Big choice of headers if going down wholecrop route
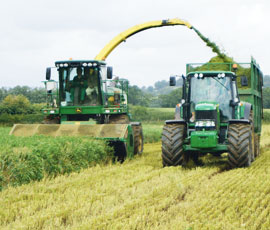
Harvesting wheat crops whole and green provides a valuable source of winter feed for dairy cattle – and added business for forage contractors. Peter Hill details the specialist equipment they use.
Cut, chop, blow and clamp. As with any forage-harvesting operation, speed (without neglecting attention to detail) is of the essence.
Among its top tips for wholecrop wheat or arable silage, Genus emphasises the need to cut the crop at the optimum timing or risk losing dry matter at a rate of up to 2% a day.
Its advisers recommend cutting a fermented cereal whole crop when the grain is at the soft/cheesy stage (GS 77-85) with about 30-40% dry matter and stems still largely green – or at least 50:50 green and yellow.
They also advise cutting relatively high – about 10cm (4in) is ideal – so that any rubbish is left behind, not gathered up to contaminate the contents of a well-consolidated clamp.
Contractors running costly self-propelled forage harvesters wanting to include this extra harvesting job in their work schedule need to operate at a good pace, not only to meet those dry matter targets, but also to service sufficient customers and hectares to make the service pay.
Arable silage provides a welcome additional workload for contractors, especially as it fares well in areas marginal for forage maize production. But while helping spread the cost of a high-performance forage chopper, harvesting this fodder also requires further investment of between £30,000 and £50,000 in the front-end equipment needed to get the crop to the chopper.
While combine cutting tables of modest width can be adapted to fit a forage harvester ready to carve its way through wheat, purpose-built disc cutters are more effective at cleanly slicing through the green stems.
QuickcutGB
Having imported the concept from New Zealand, Paddy Norman has been making QuickcutGB forage harvester disc mowers since 2003.
With the unveiling of a 6.4m version a couple of years ago, he extended the sizes available to three to cater for different forage harvester sizes and contractors’ output expectations.
The QuickcutGB 400 and 580 – 4m and 5.8m, respectively – remain popular, though, since the smallest of the trio is good for 600 to 800 acres in a busy season. Typical operating speeds are reportedly 9-14km/hr
Apart from the ease of replacing damaged disc units, using the modular Lely cutterbar enables a bespoke arrangement of disc rotation.
On the 6.4m machine, for example, the outer three discs rotate in the same direction towards the centre of the bed to help get the crop flowing from the outer extremities.
The next two discs turn in the opposite direction to kick the grass into the grasp of the centre-delivery auger. The remaining discs contra-rotate in pairs to keep the crop flowing to the back of the bed, which for this model is constructed from stainless steel to minimise friction and keep the crop flowing as fast and as smoothly as possible.
With heavy-duty Walterscheid shafts and gearboxes, the QuickcutGB mower is reckoned to happily cope with the demands of a contractor’s workload. There are mountings to fit Claas, John Deere and New Holland forage choppers.
Zurn
Specialist combine table manufacturer Zürn turned to Kuhn for the disc cutterbar used in its Profi Cut wholecrop mower, which is said to have a typical working speed of around 15km/hr.
There are two sizes – 4.6m and 6.2m – with an auto-levelling headstock built into the larger model to help follow contours accurately at the required cutting height.
Self-regulating multi-band belt drive to the auger is situated on the left-hand side of the machine.
Here, it is also coupled to a shaft that transfers drive to the centre of the cutting bed where drive goes through a pair of 90˚ gearboxes into the adjoining discs of the two separate cutterbars.
John Deere highlights the Zürn disc cutters as its approved option for the current range of self-propelled forage harvesters.
Krone
Krone builds its own wholecrop mower for the BiG X forage harvester. The XDisc is 6.2m wide and uses a fully welded one-piece disc cutting bed with a wavy-shaped leading edge designed to help crop flow.
The blades can rotate through 360˚ to avoid excessive damage against stones and other field debris and the blade holders can be individually changed if necessary without having to replace the entire assembly.
An over-run clutch provides further protection, while the 90cm diameter centre delivery auger is protected by a star ratchet. The auger itself can be fitted with serrated sections between the flights to provide a more positive sweeping action.
A single shaft connects the drive to the auger and the 14-disc end-driven cutterbar.
Claas
Drive to both ends of separate cuttersbars from a central gearbox is one of the features of the Claas Direct Disc mowing deck for the Jaguar range of self-propelled foragers.
There are two sizes – the Direct Disc 610 at 6m wide and the 520 at 5.1m – both featuring twin Disco disc cutterbars from the familiar mower range, with a secure but quick-release knife installation that minimises repair and maintenance downtime.
On the Direct Disc units, a paddle roller helps transfer crop to the auger that sweeps the material to the centre of the deck and into the harvester’s feed intake system.
New Holland
New Holland has expanded the direct cut options for its FR forage harvesters by introducing the ‘Marangon for New Holland’ disc-cutting attachment.
The harvesters can already be equipped with a Varifeed combine tables to cut wholecrop, and the New Holland 570FW Discbine attachment provides a 5.5m disc mowing alternative.
This unit uses oval discs with large blade overlap to encourage rapid crop flow, hydraulic angle adjustment helps get the right cutting attitude and the ShockPRO system individually protects each of the discs and prevents damage to the drive gears.
But the 14-disc unit from Marangon delivers extra capacity from its 6m working width and the ‘super flat’ round discs that are designed to provide uninterrupted crop flow on to the bed.
There is indirect drive to each disc gear for reduced parasitic power losses and driveline maintenance can be performed without having to open the cutterbar, which is welded into the mainframe to form a strong unitary structure.