Out of the farm workshop – Round bale accumulator
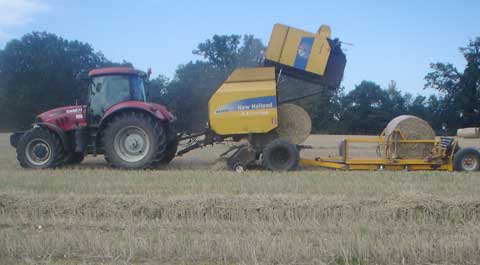
When you’re running an outdoor pig enterprise which covers 100 acres of land, has 720 sows and 7,500 offspring, there’s a need for an awful amount of straw each year – 9,000 bales of it.
For Paul Hayward and his brother Mark, who run the Dingley Dell Pork enterprise at Campsea Ashe, Woodbridge, Suffolk, the annual straw baling and carting operation is a key part of their business.
“We farm a total of about 500 acres,” explains Paul. “This gives us about 350 acres of land for cereals – wheat barley and oilseed rape – and we rate the value of the straw these crops produce as highly as the grain.”
With such a high volume of bales required, the Haywards purchase straw from a number of neighbouring farms and aim to clear fields quickly to allow cultivations to begin.
“Speed is everything,” he says. “If we are to expect to be offered straw in following years we have to make sure we make a good job of clearing fields as soon as we can.”
Until a couple of seasons ago, the system used was to employ a Traileyre bale carrier with its lift arms and spikes – one which had been converted to pick up two bales at a time to create a second layer of bales and double the number which could be carried to 20.
“We had to fit twin axles and beef things up a bit, but it worked fine,” says Paul. “The problem was that with the bales deposited in line with the baler, the Traileyre always had to work across the tramlines to pick up the bales and that was hard, slow work when they were deep and rutted.”
Paul set about building a bale accumulator which could not only drop two bales off in readiness for collection but also rotate them through 90 degrees so the Traileyre could travel more quickly along the tramlines.
With the bales positioned correctly, output improved dramatically, with rates of 100 bales/hour being cleared with a field to store distance of one mile. Previously a rate of 40 bales/hour was usually achieved.
The original intention was to build a sledge which could place two bales together, says Paul.
Hooked onto the back of a New Holland round baler which produces 1.4m diameter bales, this was not too difficult to achieve – the bales rolled out and, when there was a pair, the floor tilted rearwards and the bales were deposited on the ground.
But recognising that things could be so much better if the bales could be rotated through 90 degrees before they left the sledge set Paul thinking.
Key to it was a bed which was supported on a turntable and, through the use of a hydraulic ram, could be swung round 90 degrees and then be tilted to release the bales.
After a lot of planning, building and adjusting, the final version rolled out of the workshop in time for the 2010 harvest.
To understand how it all works it’s best to follow the sequence of operations which results in two bales being deposited side by side on the ground, each at 90 degrees to the direction they left the bale chamber.
With the accumulator hitched to the rear of the baler by a ball coupling, the first bale ejected lands on two spring-loaded pads, which encourage it to roll to the back of the accumulator. If it doesn’t and remains in the front section the operator has a “jolt” control which will persuade the bale to roll to its correct position at the back, resting against the tail gate.
“The bale normally behaves itself, but if baling down hill it can require an extra nudge to move it,” explains Paul.
With the second bale on board, the unloading sequence starts with the rotation of the accumulator bed through 90 degrees – it is actually nearer 80 degrees due to the unavailability of a ram having the right length, but it works really well, insists Paul.
At this point the tailgate opens, the bed is tilted and the bales roll out. While this is all happening the operator will have closed the baler’s door and can start making the next bale as the accumulator’s bed is returned to the horizontal, the tailgate is raised and all is rotated back into position to accept the first of the next two bales.
Hydraulic power is provided by the tractor and the sequencing of operations is controlled by a PLC unit in the control box, which receives its information from a series of proximity switches.
As ever with farm-built machines, parts and components can be something of a compromise by using parts available on the farm and making other bits to fit round them.
With more demanding work often requiring his attention outside the workshop, work on the accumulator was spread over several months.
“I started with the axle, which was actually the one we took off the Traileyre when we refitted it with tandem axles,” says Paul.
The steel for the chassis was purchased new, but most of the hydraulic rams were already on the farm – the residue of long-forgotten implements.
“Once I had the chassis it was a matter of creating the main bed and, with a significant amount of trial and error, assembling the rest so it all worked,” he says. “I had built a prototype in 2009 which just gathered two bales without rotating to ensure I had the measurements and strengths about right.”
In terms of cost, the steel cost £606, the hydraulic control £463, hydraulic pipes and valves £1,186, and the six proximity switches were £18 each. There was also a cost of employing a hydraulic specialist to assemble the system so the required sequencing worked correctly.
As with all new machines there were a series of teething problems to overcome – adjustments to be made and so on, but Paul reports that after a couple of days he had the machine working well.
“I had to alter the angle of the ramp to get the bales to drop out – oat straw proved to be particularly reluctant to roll,” he says. “And there were a few other height adjustments and sequencing changes, but nothing too difficult to fix, although it was a bit of a tease at times.”
Having built this one and having put about 14,000 bales through it, what changes would he make if he was to build another one?
“There are one or two changes I would make, the main one would be to be able to rotate the bed both to the left and right, so that the slope of the field could always be used and ensure the bales roll clear,” he explains.
He adds that he would also reduce the width of the axle so there is no risk of the wheel catching the side of the bale if it hasn’t rolled far enough away from the accumulator.
“I would also strengthen the drawbar – I had to re-weld the one being used at the moment but again, these are not major design changes,” he insists. “The important point is that the system works and we are able to clear bales from fields at a rate that was previously impossible to achieve.”