Made in Britain: Meet two UK ag engineering firms on the rise
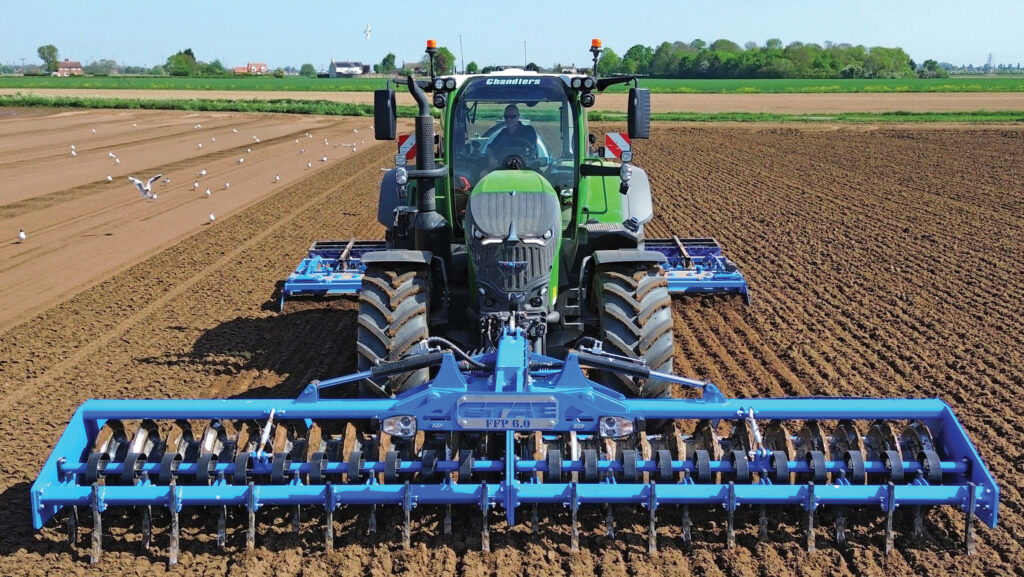
Behind many big-name machinery brands is the story of a fledgling engineering firm starting out from scratch. We meet two entrepreneurs with outfits on their way up.
See also: High-end bespoke builds put Grizzly Trailers on the map
George Merrison
GT Agricultural Engineering, Holbeach, Lincolnshire
Having cut his engineering teeth working in farm workshops and professional kart racing teams, George Merrison took the decision to branch out on his own.
Armed with a £2,500 loan from his dad in 2017, he rented a nearby workshop, kitted himself out with tools and began making and modifying agricultural machinery, with a side helping of mobile repairs and servicing.
By the end of his first year, the business had grown large enough to employ one person, two more came in the second year, and he now has seven on the books – three welders, a machinist, a painter, one admin and his dad, who works almost exclusively on design.
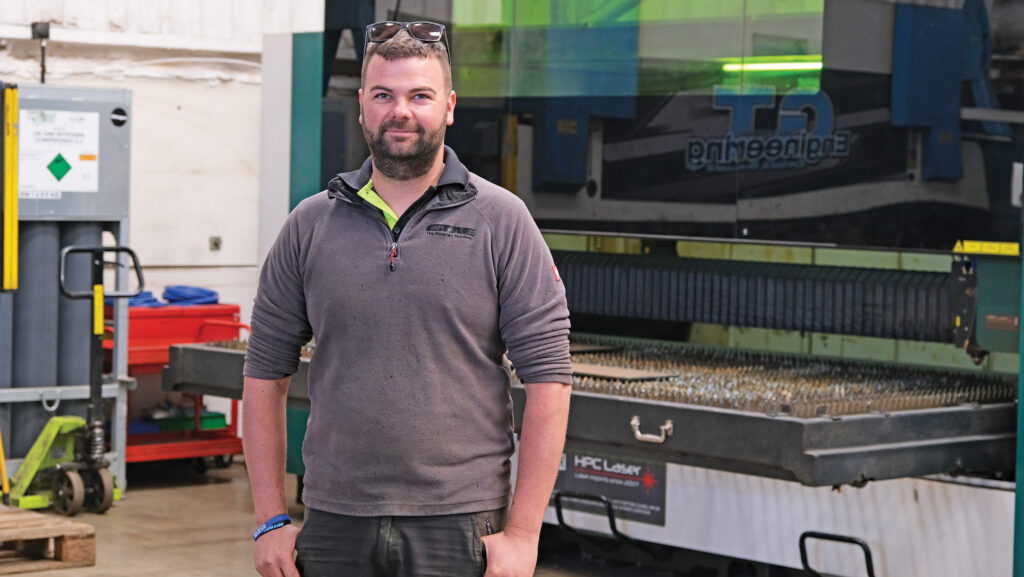
George Merrison © James Andrews
The servicing side grew particularly quickly, to such an extent that it began to detract from his core interest of design and fabrication.
