Farmers build ultra-accurate GPS system on a budget
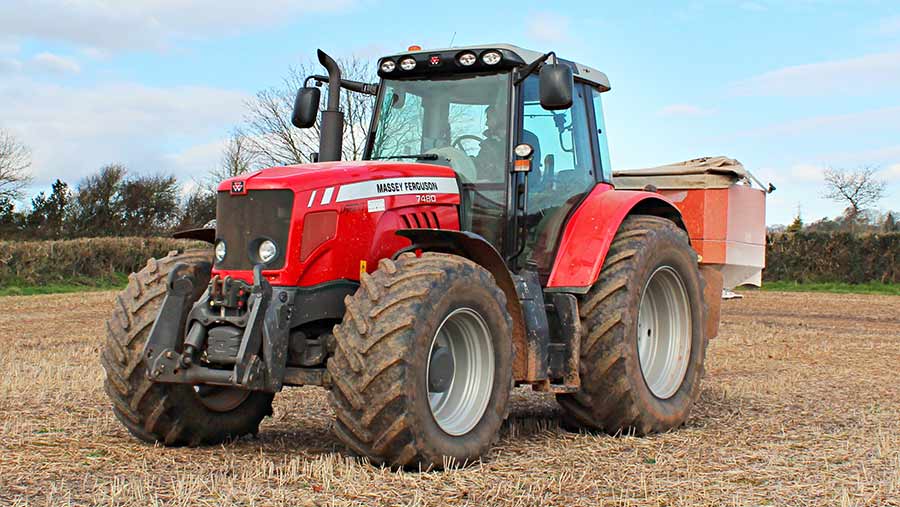
Increasing numbers of farmers are turning to GPS systems to help improve the accuracy of their field operations and make life easier for the operator.
But although prices are beginning to drop for some more basic systems, the cost of getting a machine set up for full auto-steer can still be eye-wateringly high.
Added to that, there are usually fees to pay if you want to unlock certain features and annual subscriptions for the most accurate correction signals, which are crucial for jobs such as drilling.
See also: 6 budget GPS guidance system options for farmers
However, there are a number of farmers across the globe that are cutting out the middleman by developing their own systems.
In several cases, their starting point is a piece of open-source software called AgOpenGPS, which was set up by Canadian farmer Brian Tischler.
The fact that this is “open-source” means it is free for anyone to use and modify as they wish. And crucially, any successful changes they make can be submitted to improve the way it works.
For the less technical, there are also some marginally simpler-to-use, paid-for systems such as the Spanish-made Cerea software, MachineryGuide from Hungary and EFarmer from the Netherlands.
At their most basic, all these programmes can be loaded on to a tablet computer, connected to a simple GPS receiver, and their integrated lightbar can be used to help the driver steer more accurately.
But with a bit of know-how (quite a bit in some cases) they can be adapted to run a full auto-steer system with an RTK correction that is accurate to a couple of centimetres.
Two such enterprising individuals are Somerset farmer’s son Charles Quick and Austrian farmer Andreas Ortner.
Both have used software such as this to get their tractors running on full auto-steer with RTK accuracy, but each has taken a slightly different approach. Here’s how they set about it.
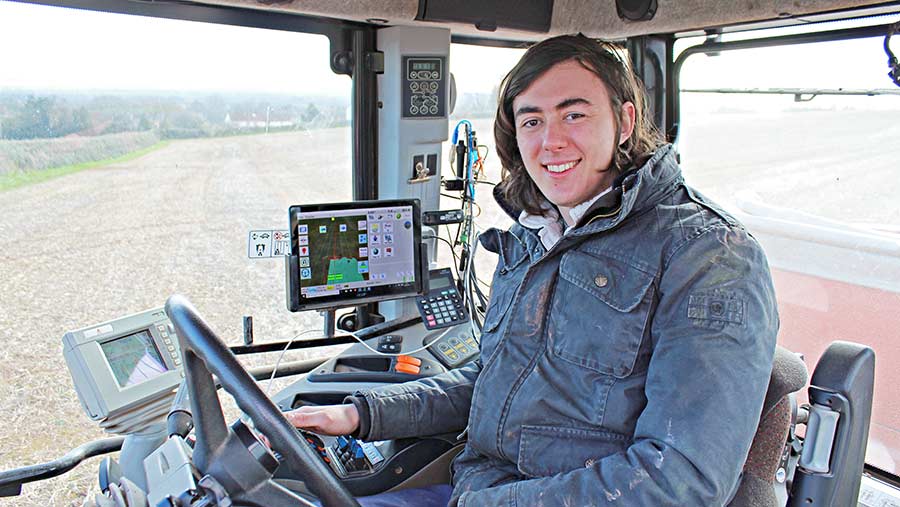
Charles Quick © James Andrews
Charles Quick, Keirles Farm, Thurloxton, Taunton, Somerset
While studying for his degree at Nottingham University, Charles Quick has managed to create his own very impressive auto-steer system and RTK network.
