Poultry Profile: James Hook
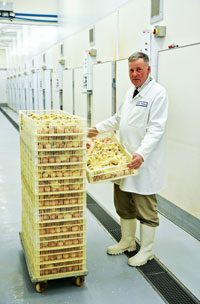
How long have you been involved in the hatchery business and where did it all begin?
My mother started the P D Hook business in the 1950s, when the broiler sector was in its infancy. My father was milking cows and my mother started a small brooder house and hatchery in the stable to supply chicks to local farmers. My father then got out of milk in the 1960s, as he could see there was more money in poultry, and I came into the business in the 1970s, by which time we were producing 200,000 chicks a week.
But then in the 1980s we lost a major contract, and then salmonella struck. We were down to just six employees and on the verge of closing down. But we did not have much to lose, so took the risk and invested, promoting ourselves as “salmonella free”. That attracted Marks & Spencer, things started to grow again and we got more customers. In many cases we offered long terms of credit and we would only get paid for our chicks once the fully grown broiler went off for slaughter. But that helped secure customer loyalty.
And where is the business today?
We are now the country’s leading independent hatchery, producing over 5m chicks a week. About 2m of these are produced at our main hatchery at Cote in Oxfordshire – the rest at our other sites at Great Yarmouth, Gunness, Dalton and Kentisbere. We produce about half of our own eggs, and the rest come from contracted breeders.
About half of our chick production is for our joint venture, Hook 2 Sisters, producing broilers on rented sites for the supermarkets. The other half is for about 20 or so independent customers and integrators with no hatcheries, including Moy Park.
How do you view the market right now?
Demand for chicken is excellent and the supply of eggs and chicks is tight. All our customers want more day olds. We’ve increased production by 1m a week over the last year as customers opt to grow smaller birds. Chicken is the meat of choice in harder times. Currency has also been in our favour, protecting us from imports. One of the biggest problems we face is a lack of growing space on broiler farms.
But we desperately need a price rise from the retailers. Chicken is still being sold off cheap, so it’s not easy. But our feed bill has increased by ÂŁ500,000 a week and that is money we can’t just find in reserves.
How else could retailers help?
The current ban on GM feed in poultry production is unsustainable, and is putting significant extra cost on broiler production. We can’t just refuse to abide by it, as the retailers would go elsewhere for their chicken. But we can try and negotiate our way out of it, arguing that food security is important and current premiums for GM-free soya are putting that at risk. We could also do with getting meat and bonemeal included back in poultry rations.
How do you see the longer term future of broiler production?
We have the capacity to produce a lot more food in this industry. The broiler sector can move fast and produce big numbers of birds quickly – unlike beef and sheep. We can produce seven crops of chicken a year. We need to tell people about this, so they understand the value of modern poultry production.
And what about value added and organic production?
We were very much behind the launch of Oakham chicken for M&S, and Willow for Tesco. Sales of both have been declining as consumers have had to tighten their belts. Organic poultrymeat sales have also gone backwards. They could pick up again, but will always be a niche. This end of the market is volatile and we don’t like that. We prefer commercial production, with lower margins, but bigger volumes.
What has given you most satisfaction in the poultry industry and why?
The first week we hatched a million chicks, as that had been our long-term goal.
How did it feel to win the 2010 Poultry Man of the Year?
It was the proudest moment of my life in the poultry industry.
THE COTE HATCHERY
Some 25 breeder units supply the Cote hatchery, with eggs collected from each twice a week. None of them are more than two hours away. About 60% of the fertile eggs come from P D Hook’s own farms, with another 20% from contracted breeders and the remaining 20% from Moy Park in Northern Ireland. “Over the year’s we’ve stepped up our own egg production and now we have a good mix,” says Mr Hook. “Most of our farms are just under 40,000 hens. The ideal site is one with four lots of 10,000 birds. Having large batches like this is good as it keeps down the number of flock codes producers have to keep. It also means we can produce large numbers of chicks of equal size. This is crucial when they go on to the broiler farms, so they have equal access to the nipple drinkers.”
The eggs arrive on pallets of 4752 eggs, with 24 trolleys on each lorry. Each egg carries the stamp of the original breeder and the date.
On arrival, the eggs are kept in the store room at a temperature of 16C for up to a week. “If they are held for longer we lose hatchability and it also affects chick quality,” says Mr Hook. “Our average hatch rate is about 80%.”
From the store room, the eggs are transferred to the multi-stage setters, where they are kept for 18 days at 37C and 80% moisture. They are turned automatically every hour, before being transferred to the hatchers for the last three days. This process involves the eggs being removed from their trays by robotic suckers and placed into deep sided white plastic trays for hatching. There are three hatching rooms, with 400,000 chicks per room – and 24,000 chicks per machine. The conditions are a bit cooler and a bit wetter, to help them hatch.
Each morning, once hatched, the chicks are moved to a sorting room, where a team of workers removes them from the white hatching baskets and sorts them into new blue baskets for dispatch. Chick processing is done at a rate of about 40,000 per hour along three conveyor belts – “Alton Towers for chicks”, Mr Hook calls it.
They are put into blue plastic crates at a stocking density of 125 per box. If necessary, the chicks are also sexed – at a rate of 3000 per hour – and all chicks are spray vaccinated before being loaded on to lorries, which take between 30,000 and 60,000 to the broiler farms.
Meanwhile, the hatching room is steam cleaned and made ready for the next inflow of 400,000 eggs from the setters, waiting to be hatched.
Four lorries a day arrive with eggs at Cote hatchery and 10 lorries a day leave with day-olds.
“The whole operation is very efficient,” says Mr Hook. “We always try to set eggs to order, but we also try to be flexible as things can change quickly. As we grow half of our chicks on our own farms under the Hook 2 Sisters joint venture we can divert any surplus birds quite easily.”
As for breed, Cote used to deal exclusively with Aviagen stock. “But now we are about 50% Aviagen (Ross), 40% Cobb and 10% Hubbard,” says Mr Hook. “In my opinion, the Ross is the best bird if you can get it to work, but it is also the hardest to manage. The Cobb is a bit lighter, but it’s easier to replicate. You get fewer eggs, but the hatchability is better – about 90%. The Hubbard is for our speciality customers who want slower growing and free-range birds. All the birds on our own broiler farms are now Cobb.”