Indirect heating leads to environment improvements
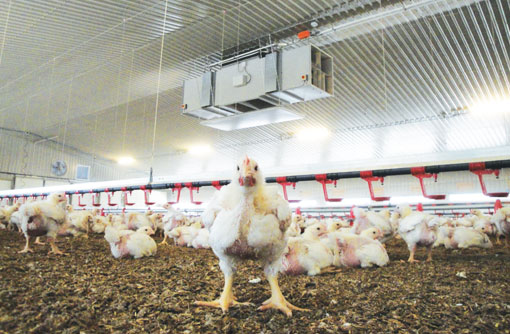
Broiler growers should consider the benefits of installing a dual ventilation system to achieve the right environment for their birds, believes Ian Griffin of environmental specialist the Draper group.
“The biggest challenge in the UK is the climate,” said Mr Griffin at a recent workshop for broiler growers.
Most of the systems that were offered off the shelf were developed for a wide range of customers across Northern Europe, he said, but UK climatic conditions were outside that range.
“On top of the challenge of the UK’s maritime climate, the criteria for rearing birds within a confined poultry shed environment varies dramatically as they grow,” said Mr Griffin.
“This means that a single traditional fan/inlet ventilation system is unable to deliver,” he claimed.
Burning a litre of propane within the house required 15.5 litres of fresh air to supply the necessary oxygen. This gave rise to three litres of carbon dioxide plus other noxious gases and 1.6 litres of water, “all of which sink to the floor with the chicks.”
Chicks were highly sensitive to CO2, he said, so there was an immediate need to start ventilating the heat away.
The answer, he claimed, was to use indirect heating, using hot water in custom-built radiator panels.
The hot water could be generated using conventional fuels such as LPG, or renewable systems such as biomass boilers.
“Carbon dioxide levels of less than 3,000ppm can only be achieved if combustion is removed from within the shed.”
Without the generation of CO2, ventilation rates could come right down, and much less heat was required.
“Using indirect heating, CO2 levels will only start to rise from three to five days, at that point requiring freshening with outside air.”
The complete answer was to provide a two-stage ventilation system, with the first comprising positive air pressure within the house, using fans to push air into the building and out through small openings, combined with indirect heating and gradual frequent transitions in environmental control settings.
This can then be followed by a conventional negative pressure system, with fans pulling air out of the building, featuring a higher capacity, but less fine control.
The transition between the two stages should occur between 21 and 28 days, and is a critical period when litter quality was often lost with excessive moisture content.
“Ventilation rates increase during this time, with larger volumes of cool moist air entering the shed. The heating that would dry this air is withdrawn as birds develop, leading to increasing moisture levels,” explained director Paul Draper.
At 21 days the birds were not fully feathered, so it was important to avoid too rapid a transition to a “coarse” negative pressure fan system, to avoid health problems that would add to the moisture drop by the flock.
“After 28 days, temperature is primarily driven by the body heat of the flock, and large volumes of air need to be extracted to hold temperature and remove moisture.” However, the position of inlets, and their profiles, was still critical to get a suitable air movement around the house, said Mr Draper.
For the first positive ventilation stage, Draper had developed the dedicated Min-Vent unit which drew in air through special roof units, where it was mixed with the warm internal air in a mixing chamber, and then passed over the radiator coils before being distributed around the shed. Correct placing of the units should ensure even temperature distribution around the house, said Mr Draper.
For the difficult post-21 day period the Min-Vent system should be used for as long as possible, especially for night-time ventilation, to minimise the effects of the outside air and keep the litter dry.
Case study: Three-stage ventilation system
Ian Johnson grows 80,000 broilers for Moy Park in three sheds near Ashbourne, Derbyshire, with his wife Sarah. He has installed the Draper Min-Vent units in one of his 30,000 bird sheds, and operates a three-stage ventilation system.
Mr Johnson uses a positive pressure system for brooding chicks, standard negative pressure ventilation for older birds, and tunnel ventilation for hot weather.
To avoid problems with planning permission, he opted for all the extraction fans to be located in one end wall, rather than employ roof fans for normal ventilation, to avoid concerns over dust and light pollution.
As a former area manager for Dove Valley poultry wholesalers, acquired by Moy Park in 2004, he believes strongly in creating the optimum conditions for the birds while monitoring costs as closely as possible.
Any environmental management system needs to make clear the cost of running it, he says.
“You can create perfect conditions, but what’s the cost going to be?” said Mr Johnson.
He claims that the gas consumption with the Min-Vent brooding system in the 30,000-bird house is the same as in the smaller conventional house next door with just 20,000 birds. In addition, he was gaining 100g a bird live weight by keeping the CO2 levels low.
The post-brooding ventilation system operates with three smaller fans in one end wall for normal weather operation, augmented with a bank of bigger fans to produce rapid air movement for tunnel ventilation on the hottest days.
“For six months of the year, however, we don’t take the covers off the big fans.”