So, in 2022, George changed tack and got back to doing what he liked best.
Today, the business is split roughly 50/50 between repairs and fabrication of new machinery, with the former carried out either in the workshop or on-site using vans kitted out with generator welders.
Despite the swell in staff numbers, George spends as much time as possible on the workshop floor.
“I do some of the CAD design work, but I’m not really a fan of paperwork and would much rather be doing some welding or machining,” he says.
As for fabrication work, this covers everything from weight block toolboxes and side lockers to front presses, tine cultivators and subsoilers.
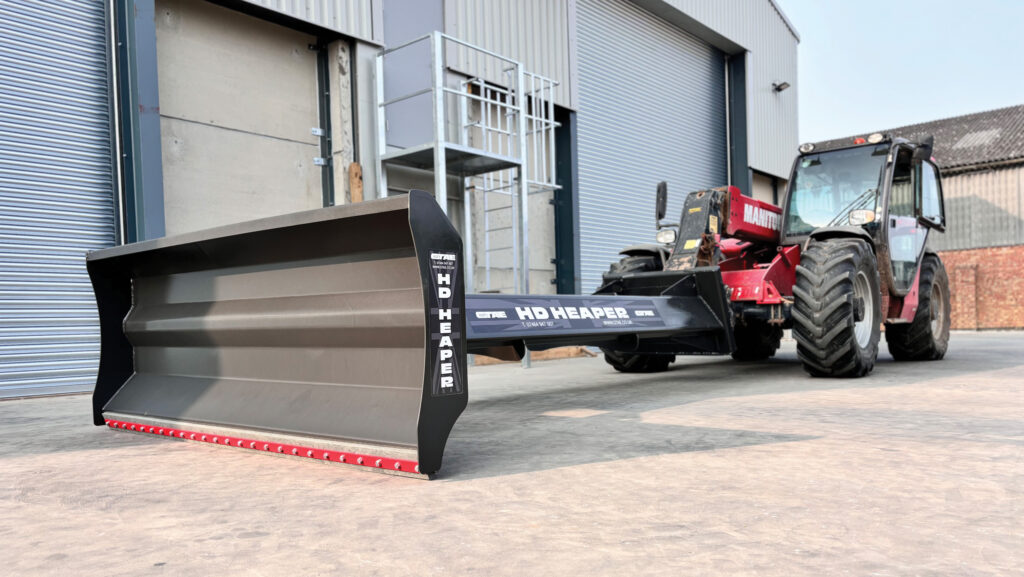
GT Engineering offers a range of grain pushers © James Andrews
Plus, he and his team carry out contract manufacturing for a couple of well-known names, such as Grimme and Perkins, as well as some non-agricultural customers.
He still has a hand in motorsport, with a sideline business making jig tables for setting up racing karts.
Bespoke builds and modifications are another area of expertise, with farmers coming to him with a plan of what they want to achieve so that he can turn it into reality – from trailer and cultivator alterations to custom-built machines, gates, bridges or buildings.
