takes hot, stale air out of the poultry shed and returns recovered heat, which means less gas is burned.
Heat exchangers are seeing a rise in popularity according to Dalton Engineering sales director Gary Walker, who explained how the heating market has changed.
Heat exchangers were more popular than biomass boilers and there was grant funding available to encourage their use.
But the government switched that support to fund biomass boilers, which saw demand for heat exchangers all but cease overnight.
“Now it has come full circle,” said Mr Walker. “The price of wood pellets has gone up so there is no advantage to burning them.
“With the price of gas rising fast, poultry and egg producers are now, once again, installing highly efficient heat exchangers.
2. Cut feed waste
Ordering too much feed creates waste as stale feed has to be disposed of. Even before it reaches this stage, flock performance could be hit because feed nutritional quality reduces over time.
Conversely, ordering too little is inefficient and adds costs through having to fast-track orders or taking whatever the market happens to be when the bin runs out.
Keeping a tighter rein on stocks is possible by retrofitting non-invasive, strain gauge weighing systems, which can be installed on the silo legs.
These provide alerts to flock managers when feed reaches a pre-determined level in the bin. It is then time to start negotiating a price and ensuring feed is delivered at the optimum time.
Among the manufacturers producing silo monitoring systems is Collinson.
Managing director Sam Collinson said the firm’s offering is a telemetry system, where data is transmitted to the cloud and can be viewed on a meter local to the silo or via an app.
Systems start at £450 and can be installed in under 30 minutes.
3. Make sheds more efficient
Another area where poultry sector costs have soared is in shed and equipment replacement.
One farm building and equipment firm suggests it can cost £3-£8/sq ft to refurbish a shed, whereas a complete new build would cost at least £22/sq ft.
There are also tax advantages to refurbishment, said Stephen Jaques, managing director of Jaques INT.
There is 100% tax relief available on a repaired building, and if the cost involves removing asbestos, this goes up to 150%.
“It can cost up to 60% more to build from scratch, compared to the average refurbishment. That makes the latter a viable option to many who need to improve efficiencies within tight budgets,” Mr Jaques said.
Not all poultry houses can be refurbished, however, and Mr Jaques listed some key considerations before embarking upon a project:
- A damaged floor often means a shed will need a total rebuild
- The height of the eaves – buildings can be increased in height for modern machinery
- Economies of scale with existing floor space
- Does the building contain asbestos?
- Red Tractor standards and RSPCA assurance schemes – existing building specifications can be modernised to meet current welfare requirements
- Insulation levels – quantities can be increased
- Fixtures, fittings and ventilation
- Additional biosecurity measures
- Planning should not be required.
4. Track and manage bird health
Measuring flock performance more closely with better data analytics can help managers to tailor inputs and make improvements, according to animal health firm Elanco’s Tom Hepburn.
Mr Hepburn highlighted Elanco’s health tracking system (HTSi), which considers a number of data feeds to provide a simple score for managers to base decisions on.
The programme generates an intestinal integrity score known as I2, which takes into consideration 23 intestinal health lesions.
These include infections such as coccidiosis, to give a score of between zero – poor gut health – and 100, optimal gut conditions. A score of 90 or below indicates poor intestinal health.
For every one unit increase in I2, average daily liveweight gain increases by 0.04g and feed conversion rate improves by 0.13 points, he explains.
A poultry company producing 100 million broilers a year could therefore see an income boost of £572,000 by improving its I2 by just five points.
Even on a smaller scale, it is possible to make more efficient use of feed by concentrating on gut health, Mr Hepburn said.
How are retailers responding?
Keen to engage in discussions with retailers about the need for higher consumer prices, the British Free Range Egg Producers Association (Bfrepa) asked representatives from Tesco, Asda, Morrisons, Sainsbury’s, Aldi, Lidl, Marks & Spencer and Waitrose to attend a Breaking Point Summit at the Pig & Poultry Fair (10-11 May).
But while Tesco and Morrisons discussed the issue with the industry outside of the event, and responded positively, the others did not attend or respond, according to Bfrepa chief executive Robert Gooch.
Although one or two of the retailers who initially failed to respond had acknowledged earlier letters, they had so far offered no constructive help on how egg producers could deal with the cost crisis.
“From our own research, there is some small movement up at retail level, but we need prices to increase by 40p/doz for free-range and 80p/doz for organic,” said Mr Gooch.
A recent Bfrepa survey indicated that more than 70% of producers will leave the industry within a year if a price rise is not forthcoming.
Adas livestock consultant Jon Walton explained how costs had risen massively in the past 12 months.
“Egg prices have increased by 3.1p/doz and returns have increased by the same amount, but total costs, excluding finance, have increased from 91.7p/doz to 117.6p/doz – up 25.9p/doz.
“Producers need a feed tracker contract,” said Mr Walton. “However, this doesn’t address all costs such as labour and energy, which are also rising rapidly. Egg prices need to go up.”
There are also concerns that while some retailers are offering feed tracker contracts, these are not being passed on by packers to egg producers.
Broiler producers are also suffering the effects of high costs, said British Poultry Council (BPC) chief executive Richard Griffiths.
“There is no escaping it, everything has gone up. It affects feed, fuel, labour, energy and water. Feedwise, availability is OK – it is the price that’s the problem,” he said.
“In the short-term there is little we can do to mitigate cost. Fuel prices are still rising – I can’t see a point where they will level out at the moment.”
Although there are areas businesses can look at such as feed conversion rates and other efficiencies, in such a volatile arena it is very difficult, he added.
“BPA (BPC??) members are in discussions with retailers about pricing and we will soon know the result, which will hopefully lead to an increase.”