What’s in Your Livestock Shed visits a £1.4m greenfield dairy
No corners have been cut in the design and building of the new parlour and cubicle shed 230m away from the original dairy at Beckside Farm, near Millom.
Robert and Rowena Morris-Eyton and their son, Patrick, built the facilities to future-proof the enterprise for the next generation and allow them to expand herd numbers from 250 to 400 this year.
You can also read the Morris-Eyton’s planning tips in 7 farmer tips to fast track planning permission.
Farm facts
- Milks 350 cows three times a day at 5am, 1pm and 9pm
- Four staff employed between 5am-3.30pm and dedicated night milkers
- Total milking time for 350 cows on three times a day is less than the 210 cows twice a day in the 12:24 herringbone parlour
- Supplies a dedicated Arla Morrisons contract
- 5m litre target output
- One rotation takes 12 minutes and milks 54 cows
What were the reasons for investing in a new parlour and shed?
The old 12:24 herringbone parlour was 25 years old and broke down once a day, while the 1960s-built cubicle sheds had narrow passages and poor ventilation.
With Patrick coming back to the farm, the family wanted to expand, but couldn’t on the original site. The new parlour, however, has the capacity to milk 2,000 cows.
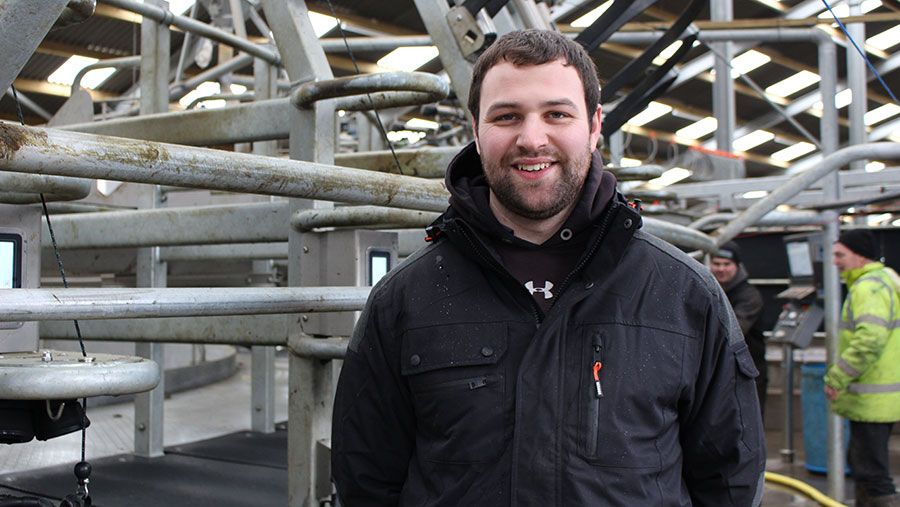
Patrick Morris-Eyton © Sarah Alderton
Tell us about the parlour
The 72x25m parlour houses a 54-bale variable-speed Waikato rotary, collecting yard, handling facility, hospital pen and an educational room with a viewing gallery onto the parlour.
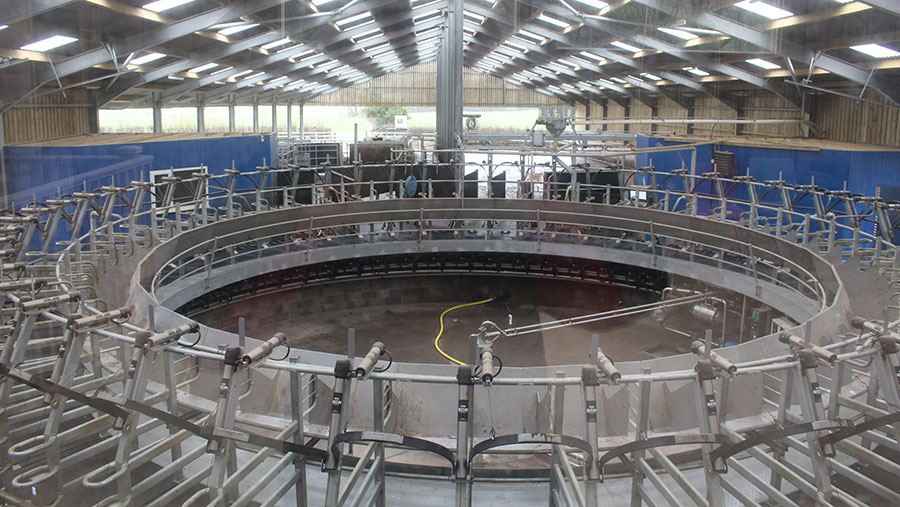
© Sarah Alderton/MAA
It is a UK first and one of only 10 worldwide. It has a 17deg pitched roof and cranked ridge.