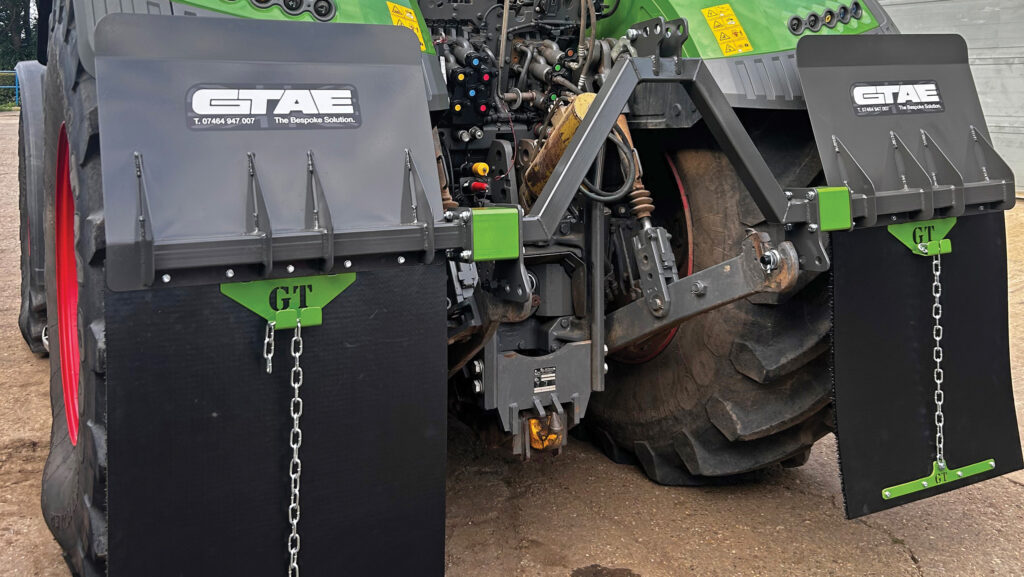
Linkage-mounted mudguards help protect trailed implements © James Andrews
To help carry out all this work as efficiently as possible, the workshop is filled with some £400,000 worth of equipment.
One of the biggest single contributors to this tally is a 6kW HPC laser cutting table, which arrived in last year and has allowed most profile cutting to be brought in house.
In addition to saving a tidy sum on each job, it means projects can be turned around much faster with parts able to be cut out as soon as they’ve been designed.
There are also high-tech CNC milling machines and lathes, a guillotine, press brake and a proper spray booth for applying 2K paint finishes.
“You’ve got to have the right equipment to be efficient, so I’ve kept reinvesting,” says George.
Tractor accessories
Though most equipment is built to order, some popular items, such as his range of storage boxes, are kept in stock.
These include options that mount below the right side of the cab on the chassis of crawlers, and on front linkages.
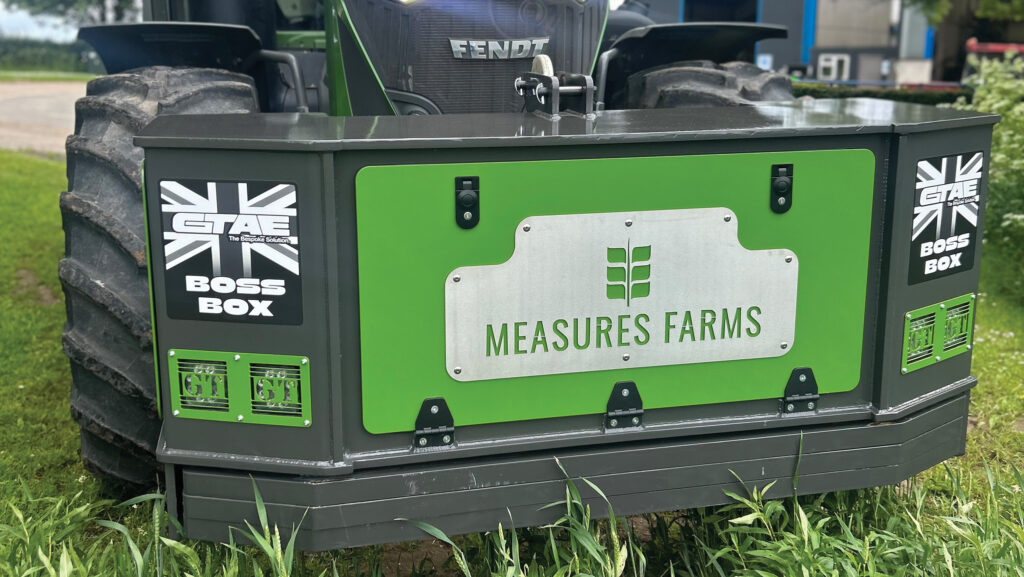
Boss Box weighs 1t empty and can be ballasted to 3.5t © James Andrews
The latter come in an array of sizes and can be fitted with neat wafer weights to create the desired amount of ballast.
