Where to invest when building or upgrading poultry units
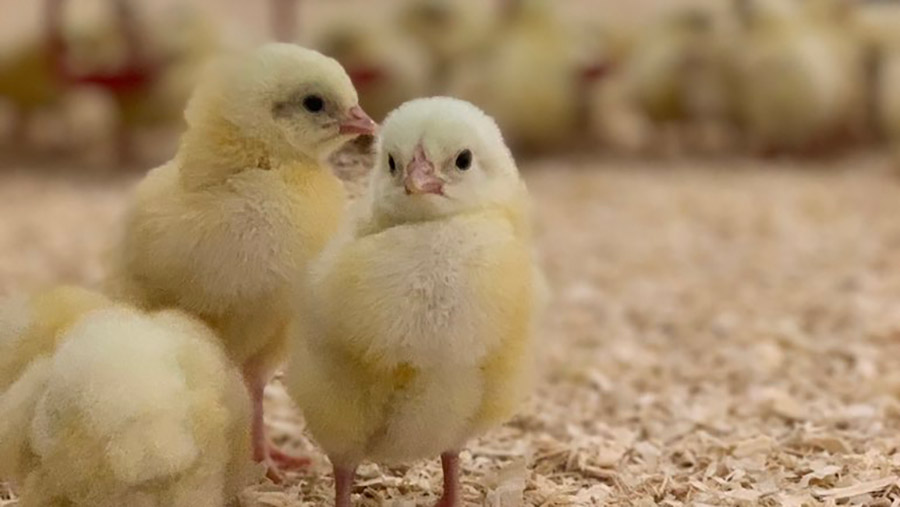
What does it cost to create a state-of-the-art poultry unit? We ask one arable farmer-turned-poultrykeeper to break down the key investment areas for anyone who wants to overhaul part of a building or start from the ground up.
Fourth-generation arable farmer Will Oliver received his first crop of Ross broiler chicks 14 months ago at Elms Farm, signalling a £3.6m diversification into poultry.
The 800ha farm is now run as a mixed arable and broiler production enterprise, with hopes of further expanding the business into poultry housing consultation.
See also: How to manage poultry housing environments in winter
Broilers offered distinct advantages over other diversifications as the business sought to future-proof itself post-Brexit.
“We had been looking at ways to improve the organic matter content and condition of our arable soils – we could see the value in producing our own source of nutrient-rich organic matter from poultry litter,” says Mr Oliver.
Broilers also meant a quick turnaround, renewable energy incentivised options, and productive use of an otherwise unused part of the farm.
Process and planning
The family started the planning consultation in July 2018, and approval was granted the following April. “The planning process went smoothly with Ian Pick Associates consulting,” says Mr Oliver. “I know planning can be a real frustration, that is why we opted for a private consultant.”
The main changes required were environment and traffic related. “We did have to build an attenuation pond to hold rainwater run-off for a period before entering the ditches,” he explains. “We also had to consult with the highways department and improve our gateways to support a rise in traffic.”
Cost: About £84,000 plus an application fee of £8,000 for an Integrated Pollution Prevention and Control permit
Groundwork
In April 2019, principal contractors from Knights Construction began the groundwork. They installed two underground dirty water tanks, giving the site capacity to hold up to 100,000 litres. The site was concreted to support heavy vehicular traffic and for better biosecurity management, covering 10,000sq m.
Cost: £740,000, including principal contractor/health and safety/worker welfare
Buildings
The site houses four 110x20m steel frame sheds that hold 48,000 birds each, and have individual control rooms.
Powell & Co Construction undertook the design and construction, says Mr Oliver. “When planning the external design and location we took into account things such as wind direction – to help with ammonia removal from sheds – and how they would look in situ.”
Other structures include amenity buildings; a plant room, a gatehouse (office, kitchen and biosecurity portal), and an incinerator. “We did over-spec but it allows for expansion in future.”
With time constraints to complete construction Mr Oliver wanted contractors who could deliver the build on deadline.
“The contractors we used could also do the internal planning and install the ventilation and the internal equipment – having fewer people managing different projects did simplify communication and things coming together.”