For a total outlay of £1,200, he has converted the farm’s 145hp Massey Ferguson 7480 Dyna VT (which wasn’t auto-steer ready) to guide itself without the need for any motors bolted to the steering wheel.
It will also steer to an accuracy of about 3cm, execute automatic headland turns and offer section control for implements such as the sprayer and fertiliser spreader. There are also no on-going subscription fees to make it work.
To purchase a commercial version of that setup you could be looking at a bill of more than £10,000, plus potentially shell out several hundred pounds a year in signal subscriptions.
Mr Quick began his project early last year when he opted to take a one-year computer science course in the middle of his crop science degree.
Initially he was tasked with building computer games, which he found “fairly boring”, so he went in search of something a bit more interesting. “I prefer programming that has a use in the real world,” he says.
As he and his father Andrew had been considering investing in a GPS system for their 280ha farm near Taunton, Somerset, Charles turned his attentions to that.
By autumn he had his creation up and running and began testing it out. “I have some embarrassing lines where I used it for drilling, but I didn’t have it fully tuned,” he says.
Now that the steering sensitivity has been sorted, it performs well, with just the occasional glitch, he says.
The system itself consists of three parts: a tablet computer running the AgOpenGPS Software, an RTK system with base station and receiver, and a hydraulic steering control unit.
Describing the specifics gets a little involved, so pour yourselves a stiff drink, dear readers.
The techy bit
For the tablet, Mr Quick opted for an off-the-shelf Acer Switch Alpha 12. The open-source software was loaded on to this and the settings were adjusted to get it communicating with the rest of the setup.
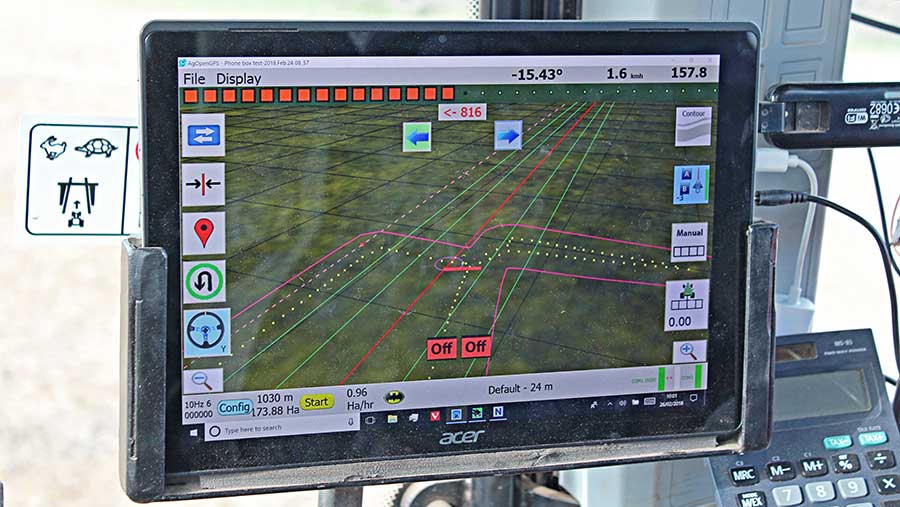
Acer tablet © James Andrews
The RTK part of the puzzle is a little more complicated. This uses a base station in the yard that he assembled himself using a cheap antenna and old drill disc, which acts as a ground plane to ensure a clean signal is received.