Topping out this range is the Boss Box, which weighs 1t empty and can be cranked up to 3.5t if required.
Cleverly, the wafer weights allow this to be achieved without compromising the two side lockers and large central compartment with drop-down door.
Most front boxes can be fitted with removable swath rollers and have several neat optional extras such as heated sink units, drawers and a fold-down vice.
Another popular tractor accessory is a set of adjustable link-arm mounted mudguards, which prevent trailed implements getting plastered with mud.
Though similar in concept to some competitors, they are fitted with proper spray reducing material, rather than smooth rubber.
In addition to storage box swath rollers, George has a dedicated front linkage-mounted version that can be fitted with string, net or wrap holders, as well as a road lighting kit.
Grain pushers are also available in a wide range of beam lengths and blade widths.
All have replaceable blade wear strips made from recycled plastic and they can be fitted with brackets to suit any headstock.
Cultivation kit
Ground engaging equipment is another forte, with conversion work carried out on existing machines alongside a growing number of George’s own creations.
One of these is a close-coupled wheel track eradicator fitted with hydraulic lifting JJ Metcalfe NG legs that only pushes the implement back by 25cm.
This is available in multiple track widths and has a removable centre section so that a pto can pass through.
A range of front presses is also in the offing, all of which have a heavy-duty construction to make sure they last.
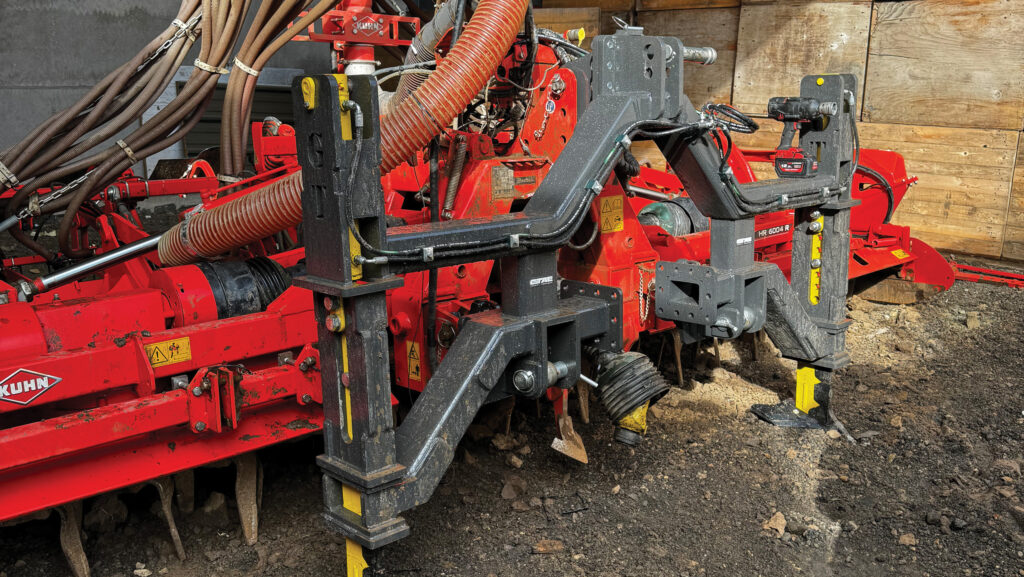
GT’s close-coupled wheel track eradicators carry JJ Metcalfe’s NG legs © James Andrews
These range in size from 3m rigid to 6m folding, all of which have the option of front tines and levelling paddles.
Each is fitted with a neat steering system that means they turn with the tractor during work, but lock solid when lifted to prevent them swinging around.
Other soil-working equipment includes a spring tine seed-bed harrow, a nine-leg, 5.4m trailed subsoiler and a six-row ridge press.
This has a series of pneumatic tyres that helps seal up cracks in the ridges after topping to prevent potatoes going green.
