Slurry separation options compared
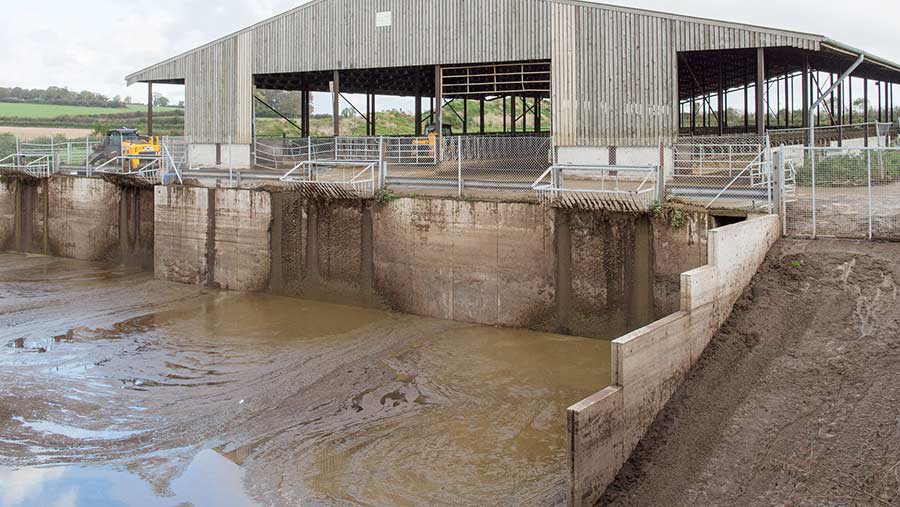
Dairy farmers are investing in slurry-separation systems amid tighter environmental controls.
Balanced with the cost of increasing storage infrastructure to be compliant with nitrate vulnerable zone (NVZ) regulations, separation technologies can offer an affordable solution to managing slurry.
Separating the solids and liquid not only reduces slurry volume, but the potential for pollution too.
See also:Â Guide to safe storage and spreading of slurry and fertiliser
Several technologies are available, each with different approaches to achieving similar results, and range from mechanical separators, capable of recovering nearly three-quarters of the solids in slurry, to membrane systems that produce nutrient-rich solids.
Which of these offers the best solution for an individual farm depends on several factors, including slurry type and volume and the end product required.
Budget and operational costs are also a consideration – for instance, models with a higher separation performance are mostly more expensive to run because they consume more energy. And some require more labour input than others.
Farmers Weekly takes look at what the different systems offer and asks manufacturers to give the lowdown on their topsellers.
Different types of slurry separators
Type one: Screen separation
How it works
Slurry is pressed against a screen made up of specified pore sizes that allow only particles of a certain size to pass through.
This typically produces separated solids of 18-30% dry matter.
Screens vary according to the model – the three most common are stationary screens mounted on an incline, vibrating screens and rotating screens.
1. For stationary screen equipment, slurry is pumped to the top edge of the screen and from there liquids pass through it while solids fall to the bottom.
This system is popular because there are no moving parts and the pump is the only power requirement. However, it can be prone to clogging, so careful maintenance is needed.
2. In vibrating systems, the liquid drains through a vibrating screen and the solids collect on the edges of that screen. This system is semi self-cleaning, but requires power.
3. Rotating screen models work on the principle of slurry being fed into the top of the unit and through a spinning and perforated drum. The liquid passes through the holes in the drum while the solids gather in a collecting area.
This design is noted for its lack of clogging in the screen pores.
Type two: Press separationÂ
Mechanical pressure is applied to the slurry material by either roller, belt, screw or filter presses, allowing the liquid to pass through a filter or screen while the solids are retained.
This approach can achieve a high level of dewatering, producing pressed, solid material.
With filter press systems, buyers can specify the size of the filter depending on what proportion and size of material they want to remove.
Type three: Membrane separation
This method of separation can be highly effective and has the potential for greater control over the composition of the end products.
Slurry passes through a series of membranes, each membrane containing smaller-sized pores than the last. Target particles including nutrients such as phosphorus and nitrate can be captured and retained, which means only purified water passes through.
The recycled water can be reused on farm and, because filtration removes the water, the total volume of slurry can be reduced by up to 70%.