Cost: £810,000 for housing, including amenity buildings
Solar power
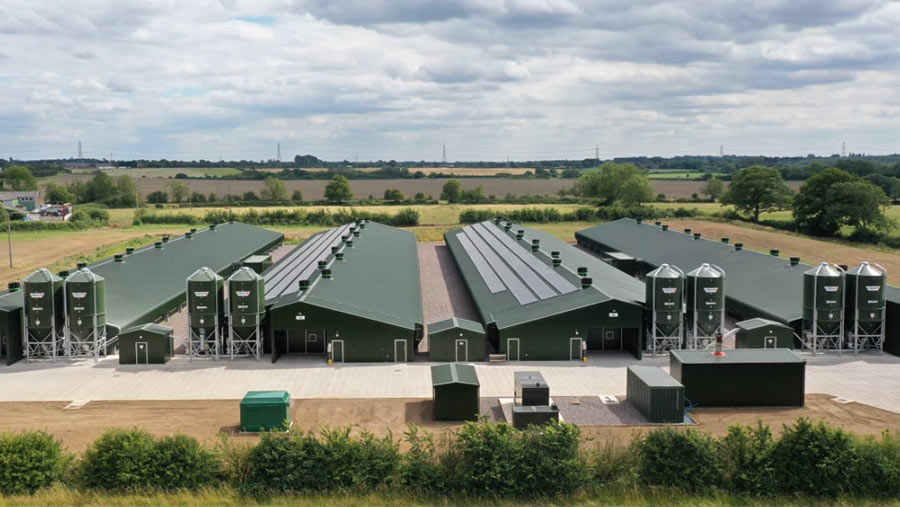
Solar panels help power the sheds’ ground-source heat pumps © Will Oliver
Mr Oliver opted for a 250kW solar installation, with panels on two of the four poultry shed roofs.
In total, these generate 206,610kWh/year of electricity, which is used to help meet the energy demands of the ground-source heat pumps installed in all four sheds.
The panels, which were the last thing to be installed on the site, have saved about £27,986 on energy bills in the past 12 months.
Cost: £183,000 for solar panels, including installation
Heat
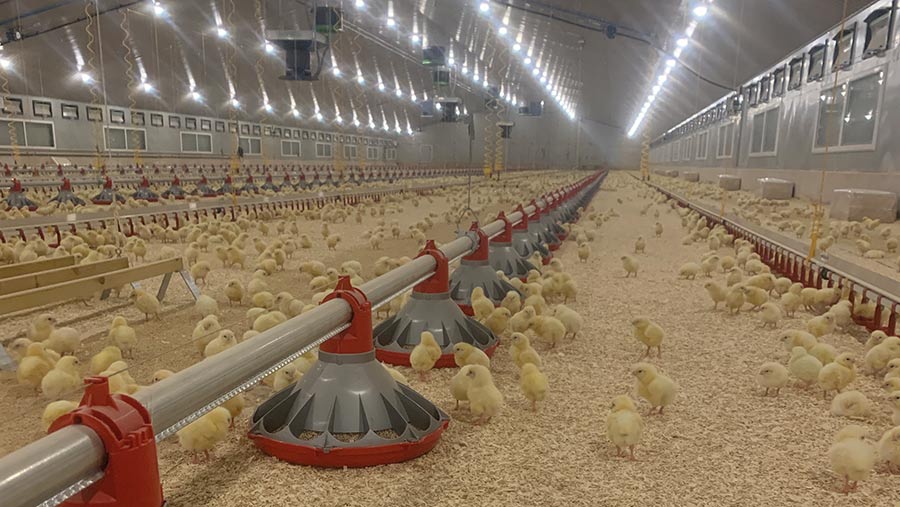
Used litter is recycled for high-quality manure for the farm’s arable crops © Will Oliver
A 960kW ground-source heat pump provides underfloor heating, and can also cool all four sheds in hot weather.
“Heating the shed before chick placement is really important for uniformity, mortality and finished bird weights,” says Mr Oliver.
Cold concrete is difficult to heat up and prone to condensation when using conventional heating. The ground-source heat pump is an effective way to heat the floor without having to burn excessive amounts of fuel.
It also reduces ammonia levels caused by wet litter, and carbon dioxide levels from burning fuel to heat the shed. The litter produces a high-quality manure for the arable crops, saving the farm £43,000/year on fertiliser.
The heat pump is cheaper to run, too, with the electricity demand helped by the solar panels and an annual £118,000 return through the Renewable Heat Incentive.
Each shed also has a conventional heating system as a contingency plan. All heating and renewables were supplied by Bavenhill.
Cost: £712,000 for ground-source heat pump, including underfloor heating in all four sheds
Ventilation
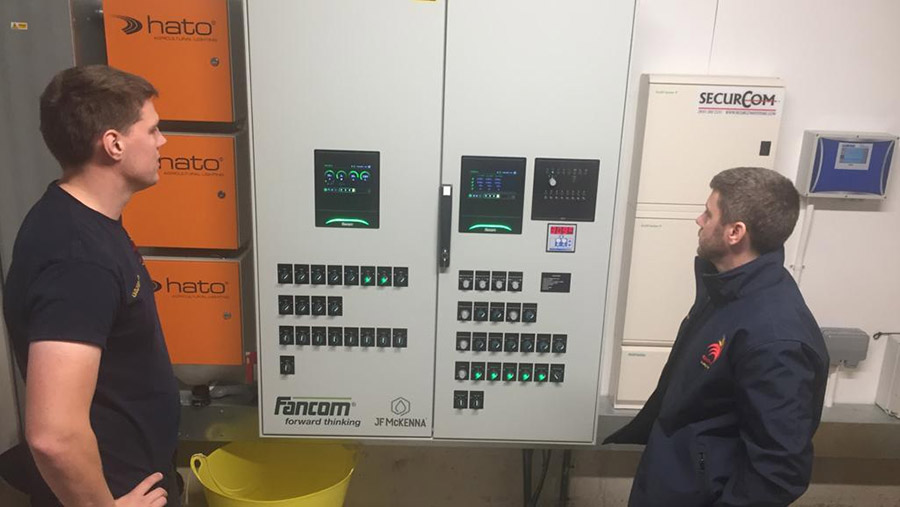
Will Oliver (left) and farm manager John Jevons take regular readings from the climate-control units © Will Oliver
The four sheds are kitted out with equal-pressure combi-ventilation systems with a capacity of 561,660sq m/hour. That capability can purge and replace all of the air in a shed in one minute.