More implements are in the design phase and could be added to the line-up in the next few years.
“I’d like to get to the stage where we’ve got a wide range of cultivation equipment on offer,” says George.
“The only problem is that there’s a lot of expensive metal in them, so it might take a little time to build this up.”
James Silk
J Silk Agricultural Co, Hemel Hempstead, Hertfordshire
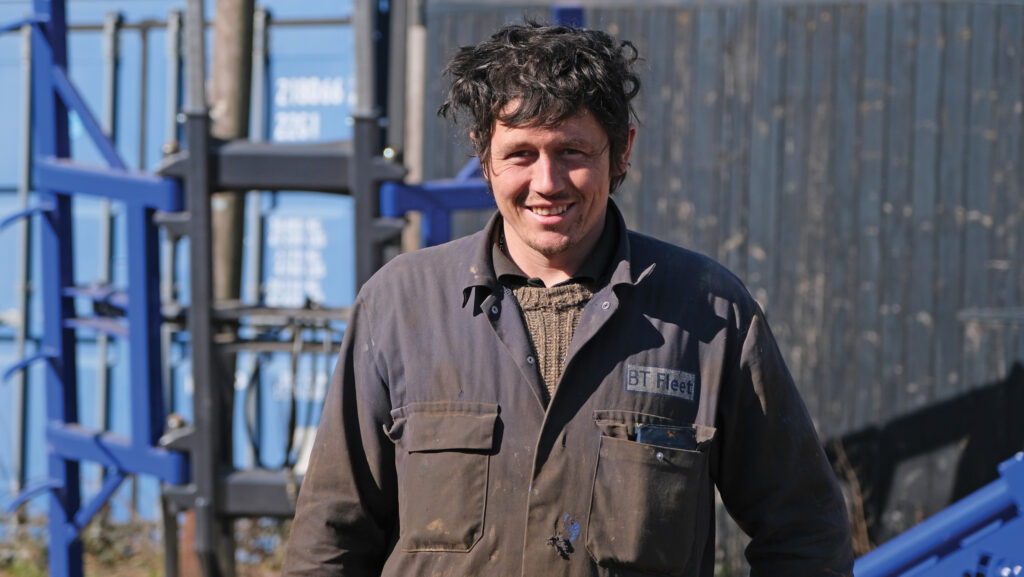
James Silk © James Andrews
After launching a small agricultural contracting business in his teens, James Silk soon realised that the key to making it pay was by building and mending his own equipment.
He took to the fabrication work like the proverbial duck to water and, as word of his welding prowess spread, it wasn’t long before he was taking on projects for other people, working out of a shipping container in his dad’s garden.
An agricultural engineering degree from Harper Adams came next, where he was able to hone his skills and get up to speed with CAD design, before properly launching into engineering and fabrication full time.
A decade later, he employs a team of six at his base near Hemel Hempstead, Hertfordshire, and builds a raft of equipment both for his own brand, J Silk Agricultural Co, and a host of other manufacturers.
“It’s basically a hobby that got out of hand,” says James.
Although he does some bespoke projects, he’s geared the business towards making machinery in volume.
This means he produces sizeable batches of products such as grain pushers, bale grabs, mole ploughs and buckets, which helps keep costs down.