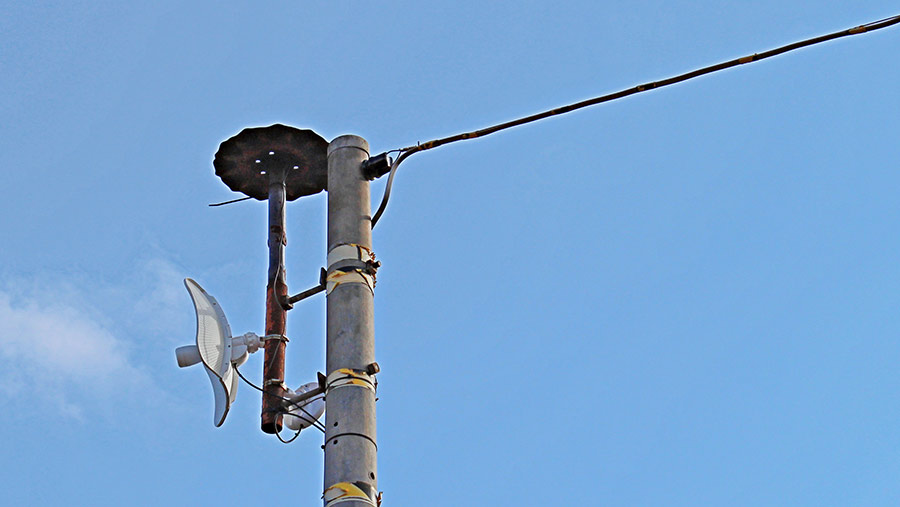
The home-made base station © James Andrews
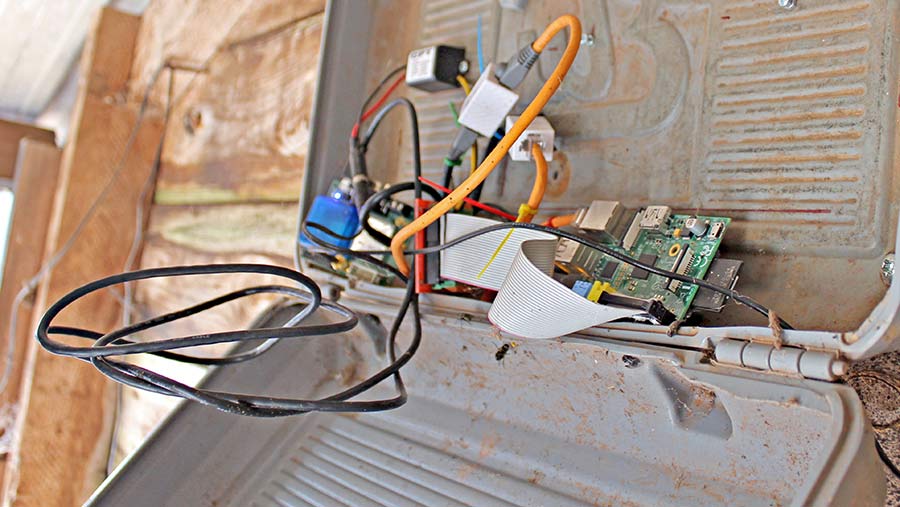
Base station © James Andrews
This is connected to a simple Ublox GPS receiver that generates an RTK correction signal, which in turn is transmitted over the internet via a mini computer known as a Raspberry Pi.
See also: How to upgrade your fleet to autosteer guidance for £20k
At the tractor end there is a Ublox GPS receiver that picks up this signal via the tablet computer’s 4G connection. This is then fed into the AgOpenGPS software and used to improve the accuracy of its positioning.
Finally, the software sends a position signal to his particularly clever home-built hydraulic steering system, which automatically turns the wheels to keep the tractor in line.
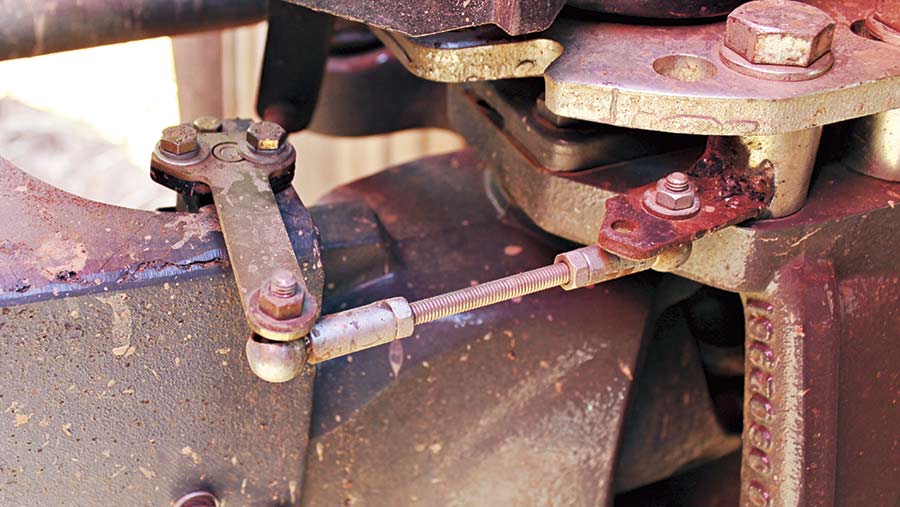
Steering angle sensor © James Andrews
Another mini computer called an Arduino forms the brains for the steering system. It’s a cheap and cheerful unit that entry-level programmers often start out on and can be picked up for about £20.
