Belt planters becoming more attractive for potato growers
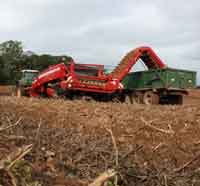
Belt-fed potato planters have been around for years and have a loyal following. But interest is once more growing, thanks to the extra output such machines can offer time-stretched growers. Nick Fone reports
Potato growers have two basic options for getting their seed stock in the ground – cup or belt planters.
As the name would suggest, the former use cups to lift tubers from the planter hopper and deposit them in the row. Conversely, belt planters employ a giant rubber band to distribute seed from the hopper.
While cup planters can pretty much guarantee placing the potatoes at an accurate distance apart, belt-fed machines aren’t so limited on speed and, in the right conditions, can work at over double the pace.
“Cup planters have always been felt to offer better accuracy than belt machines,” says Russell Blight from Miedema Mercer Machinery, the company that sells Structural belt planters in the UK.
“But because our planters are gentler, they’ve traditionally had a loyal fan base with those growers using chitted seed.
“More recently though, it’s farmers looking to speed up their planting operations that are coming to us.”
And that trend is reflected with the market leader, Grimme. In 2007, the German company introduced belt planters to its range that had previously only included cup machines.
“Three years ago 100% of our sales were cup planters because that’s all we had to offer,” explains the firm’s Ralph Powell.
“But since we’ve introduced the belt-fed machines, they now take up a third of our planter sales.”
Much of this is down to belt machines’ abilities to handle irregularly shaped and sized tubers, making seed that is much cheaper to buy, he reports.
Although important, Mr Blight would argue that tuber spacing is not as critical as it was once felt to be.
“We find that the Structural machines tend to drop bigger tubers at wider intervals and smaller ones closer together which, when you think about it logically, makes sense.
“What matters is tuber count per hectare and belt-fed machines are just as accurate on that front.”
And for those growers where fields are spread over an area, road transport is often an issue. Where a two-row belt planter can match the daily workrates of a four-row cup machine, it’s inevitably the former that is chosen because it is so much easier to handle on the road.
Where Dutch-built Structural planters can come in for criticism is when working on banked ground. Because it is gravity that ultimately decides tuber flow rate onto the belt, when running downhill the hopper outlet can become flooded and, when working uphill, it can be starved.
The company has tackled this problem with the addition of a hydraulically adjusted bed, its angle controlled by a fluid switch that senses slopes and corrects the machine accordingly. Currently in prototype form, Hilmaster planters are hoped to be on sale next spring.
CASE STUDY – Harry Chase, Rosemaund Farm, Herefordshire
Farming the land at ex-ADAS research farm, Rosemaund, close to Hereford, Harry Chase’s family have long been fans of belt-fed planters.
200 acres of Maris Piper are grown, 1000t of that going to the farm’s new vodka distillery venture. The remainder is destined for the pre-pack and chipping markets, all sold on a free-buy basis.
“We’ve tried most options to try to get spuds in the ground as quickly as possible in that ever-tightening spring planting window,” says Mr Chase.
“We’d always preferred belt planters because of their speed, but one year we were tempted by the price of cup planters and so tried a Grimme 32-B. It just couldn’t keep up so we went back to a Structural.”
Planters are generally run at between 7-8kph on the farm’s red soils and, according to Mr Chase, are only limited by how fast nematicide applicators can work and by the final bed finish.
This significantly cuts labour requirements and with one man on the planter and another keeping him topped up, the two-man team can plant 25 acres a day.
With tuber spacing so critical to the final size, shape and quality of the lifted crop, Mr Chase feels he has good control over this with a belt-fed machine.
“In the pre-pack market it’s very important to get a uniform product and the best way to achieve this is accurate tuber placement.
“With big tubers we tend to find the spacing lengthens and with smaller ones they’re closer together. But it seems to even out over the growing season – the key is having evenly sized seed in the first place.”
When the Chases’ potato area grew to around 700acres a number of years ago, the decision was taken to step up from a 1.3t mounted machine to a big trailed planter with a 3t hopper. Having sold their crisp business, the planted area is now somewhat smaller and consequently a smaller machine will be sourced for next spring.
“We always aim to add value to our products and avoid the commodity markets. Whether it’s crisps, apple juice, beef or vodka, we’re always looking to produce top-end stuff.
“And that extends right down to the humble potato – it has to be grown in the right way and that starts at planting.”