Roller doors, like those in a fire station, are situated on either side of the parlour, adding light and ventilation to create a more pleasant workplace.
The 11x44m collecting yard has an automatic backing gate and a printed concrete floor (cobbling effect) that provides grip.
The sides are Yorkshire-boarded, while the Waikato Centrus rotary platform is made from fibreglass.
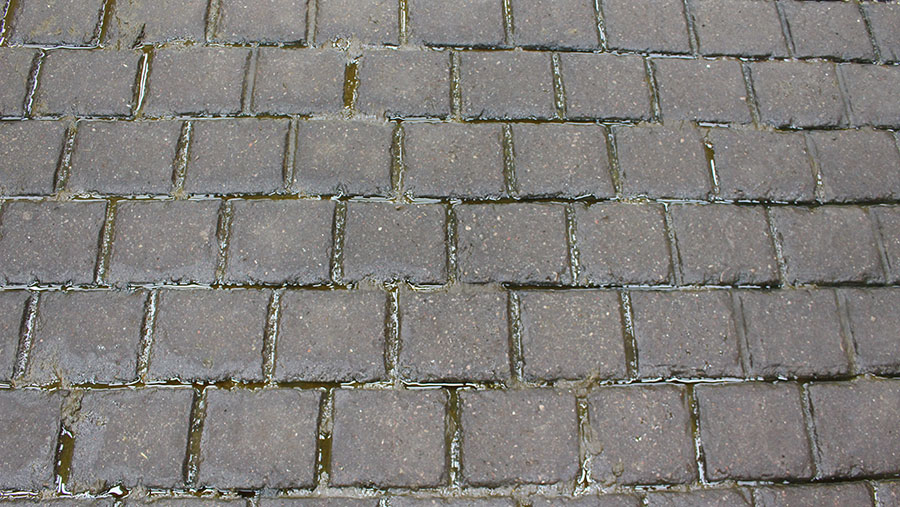
© Sarah Alderton/MAA
At 15% of the weight of concrete, this reduces wear on running gear, while being less prone to chemical damage.
There are automatic deck sprayers, cluster removal, teat sprayers and electronic milk meters.
Auto-ID entry means cows can be fed to yield from two feed towers. In the parlour, LED lights provide 500 lux via a timer.
Tell us about the cubicle shed
The 120x25m shed contains 336 cubicles with feed space on the outside.
Two 5m-wide outside passages and a central 4.5m passage contain two rows of head-to-head cubicles, which sit between three main passageways and three cross-passageways.
A 25m gap between the parlour and cubicle sheds improve ventilation.