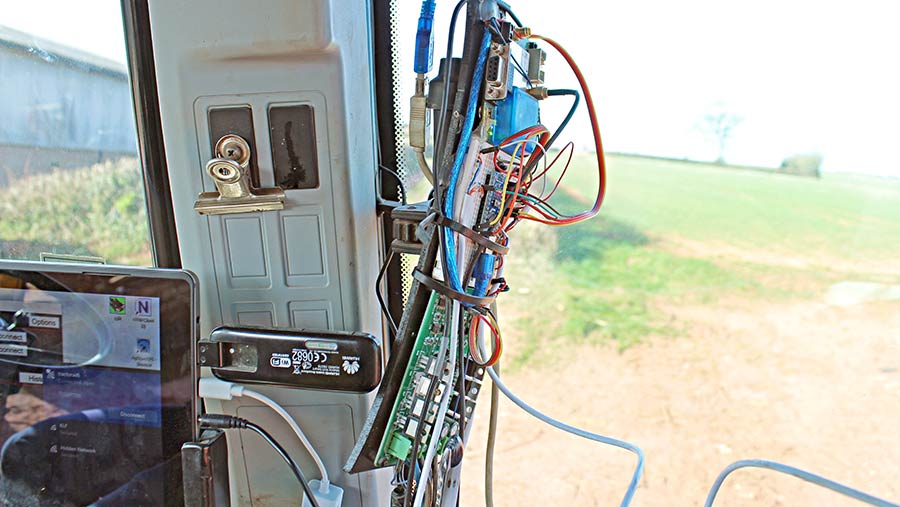
Arduino computer and GPS unit © James Andrews
The position signal, as well as readings from a steering-angle sensor on the axle and a tilt sensor in the cab, is fed into the Arduino. Mr Quick’s programming then works out where the tractor should be and sends another signal to an electro-hydraulic proportional value.
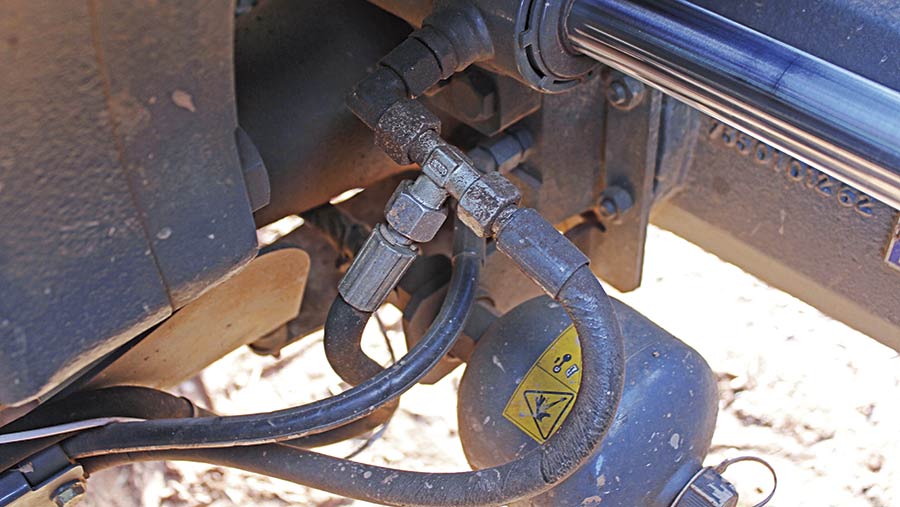
Steering ram tee © James Andrews
This is plumbed directly into the tractor’s steering circuit and when it receives the signal, pumps oil to one side of the ram or the other, thus turning the wheels in the correct direction.
The valve itself is fed from the tractor’s load-sensing hydraulic circuit and is switched on and off via a redundant switch on the tractor’s armrest.
Teething problems
As the kit is in its infancy, there have been a few niggles and bugs to iron out. This means it is a bit sensitive to being unplugged and often requires some manual input to remind it which USB each of the elements is connected to.
