Banham Poultry ‘future proofs’ new broiler sheds
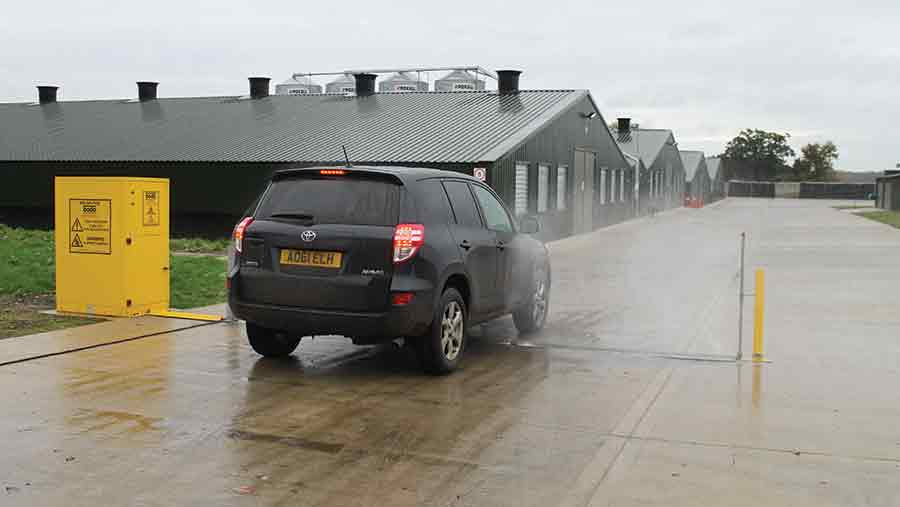
Increasing demand for poultrymeat has triggered expansion for Banham Poultry – and that means new poultry sheds.
Gaining planning permission for any new poultry shed requires attention to detail and a commitment to high standards.
But when your farm is next to a stone curlew breeding area and a Site of Special Scientific Interest, then you really have to pull the stops out.
That has certainly been the experience for Norfolk-based Banham Poultry, which has been rebuilding a number of broiler units at East Wretham, just to the north of Thetford.
Banham Poultry
- Privately owned integrated business supplying Morrisons and Aldi
- 30% of farms sheds are under 10 years old, 60% are under 15 years old
- 43% of throughput from owned farms, 33% from rented farms, 24% from independent growers
- All farms audited for biosecurity three times a year
- Two hatcheries producing 600,000 chicks a week
- 120,000 chicks a week bought in
The aim throughout the redevelopment of Middle Farm – one of a number of former Buxted Poultry sites in the area – has been to “future proof” it.
But there has also been an emphasis on working closely with the Environment Agency and Natural England, to secure smooth passage during the planning process and beyond.
“The EA was especially concerned about ammonia emissions, so we have included a number of measures to keep on top of this, including an ongoing monitoring programme, with a report submitted to the EA after every crop,” says Bob Waterson, special projects manager with Banham.
Another example is when bats were discovered during the demolition of the derelict manager’s house.
“After approval of a European protected species licence, the bats were moved into a purpose-built loft in the new manager’s house, creating a path approved by Natural England for the development to continue.”
Keeping the statutory consultees on board has been a top priority. But ultimately it is all about customer satisfaction – providing the public with chicken that is affordable, yet meets all the animal welfare and food safety expectations. And that means getting the design right.
“Throughout the design process, we have looked around the whole industry – including our own farms – to find out what works and what doesn’t,” says Mr Waterson.
While he acknowledges that selecting bespoke equipment means additional cost – about 10% more, he suggests – this is justified in terms of improved bird performance, fewer complaints from neighbours and reduced disease pressure.
Middle Farm features
Fencing. All manner of intruders pose a threat to poultry farms, from vermin and wild birds, to burglars and animal rights activists. A sturdy fence and locked gates send out a clear message.
Entrance. Once through the gates, automatic sensors ensure all vehicles get a good disinfection – underneath, as well on the sides.
The run-off is collected and disposed of with other wash water at turnaround. Generally, vehicles are encouraged to park outside the gates, and a footpath takes visitors past the sprays to the farm office.
Changing room. Once signed in, all staff and visitors are required to shower and don farm-specific clothes and footwear.
A metal swing barrier has been installed, at the vet’s suggestion, to reinforce the message that personnel are entering a high biosecure area.
Control room and barriers. Each control room serves two sheds. Boot dips are kept indoors, as this has been found to be more effective than leaving them outside.
Plastic barriers with sliding seats are situated on either side, to make it easier to put on plastic boot covers before going through to the chickens.
There are also hand sanitisers, a basin for a hot hand wash and the room has contained drainage and Altro flooring – a food grade material designed to resist bacteria.
Controls. The control panels at Middle Farm have been purpose-built by specialists Bowden and Knights, based on POLA HP36 units for ventilation and POLA HP12 for fans and alarm.
The same system is being rolled out across all farms in the group. One panel controls the ventilation, heating, lighting and windows, while another monitors ammonia, CO2, air temperature and humidity.
The aim is to achieve continuity and simplicity, so that any stockman on any company farm can recognise and operate the system.
Banham does not employ handheld devices – “we want our managers to look in the shed before changing any settings” – but all data is fed back to the manager’s office and head office.
Windows. All the sheds at Middle Farm have windows – but not just any windows. All are double-glazed, all have rack-and-pinion operated shutters and all the shutters are insulated, to maintain the integrity of the shed.
Heating. Wood pellet biomass boilers from Danish manufacturer Passat provide the heat for new arrivals at Middle Farm – indirect heating being a vital part of the ammonia control strategy.
Each boiler is capable of 210kW and heats two sheds. Wood pellets have been chosen over wood chip as they have lower moisture and produce less ash.
They can also be fed via feed bins, providing an integrated appearance with the rest of the farm. The heat is distributed from suspended radiators, while Hired Hand propane burners provide the back-up.
Banham rejected underfloor heating, having studied it in Holland, as it can create hot and cold spots, and exacerbate capping of litter.
Ventilation. The ventilation set-up is based on side inlets with ridge extraction – but with a difference.
To satisfy the Environment Agency, the system also has an accelerator vane in the ridge chimneys, to discharge air at 10m/sec and throw it as high as possible, to maximise ammonia dispersal.
Each shed also has tunnel ventilation to help cope with summer weather, with Zeal fans at one end and shuttered inlets at the other. This can move air at 3m/sec.
Feed and water. The farm incorporates Roxel feeders and Lubing water lines and nipple drinkers.
Dimensions. Each of the eight Moorspan sheds at Middle Farm measures 66ft x 300ft and houses about 40,000 birds.
This is considered the optimum width, as going wider would require thicker, more expensive steel. The sheds are also easier to ventilate than wider sheds, litter is kept in better condition and catching is more efficient.
Accommodation. The farm manager is provided with a quality, four-bedroomed house. Good accommodation equates to satisfied, loyal staff. Middle Farm also provides an identical assistant manager’s house, with the intention that the farm will become a training unit for new recruits.