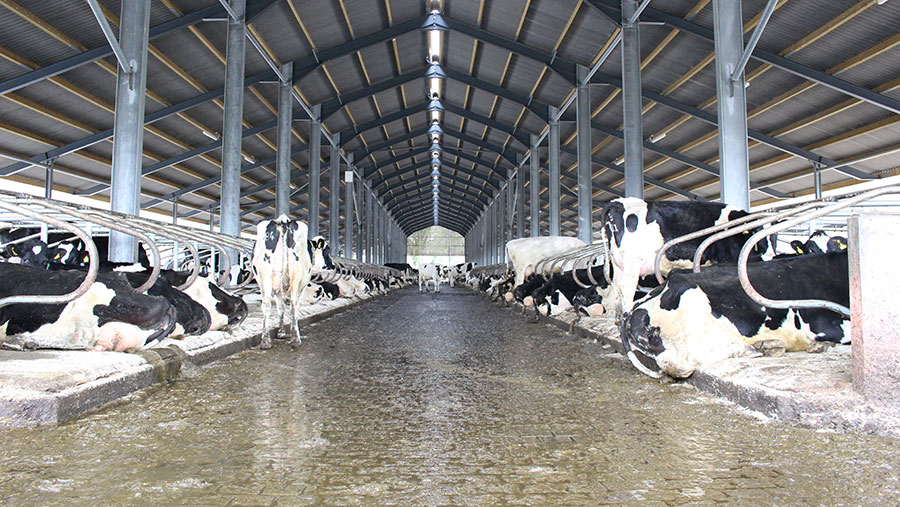
© Sarah Alderton/Maa
The cubicles are Wilson C50s with a 40mm foam mat, topped with a thin layer of sawdust (applied twice daily) and disinfectant powder (applied once a day).
Twice a day, a Bobman is used to brush sawdust off the bed to keep it fresh.
“Pillows” situated in each cubicle help improve cow placement so few defaecate on the bed.
For longevity, the feed fence is concrete panelled and the 1m-wide outside feed space has a polished, concrete surface that is raised 120mm to aid feed intakes.
There is a 2.5m overhang covering the feed area, and a 2deg floor gradient cuts out any pooling of liquid to improve foot health.
The open-sided cubicle shed has a central, open ridge roof and measures 4m to the eaves to aid air flow.
The shed has eight rotating cow brushes and bottom-drop water troughs.
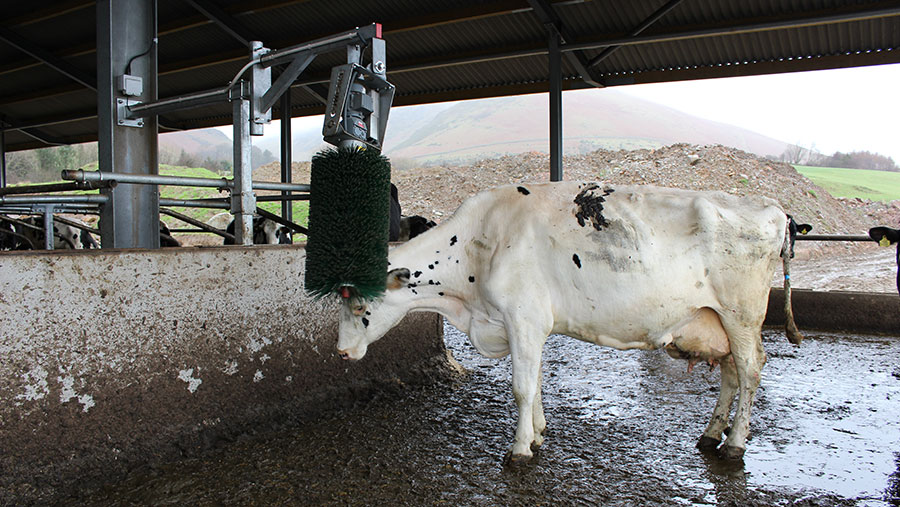
© Sarah Alderton/MAA
Sensor-controlled LED lighting provides 200 lux a cow at head level for 16 hours a day. Roof lights were not used, to keep down summer temperatures.
Cameras in the cubicle shed and parlour, as part of the Arla 360 programme, allow us to demonstrate our good practice.
How has the parlour eased the workload?
Cows enter the parlour through double races that improve cow flow and mean there is rarely an empty bail. This, along with automation, has speeded up milking.
One person can milk 200 cows/hour comfortably, while two can handle 350 cows an hour.
Why didn’t you opt for automatic scrapers?
Scraping is done using a telehandler-mounted, 5m-wide Storth scraper rather than automatic scrapers. This prevents cows catching their hocks and eliminates potential breakdowns.