On the steering side, the sensitivity settings were also “a little off”, so the tractor would either over- or undercorrect. But after tweaking the settings in the AgOpenGPS software, Mr Quick was able to trim it perfectly.
Now the only glitch is the slope compensation, which is accurate to about 10cm. “I need to work on the maths to improve that,” he says.
Also, from a safety point of view the auto steering doesn’t automatically disengage when the driver grabs the steering wheel. This means it will try and pull back into line, even when the driver hauls on the wheel.
Pressing the button on the armrest completely disengages it though, and in an emergency the power lead to the hydraulic valve can also be pulled out.
This armrest button can also be used at the headland so the driver can take over and perform a turn, but the software is also capable of doing it itself.
In this semi-autonomous mode the tractor will work its way across the field without the driver having to touch the wheel or press any buttons.
What’s next?
To extend the distance his system will work over, Mr Quick is also considering upgrading his GPS transmitter and receiver.
The current Ublox L1 units generally work up to 10km from the base station, but higher-grade L2 versions will extend that to about 30km.
He is also hoping to programme the unit to perform curved A-B lines. At the moment the software will only work in straight lines, which isn’t ideal in some more awkwardly shaped fields, he says.
“I was chatting to Brian Tischler about this the other day and it turns out it’s a very tricky bit of programming – so if any of the big manufacturers would like to share that with me, I would be very grateful!”
Mr Quick is also putting a second system together that will work with the farm’s Massey Ferguson 6290.
As this tractor doesn’t have load-sensing hydraulics he plans to connect the steering valve to a spool valve, which can be set to constant pumping.
He is also considering adapting this kit so it will fit on their Lexion 630 Montana combine.
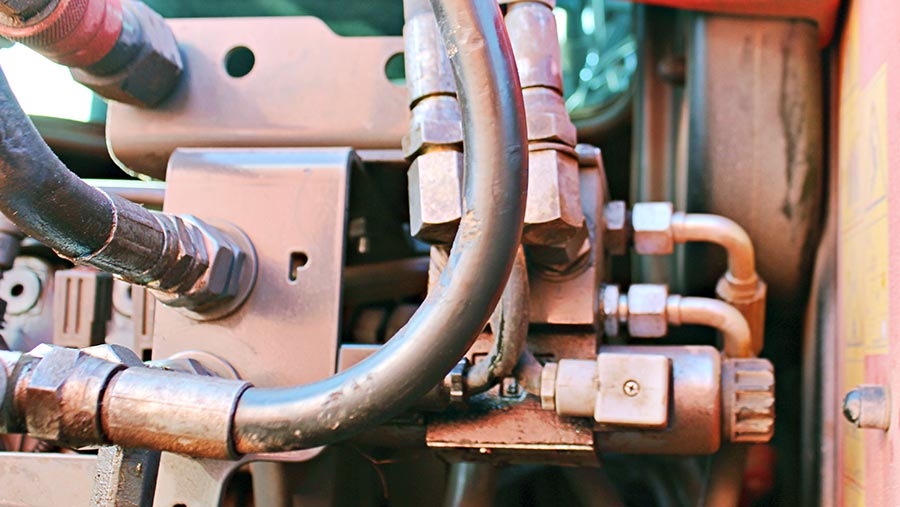
Hydraulic valve © James Andrews
Despite the success and relatively low cost of the system, Mr Quick is unsure about selling it to other farmers.
That’s partly because it would be difficult to guide them through any problems they had with it, but also that it’s not in the spirit of open-source programming.
“I didn’t have to pay for the software I started with, so when I do get it perfected I might share plans for my system so that other people can have a go.”