The Fancom control centre automates the ventilation system by linking it with the LED lighting system and data from internal environmental sensors, including temperature, humidity, carbon dioxide, and ammonia, as well as external weather sensors.
Each shed has 138 side inlets, 12 roof chimneys and eight belt-driven fans at the gable end. The climate-control units are kept in the control room to prevent dust and moisture getting inside them.
To make sure data being fed back to the climate control unit is correct, the staff take manual readings regularly.
Cost: £58,000 a shed for ventilation equipment
Feed equipment
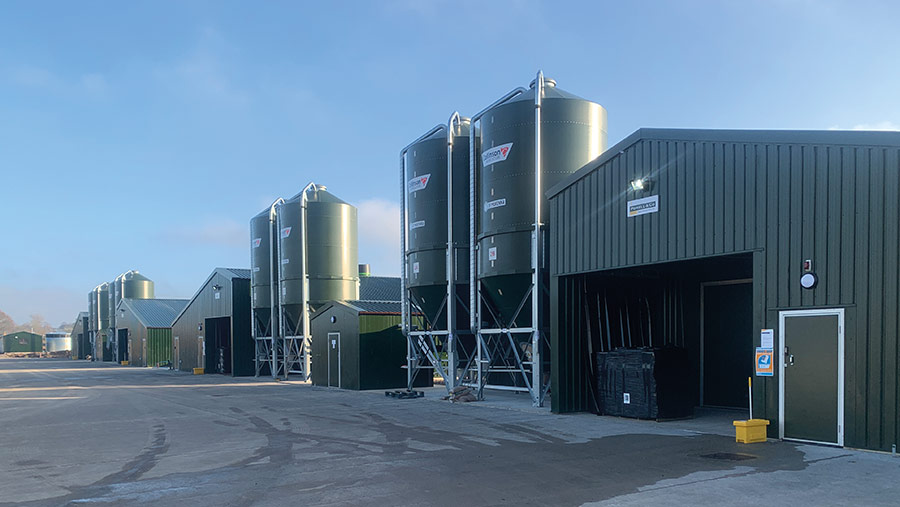
Feed is stored in 31t Collinson feed silos, sited next to the sheds © Will Oliver
All of the internal equipment and feed silos were sourced from JF Mckenna. “You could pay less if you shop around, and it might spread a bit of risk. But we liked our supplier and it simplified ordering, installation and the admin of the build to source everything from them,” says Mr Oliver.
Each shed has 560 Chore-time pan feeders suspended from four rows, which allows a stocking density of 89 birds a pan.
Reduced feed intakes and gut health problems such as coccidiosis can be caused by contaminated feed, so Mr Oliver opted for a pan feeder with a guard to help with hygiene and reduce feed waste.
The pans are also good for day-old chicks. “We still use chick paper as well, but a combination in those first few days makes sure feed is in front of every chick,” he says.
Feed is stored in eight Collinson 31t feed silos. “We buy in feed but also use our wheat as a bulking agent – about 60t of wheat is consumed per crop.”
“Most people will put the silos away from the sheds to reduce the risk of contamination from feed lorries. But I wanted everything to be as accessible as possible and placed them immediately adjacent to the sheds.
“I opted to install a wheel wash connected to the mains water, which automatically cleans vehicles as they come on site. The mains water means it’s a constant and reliable way of managing biosecurity.”
Cost: £64,000 (£16,000 a house) for feed equipment, including weighing and blending system, augers and pan feeders
Water equipment
Mr Oliver installed 20 Lubing drinking nipples per 3m section of shed, across six lines of Lubing drinkers, which allow a stocking density of 11.9 birds for each drinker. There is also an auto-flush system, giving greater control over hygiene and bird health.
“This cost us an additional £3,000 a shed but it means we can keep drinking lines clean and free from harmful pathogens,” he explains.
Any medications and vaccinations can be put through the drinkers, too, and residue can be flushed out after treatment.
When installing a drinking system flock-keepers should check the existing water supply is sufficient and that there is a backup tank in case of disconnection.
Cost: £68,000 (£17,000 a shed) for water equipment, including drinkers, electric winches and auto-flush system