We calculated that using a 5m-wide scraper, instead of a 4.5m-wide scraper, reduces workloads by 18 minutes/day, or 109 hours/year.
Have you reduced bedding?
Cows used to be bedded up twice a week with a thick layer of sawdust. Now we use only a fine layer twice a day, which has halved sawdust use, despite having 100 more cows.
What elements of the parlour and cubicle help improve cow health?
Undoubtedly, the automatic Hoof Count foot-bath on the exit race helped reduce lameness. It contains a 1% formalin solution that automatically refills after a certain number of cows.
Digital dermatitis has dropped by about 75%, with less than 2% of the herd affected.
The printed concrete flooring also aids foot health.The better cubicle accommodation and less waiting time in the cubicle yard have increased yields by 1,000 litres a cow a year.
Milking three times a day added a further 1,000 litres a cow, taking production from 10,000 litres to 12,000 litres.
Mastitis has also reduced. A low-lying mastitis issue meant we were pre-stripping every cow.
However, the parlour has a full D-tect system. After the operator has wiped the teats and put the cups on, there is a 60sec delay before pulsation starts.
In that time, a small milk sample is automatically tested using a milk conductivity meter. High cell count cows will be flagged or the cups will be automatically removed.
This helps us pick up mastitis cases earlier and eliminates pre-stripping every cow, reducing the workload.
How did the cows take to the new parlour?
We bought 80 milkers plus youngstock from the pedigree Ballyginniff Holstein herd and put 70 through first.
They settled quickly and by the third milking, were going in voluntarily. We then introduced the rest.
Who designed and constructed the building?
The buildings were designed by Cowplan’s Ivor Davies and built by Ian Pickthall using steel supplied by Simon Schofield.
What was your initial budget, and did you stick to it?
We spent £1.4m on everything, including the parlour at £750,000 and £500,000 on the cubicles. It is a lot, but we have future-proofed our business without scrimping on anything.
We went over by £250,000, as we purchased a herd of cows and added an Xchanger milk cooling system.
This recovers energy from milk cooling to heat water for parlour washing and underfloor heating in the office and staff changing facilities.
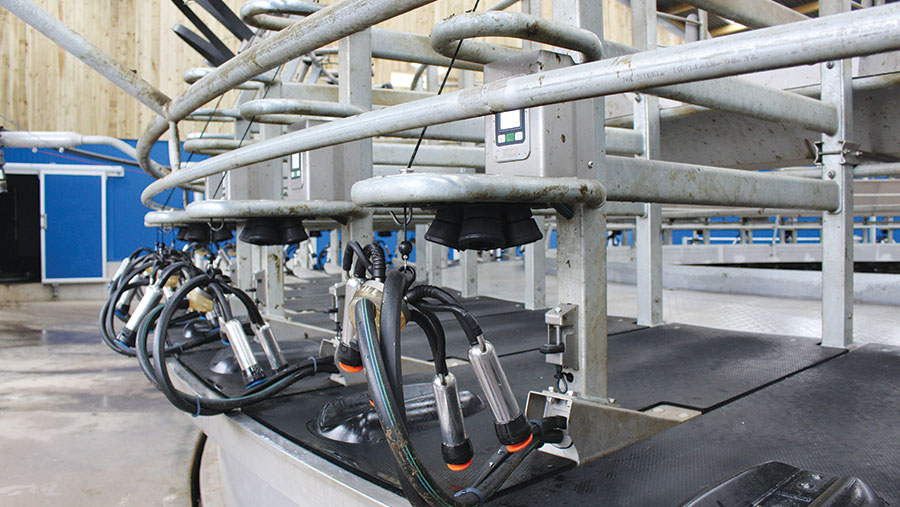
© Sarah Alderton/MAA
How is the new site saving energy?
The Xchanger milk cooling system provides a massive energy saving and 90% of the energy used is produced from hydroelectricity.
We have also built a 27.3m-litre clay-lined slurry lagoon, which is gravity fed, so there is no need for pumps. All the volume wash water is also gravity fed.