Andreas Ortner, Graz, Austria
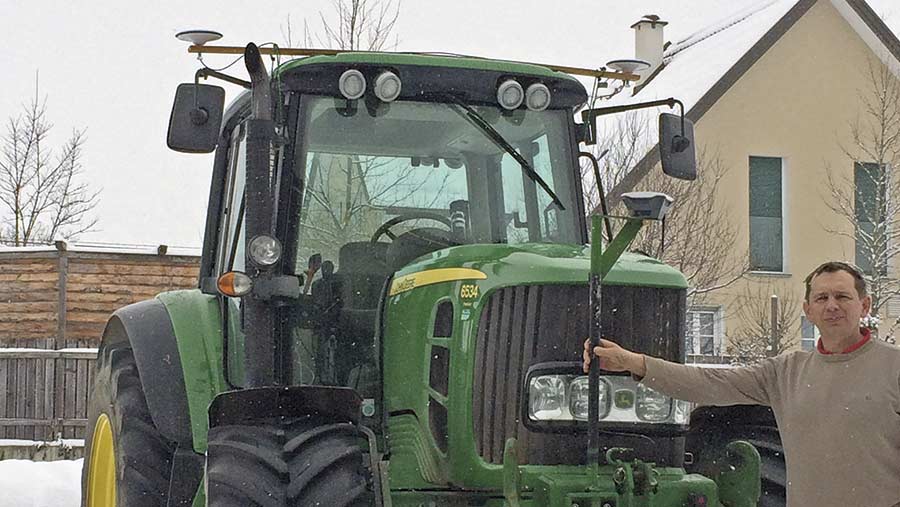
Andreas Ortner
Andreas Ortner runs a 50ha arable and pig farm near Graz in the undulating south-east Austrian state of Styria.
He grows maize, barley, wheat and sorghum, most of which is fed to his pigs, and has developed his own guidance and RTK auto-steer systems.
These are fitted to all three of his John Deere tractors, including a 180hp John Deere 7530, a 150hp 6354 and a 110hp 6320.
The 6534 and 6320 are used for fertiliser spreading, spraying and other light work and run a simple visual guidance setup.
But, his 7530 drilling tractor has a home-made full RTK auto-steer system that can work to about 2cm accuracy.
See also: 7 budget GPS guidance systems on test
Initially, all of Mr Ortner’s systems were based on a piece of off-the-shelf software called Cerea, but like Charles Quick he has been working with AgOpenGPS and is gradually switching to using that.
This software is loaded on to a series of Windows-based tablet computers, and notebooks (one for each tractor) including a Trekstor, Chuwi and Panasonic, all of which cost less than £300.
For the simple setup, this is connected to a basic GPS receiver, but for the more accurate version on the 7530 drilling tractor he needed a RTK correction signal.
This came in the form of a system called Reach, built by Russian firm Emlid. It uses a GPS base station back at the yard to send out the correction signal over the internet.
A receiver on the tractor then picks up the signal via a wi-fi hotspot, consisting of a wireless router with sim card installed in the tractor cab.
This is then fed into the tablet computer running his Cerea or AgOpenGPS guidance software using a simple USB connection.
For the auto-steer setup he has bolted the GPS receiver’s antenna on a bracket mounted off the tractor’s front linkage. This apparently provides a faster heading correction than mounting on the roof.
But for the tractors with simpler manual steering, he has positioned it on roof to provide a better sky view. It is apparently also more accurate as it is positioned closer the driver.
As for the automatic steering element on the 7530,Mr Ortner opted for a motorised system that turns the tractor’s steering wheel, rather than a more complex setup plumbed into the hydraulics.
This operates in a similar way to Trimble’s EZ-steer, but rather than buy one, he decided to make his own.
Most of the components for this were sourced from Canadian electronics specialist Phidgets, including a motor, encoder and control unit.
Once assembled, this was mounted to the steering wheel and plugged into the tablet running the Cerea or AgOpenGPS software. This then sends the steering direction signal back to the unit.
All in, the system cost less than £2,000, including about £400 for the Reach RTK kit, £150 for the Cerea software, £250 for the components to build the steering system and about £300 for each of the Windows tablets.
Emlid also offers a more sophisticated version of Reach called Reach RS. These units are self-contained, with the battery and antenna housed in a waterproof casing.
They cost a shade less than £600 and will communicate directly with a tablet running GPS software via wi-fi or bluetooth.
What’s next?
Although the current system works well and will provide steering accuracy of about 2cm, Mr Ortner is considering testing a more expensive GPS setup with dual antennas. This should provide even more accurate headings with sub-cm precision, he says.
He has also programmed an Arduino mini computer to control a relay board for automatic section control on his sprayer. This gets its commands from the Cerea software running on his windows tablet.
Mr Ortner is also working with Emlid and AgopenGPS to develop and improve their software. “It is a hobby for me and I like to help at AgOpenGPS because it is open source,” he says.
AgOpenGPS
For anyone who wants to learn more about AgOpenGPS, there are extensive conversations on the North-American Combine Forum.
Canadian farmer Brian Tischler, who is based in Mannville, Alberta, leads many of the discussions. He developed the original software and others, including Andreas Ortner, have contributed.
The programme itself is hosted in an online repository called Github and is free for anyone to download and play around with.