Membranes must be livestock specific because waste from different species varies. For instance, the constituents in slurry from dairy cows are different to those in pig slurry.
Type four: Decanting centrifugationÂ
Centrifugal force and gravity are used to separate the compounds in slurry.
Raw slurry is subjected to a large centrifugal force in a high-velocity rotating drum, typically 2,000-4,000rpm. In the course of this process, the particle components of the slurry settle toward the periphery of the drum and are subsequently removed by a rotating screw.
It is a well-tested technology, which has been used for sewage treatment both in industry and on municipal sewage disposal plants.
But, in terms of capital and operational cost, centrifuge is typically the most expensive system. Therefore, in most cases, it is not financially feasible as an investment by a single farm.
Mobile separators, featuring a decanter centrifuge mounted on a trailer, have been developed and are more commonly used in pig units in northern European countries since the introduction of nitrate controls in 2003.
What’s on the market?
1. Screen separation technology
Pollution Control’s Groundhog Model 600 and Superdry 1200
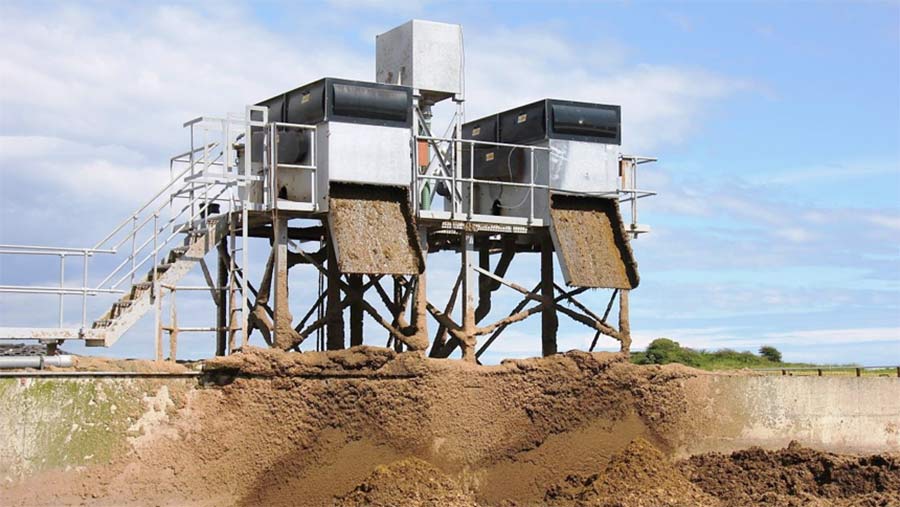
Groundhog model 1200
Throughput capacity
Depends on age, dry matter content and viscosity of the raw slurry, but the 600 model will typically process 26cu m/hour of diluted cattle slurry and the 1200 model will typically process 54cu m/hour, both at 6-8% dry matter (DM).
Is the machinery protected from incursion by small stones?
Compression rollers on flexible arms deal with small stones. The separator is also designed to deal with sand-laden slurries.
Pre-screening slats or grids at a maximum aperture width of approximately 60mm are recommended to keep out large debris.
To avoid blockages, a 100mm pump is recommended with approximate 5.5kW or 7.5kW rating.
Special features
The Groundhog Super-Dry Separator provides a double pressing action in the second stage to ensure the maximum amount of liquid is extracted.
Life expectancy
With simple routine maintenance, the company says more than 25 years is not uncommon.
Capital cost
Starts at £14,000 excluding VAT for a basic 600 model, rising to £38,000 excluding VAT for a 1200 Super-Dry complete with supply pump, mixer and support steelwork.
Running costs
From £3.85/day for a 600 model with pump and mixer running for four hours/day for a small herd of 60 cows to £27/day for a 1200 Super-Dry model with supply pump and mixer running 18 hours/day for a herd of 800 cows.
Herd size suitability
A 600 model is suitable for a 60-cow herd and a 1200 model for up to 1,000 cows.
Bedding suitability
Suitable for all bedding types, including sand and sawdust.
