Deere shares i-Farming vision
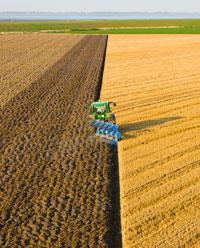
Has the bigger-is-better approach had its day? Emily Padfield went to John Deere’s new technology centre in Germany to see what the US giant is concentrating its efforts on.
Farm machinery may have been getting wider and more powerful for decades but at Deere’s new European Technology and Innovation Centre (ETIC) in Kaiserslautern, Germany, the emphasis is beginning to change. The future could be as much about increased technology and innovation as sheer size, according to the general manager of Deere’s Agricultural Management Solutions (AMS) arm, Dr Thomas Engel.
John Deere says it invests close to $1bn each year into research and development. The new technology centre will employ close to 200 people, most of them engineers, computer experts and technicians working on software and electronics to make farming applications as automated and efficient as possible.
Deere believes that the future evolution of farm machinery will involve much more than simply stuffing a bigger engine in. Instead, machines will become increasingly automated and even self-operating.
* Tractor-implement automation
Seen at Scotgrass earlier this year, this new development allows two-way data transfer between the tractor and implement – in this case between a 7530 tractor and 864 round baler through an extended Isobus system. The baler tells the tractor when the bale is near completion, then automatically slows and stops the tractor while starting the net wrapping process and unloading the bale. It then tells the tractor to start off again.
This is all done by the operator putting their foot on the brake, or knocking the tractor into neutral and then taking their foot off or selecting drive. This could be automated further, says Deere, though health and safety dictates that this final step has to be done by an operator.
The technology has already been configured to work with a Pottinger forage wagon, too, with hydraulics, pto and forward speed all determined by the density or shape of the grass swath in front of the machine.
* More automation for sprayers
Sprayer operation is set to get more straightforward with a tank fill calculator, automatic boom and section control and auto dilute.
Operators enter the application rate and the area that needs to be sprayed and the calculator works out the amount of chemical and water needed for each individual fill or partial refill. A printer in the cab gives the driver a handy ticket with the required quantity of chemical and water for each bout.
The Sprayer Pro system provides standard section control and shut-off at the headlands, while the Auto Dilute feature controls the level of dilution of residual liquid left in the sprayer after application, and (depending on the next application) selects the quickest and most efficient method of cleaning.
* More steering options
Aimed primarily at veg crop growers, there are now two levels of implement guidance on offer that work alongside Deere’s standard steering systems. Passive implement steering is provide through iGuide, which automatically keeps implements on track by two StarFire RTK receivers: One mounted on the tractor and one on the implement, which enable the tractor to compensate for implement drift on slopes or when going round headlands.
Active implement steering, called iSteer, is suitable for three-point linkage mounted equipment like mechanical weeders and, as seen at Cereals, ploughs. Deere has worked with Dutch company SBG to develop a receiver that is mounted on the implement. In the case of a plough, an electronic valve block controls the vari-width function, maintaining arrow-straight furrows, even on hills.
* Emissions
Deere also outlined the route it will take to meet the next round of emissions legislation, due to come into play on 1 January 2011. The regulations require a reduction in particulate matter by 90% and in nitrous oxide by 50% in tractors over 174hp.
To meet the Stage IIIb regs, Deere is sticking with exhaust gas recirculation (EGR) instead of going down the selective catalytic reduction (SCR) route, adopting the same technology featured in its new 8R Series tractors.
This includes a variable geometry turbocharger as well as an exhaust filter component that includes a diesel oxidation catalyst and particulate filter to meet the particulate matter targets.