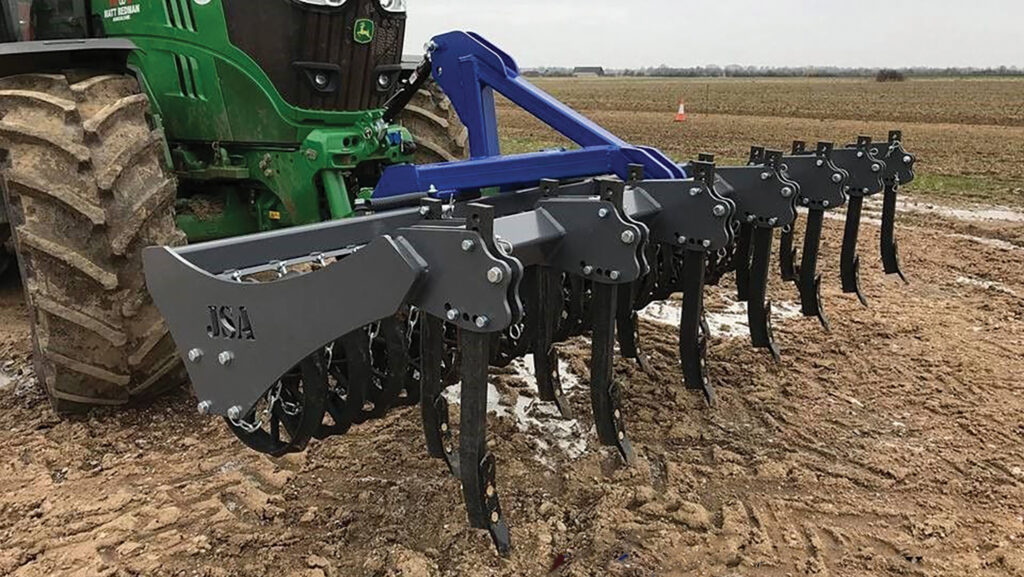
Front presses are one of several soil-working implements built in the workshop © James Silk
Most of these are his own design and are sold in his colour scheme, although some are sold by other manufacturers in their own livery.
Popular machines are kept in stock, but the amount of storage space required for this means he’s currently only able to have select items available to pick up immediately – the rest are built to order.
This won’t be the case for long as he’s moving to a larger purpose-built production facility with plenty of room for storing a broad range of kit.
In addition, he fabricates equipment for some big-name brands using their own designs, many of which require him to sign non-disclosure agreements (NDAs).
His workshop is geared to suit, with a plasma/oxy-acetylene table for cutting sheet materials, a band saw for processing box section and a hefty 4m/150t press brake for bending profiles.
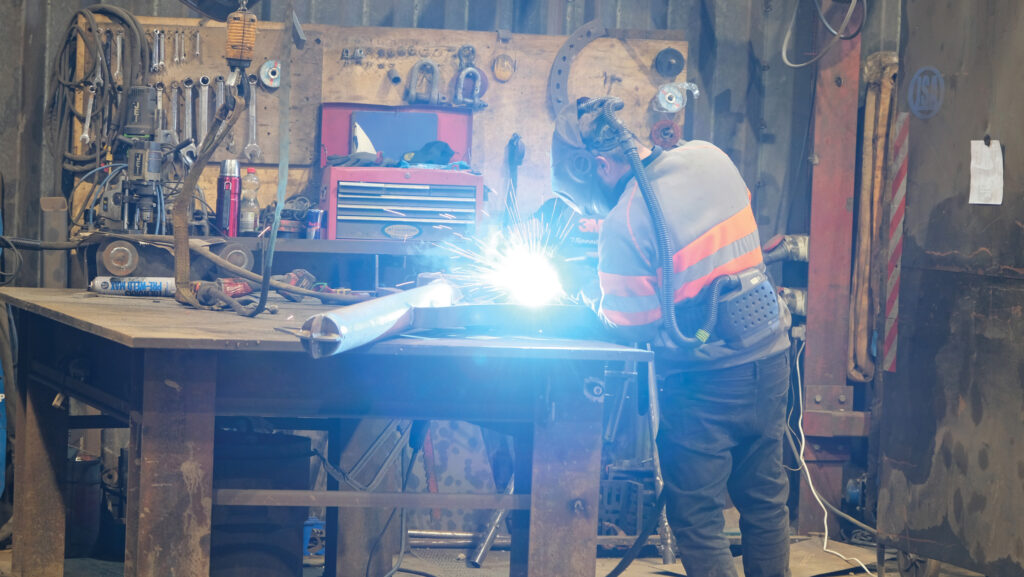
Welding burden will be eased with a new robot machine © James Andrews
There’s also a large CNC milling machine for accurately shaping and boring holes in material, a CNC twin spindle lathe and a computerised vertical storage system to give rapid access to parts during assembly.
“You just type in the code for the machine you’re building and it will rotate until it gets to the shelf with all the relevant parts – it’s saved a huge amount of time,” he says.
He’s also invested just over £300,000 in a robot welder to help fulfil a new contract.
“It’s a big risk for us but will double production capacity in a very compact footprint.”