Contact details
Pollution Control 01772 620 066Â www.pollution-control.co.uk
2. Press separation
Roller press
The Evolution stainless steel roller press separator from CE Projects, Market Drayton
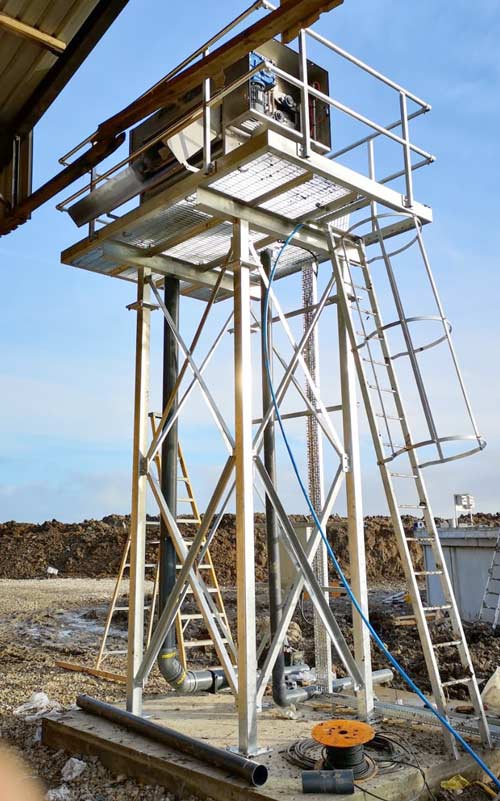
Evolution stainless steel roller press separator
Overview
This separator has two outer and two inner rollers and presses the slurry through a stainless-steel perforated screen.
Considerations
For pig slurry the machine runs very fast, but it is slower for very thick cattle slurry.
It is constructed entirely of stainless steel.
The company supplies complete systems, including pumps, gantries and control panels.
Life expectancy
25 years or more.
Storage
On average, it is possible to gain up to 30% on storage requirements by removing the fibre.
Herd size suitability
Three models are available, the smallest is suitable for a herd of 60 cows and the largest for a herd of 500 or more.
Special features
Has a removable stone trap and a monitor can be fitted to sense if anything large enters the machine and the system then turns off.
Running cost
It runs on a 1.5kW motor and costs about £0.20/hour. For 200 dairy cows the machine would run for approximately 2.5 hours/day depending on the viscosity of the slurry.
Bedding suitability
Compatible with sand bedding.
Capital cost
The basic 600 machine starts at £10,000, the 1000 machine from £13,000 and the 2000 starts from £18,800. All prices exclude VAT and carriage.
Contact details
CE Projects 07960 986622 /07850 363131 www.ceprojectsltd.co.uk
Screw press
EYS SP600 screw press separator from Midland Slurry Systems
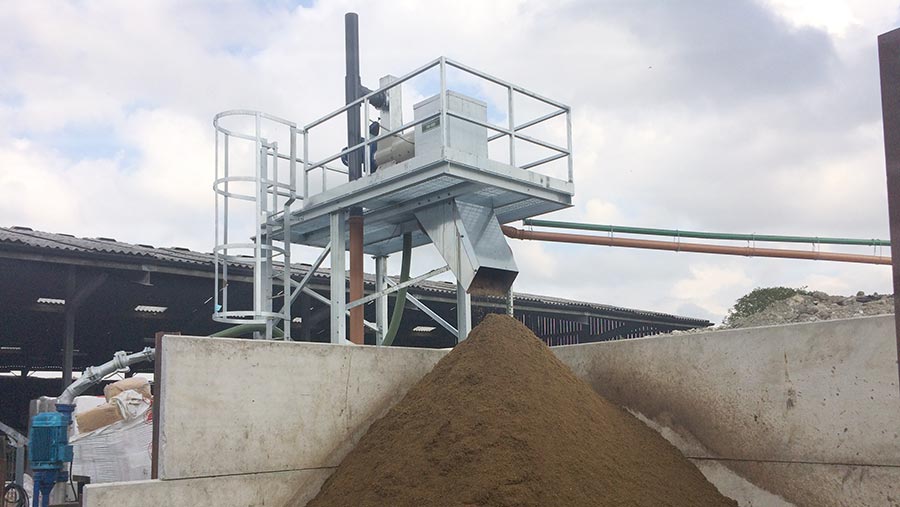
EYS SP600 screw press separator
Overview
Separates solids and liquids via a tungsten hardened auger screw and a stainless-steel screen.
