Crown Chicken: a model of integrated production
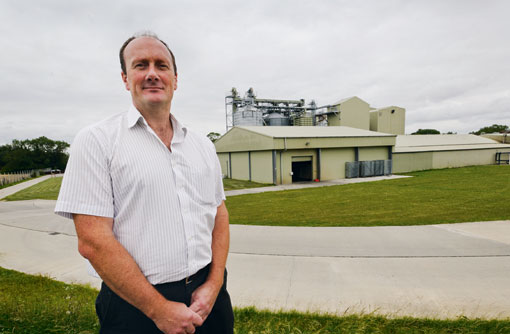
Crown Chicken has enjoyed steady expansion and picked up several awards since its launch, as Scott Casey finds out
It was in May 1993’s Poultry Would that the birth of Crown Chicken as an independent concern was first announced and Matthew Ward, agricultural director at the integrated feed, chick and broiler producer still carries his copy to prove it.
“For nostalgic reasons I kept it,” he said, flicking through the magazines’ dog-eared pages. The pictures featured in the issue still hang in the office lobby of Crown’s headquarters near Norwich.
In the 18 years since then, Crown has grown from processing 185,000 birds a week to 370,000, selling a further 25,000 live birds a week on top of that, and hatching 460,800 eggs per week.
Despite this growth, the physical spread of the business has actually decreased over the years, with rationalisation leading to fewer farms producing larger numbers of birds.
“In today’s world, for a broiler site to be viable it’s got to be able to do 200,000 birds, otherwise there’s not a lot of point to it,” said Mr Ward.
“In 18 years, we’ve bulldozed and sold off about five farms, and we’ve taken that money and reinvested it. They were in the wrong location and capable of being sold off as building plots, while we had spots where there was the opportunity to expand and build more sheds.”
The company still has some sites where the sheds are 40 years old, or more. “If we made the profits the supermarkets do, then we’d knock them down and start again,” he said.
Renewable energy
Tight margins aside, Mr Ward sees a great future in the business, with renewable energy one area which interests him.
“We’ve got the problem of energy costs going up and up. But what are we going to do? Are we going to put solar panels in? Are we going to be burning litter to produce our own heat?
“Ultimately if everyone puts solar panels on chicken sheds and are not buying gas anymore, we’ll have a cost saving – and then the supermarkets will want that benefit as well.
“But if we don’t do it, then we’ll be at a disadvantage to the person who does do it, so it’s a survival game isn’t it?”
He does admit that Crown’s growth over the last 18 years has now reached a crossroads, where to expand any further would be a considerable undertaking.
“Right now in terms of our factory size, we have gone as far as we can without a massive spend, increasing refrigeration space and killing time,” said Mr Ward.
“We’ve probably got to do a ÂŁ5m investment and then we could do a 50-100% expansion. But then we’d also have to expand the breeders and the hatchery. We will expand, but slowly.”
Hatchery and breeders
Crown prides itself on its integrated method of production, controlling almost all aspects of poultry production from feed mixing to breeding, hatching, growing and slaughter.
Each week 460,800 eggs are placed in the hatchery, supplied from 10 breeder production sites – the 10 breeder sites being supplied from two breeder rearing facilities. The broiler chicks are then placed on 20 broiler farms in Suffolk and Norfolk
Mr Ward believes rearing is one of the areas where the most change has happened since the early 1990s.
“If you go back to the 1980s, the rearing side was predominately done in rubbish sheds. Money was being spent on broiler farms and the industry was growing every year,” he said.
“The breeders were just left with the old sheds that were left behind. So about 10 years ago we found some farmers who wanted to invest in something else and we persuaded them to put up rearing sites.”
Crown now operates 10 breeder farms – four 10,000 bird sites and six 15,000-20,000 bird sites – with seven of the sites in lay at any one time.
Feed
The company’s milling operation has also transformed since the early days with their mill capable of producing 4000t a week of feed, half of which goes to local pig producers rather than Crown’s chickens.
“We are a chicken business with a feed mill on the side. We’re in total control of what we do (with the mill), we can respond to raw material changes very rapidly,” said Mr Ward.
“With our production, if we think it is right to save ÂŁ10/t on the diet, but it affects the feed conversion rate, but we’ve done the maths and we think its right, then we haven’t got to worry.”
Awards
The breeding operation has also come in for praise from genetics companies, with Crown winning the Ross UK Flock of the Year 2011 award from breeding company Aviagen.
Manager Les Able, who has worked for the company for 26 years, produced the winning flock close to Crown’s headquarters, saying “a bit of luck” was involved in his success.
“I think you’re always learning in this game and we need to get it right. If it’s wrong, you can mess the birds up. You need to rear them properly and then hatch them all right,” said Mr Able.
“Our latest flock is almost as good as the award-winning one and we might get the same result if things go well in the next 15 weeks. We might be in the running for another award. That’d be nice.”