Paint is applied in-house using a durable 2K polyurethane product that’s guaranteed for 20 years.
Handler and excavator attachments
Of some 100 items on James’s website, single-tube grain pushers are one of the biggest sellers.
Available in lengths from 2.5 to 18m, they come with a range of headstocks and are fitted with a durable, hard rubber blade edge.
Other handler attachments include buckets, grabs, bale spikes and bag lifters with two or three prongs, plus a model that offers hydraulic width adjustment.
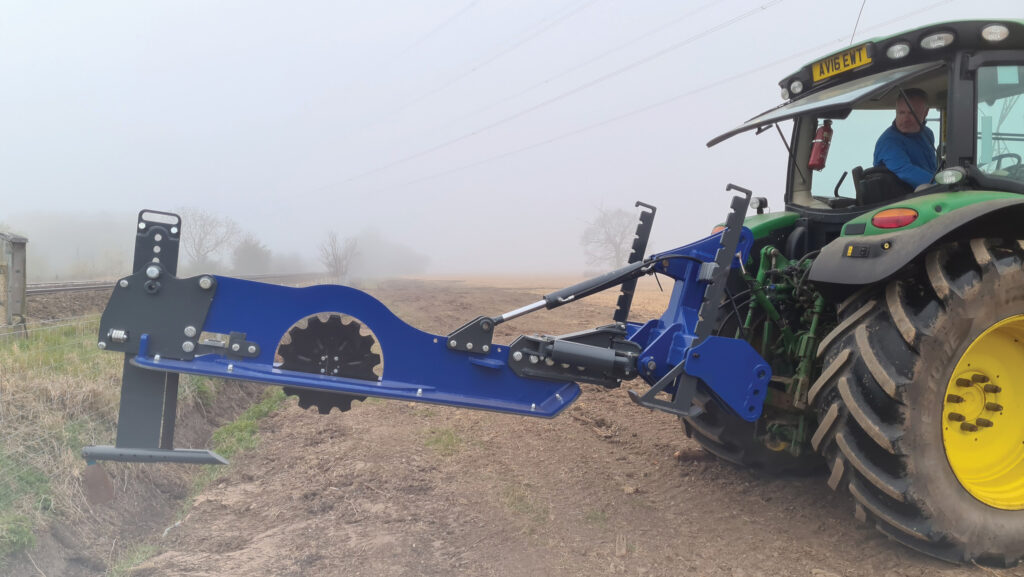
Linkage-mounted mole plough has a twin-axis pivot © James Andrews
Excavators are equally well served, with all the regular soil shifting attachments plus log grabs, land rakes, grading beams and compaction wheels.
He also offers a post knocker suitable for machines of 3t or more, which comes with the option of hammers from 150 to 400kg.
Like all his designs, James uses finite element analysis in Solidworks software to get the right balance of strength and lightness.
He also uses Hardox steel at most of the main wear points to increase longevity.
Subsoilers and presses
More involved builds include an array of cultivators, such as grassland subsoilers with cutting discs and a flat roller, and a low-disturbance model with a packer roller.
The former is available in several configurations, from a single-leg, 1.2m machine to 3m version with five legs, and all have discs with five-stage depth adjustment.
As for the low-disturbance models, these can be fitted with any brand of wearing metal, although JJ Metcalfe NG legs are the most common.
Leg protection is provided by shear-tabs. They come with a toothed packer roller and have a mounting point for a small seed applicator.
Mole plough
Then there’s his three-point linkage trailing beam mole plough, which is designed to both follow contours and reduce the amount of surface soil disturbance.
A twin axis pivot allows it to pull around gentle curves and it’s fitted with a 560mm notched disc to cut through trash, preventing it hooking around the leg.
This is protected with a simple shear tab and comes with a series of shims for adjusting the working angle.