Comes as standard with a 0.65mm screen designed to produce dry matter of 25-35%.Â
Throughput capacity
25-45cu m/hour, depending on the viscosity of the slurry.Â
Storage
Will typically reduce storage requirements by about 25%.
Considerations
The machine is designed to be fed well-mixed slurry via a pump fitted in a suitably sized reception tank.
Various screen sizes are available to suit different applications.Â
Life expectancy
The company claims the screen and auger will provide many years of trouble-free service, providing any abrasive material is kept out of the system.
Herd size suitability
SP600 can handle slurry from herd sizes of up to 1,000 cows.
Other EYS models are available including the SP400 with a 2.2kW motor which handles 10-15cu m/hour for a maximum herd size of 150 cows.
The bigger SP800 model runs on an 11kW motor, handling 40-60cu m/hour for a max herd size of 1,500 cows.
Capital cost
The SP600 model costs £20,835.00 excluding VAT for the machine only, but when added to a complete system to include a mixer, pump, gantry, control panel, pipework, delivery and installation, but excluding tank and electrical work, the total cost is in the region of £55,000 excluding VAT.
Running cost
Comes with a 5.5kW three-phase motor that costs about £0.55/hour for the electricity.
Bedding suitability
Best suited to chopped straw, sawdust, shavings and other soft bedding.
Sand or abrasive bedding are not recommended.
Contact details
Midland Slurry Systems 01608 664219 www.midlandslurrysystems.co.uk
3. Decanting centrifugation
GEA Decanter
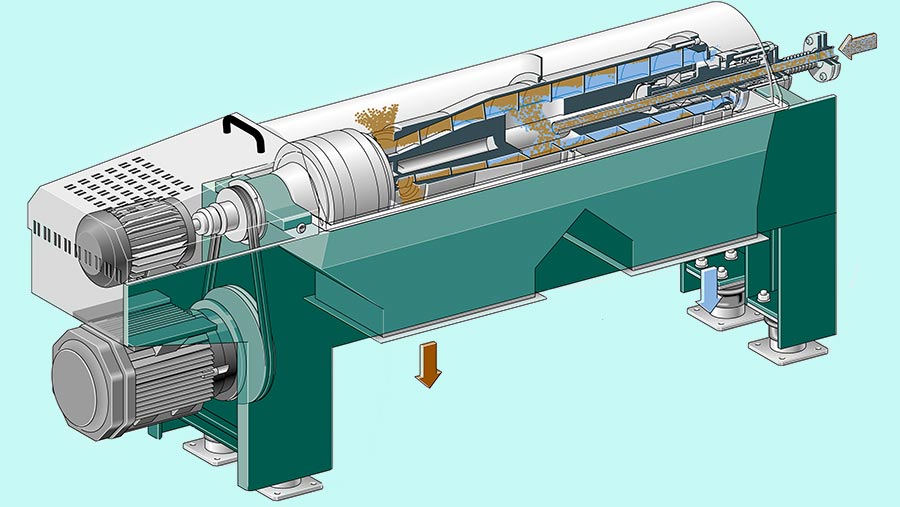
GEA Decanter
Overview
A continuously operating centrifuge developed specifically to dewater liquid manures and digestate.
Considerations
A high capture of solids means there is little or no settlement in storage lagoons and tanks so regular agitation and digging out is not needed.
Solids can be used as green bedding under the right conditions and in compliance with legislation.
A service interval of 10,000 hours is recommended.
Slurry throughput capacity Â
Processes up to 80cu m of slurry an hour.
Storage
Extracts more than 85% of the liquid fraction.
Life expectancy
20 years.
How does it deal with small stones?
Small stones are usually screened out, but surfaces are protected against incursion with tungsten carbide hard facing. 

Herd size suitability
Suitable for a herd of 150 cows or more.
Capital cost
This depends on the machine configuration, but approximately £65,000 inclusive of VAT. Lease options are also available from GEA.
Bedding suitability
Any bedding can be handled, but when sand is used the replaceable tungsten carbide discharge ports should be checked regularly.
Running costs
The decanter uses up to 0.9 kWh/cu m. Running costs are dependent on energy prices.
Contact details
GEA 01908 576525 www.gea.com