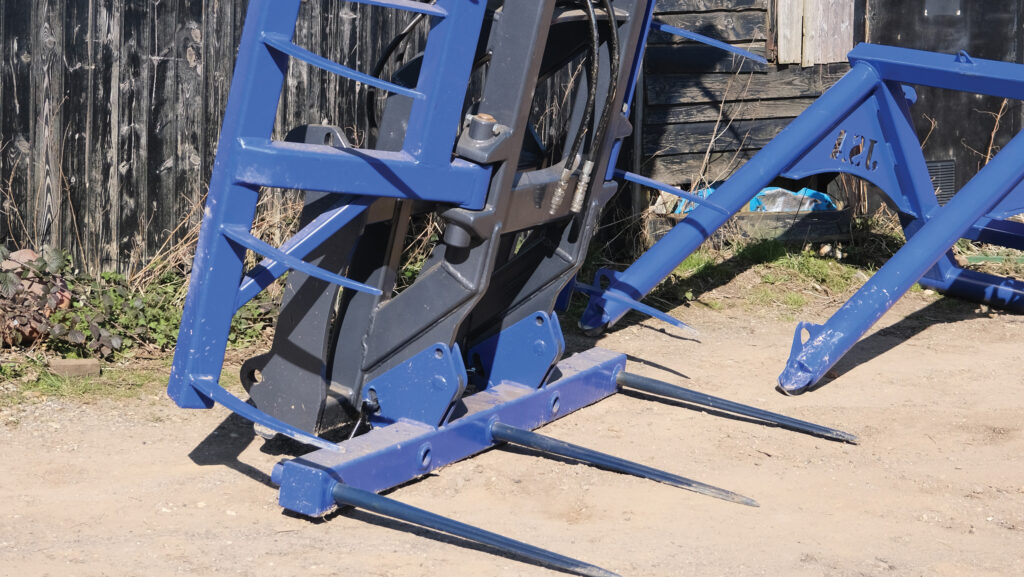
This big bale grab is one of umpteen handler attachments © James Andrews
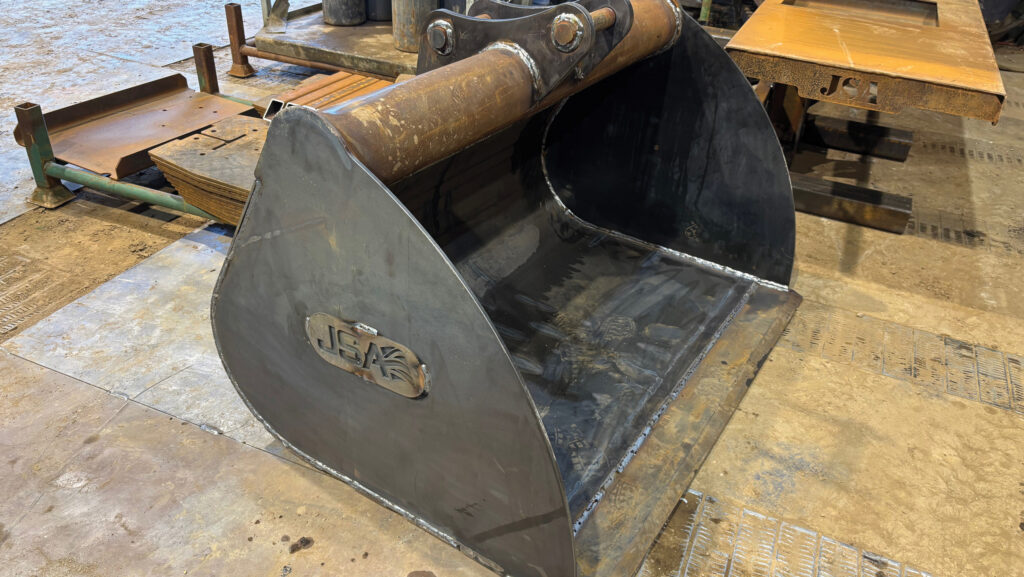
And excavators are also accounted for with buckets, grabs and rakes © James Andrews
A ram attached to the headstock allows the mole to reach the desired working depth in the shortest possible time, as well as allowing it to be drawn out gently at the other end to reduce soil disturbance.
Either 85mm of 100mm expanders are available to suit different conditions and it comes with a full-length Hardox skid plate to protect the beam.
Though he has to devote more of his time to design work and running the business these days, James is still very involved with the manufacturing process.
“I keep my hand in on most of the machines, which helps me make our processes more efficient and means I can step in if someone is off sick.”