Getting the best from… a loader tractor
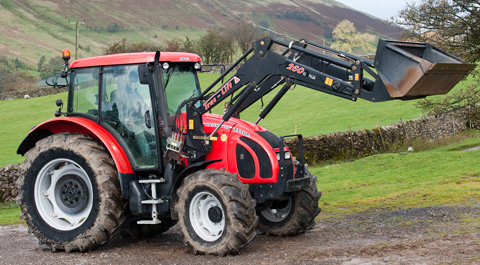
The humble loader tractor gets some stick. It runs day in day out, usually up to its axles in slurry, the cab often looks, and smells, like a silage pit and servicing is a luxury it is rarely afforded.
If a mirror drops off it usually isn’t replaced, if a tyre runs soft it’s ignored and as the tractor gradually slides into disrepair the driver learns to live with its growing list of problems. But give it a bit of TLC and the most regularly used tractor on the farm will last a lot longer and give the operator a great deal more comfort to boot.
Stuart Facer from Kirkby Stephen-based dealer Tunstall Tractors picks out ten tips for getting the best from a loader tractor.
Hydraulics
Hydraulic pipe routing is crucial for loader performance – pipes routed at acute angles will reduce oil flow making the loader slow and irritating to operate. Watch pipes carefully throughout the lift sequence to make sure they don’t become stretched or kinked at any point. Consider re-routing if they do.
Keep a close eye on hydraulic oil levels and change the filter regularly, particularly if operating in dusty environments. Slow or juddery loader performance could indicate low hydraulic oil level or a blocked filter.
Cable care
The loader joystick cable is the only link between the driver and the loader. If the plastic coating becomes scuffed, water will get into the cable causing it to rust and eventually snap. Water ingress can also cause the cable to freeze solid on cold mornings.
If the joystick becomes stiff to operate, don’t wait for tennis elbow to set in. Look for damage on the cable and replace if needed. Replacement cables cost £40 to £80 and should take no more than an hour to fit.
Greasing
Loader pivots, particularly in the headstock, will wear quickly if they are not regularly greased. Carry a grease gun on the tractor and lubricate the main pivots according to the operator’s handbook.
Choosing a loader with protected grease nipples will make the task much more bearable as broken or damaged nipples are a nightmare.
Watch out for broken pivot pins or loose bolts, usually caused by insufficient greasing, and replace immediately. If a pin comes out the loader could be irreparably damaged.
Anti-bounce kit
Fitting an anti-bounce kit to the loader hydraulics will considerably improve operator comfort and reduce strain on the loader and tractor.
Accumulator units allow the loader to move independantly, preventing the whole tractor from bouncing when carrying a load at speed.
An aftermarket unit will set you back about £350 and it’s sensible to opt for an isolation tap which locks the kit out. This stops the loader dropping if loading a heavy weight over an object you don’t want to crush.
Wheel weights
Counter-balancing a loader tractor will keep the rear wheels on the ground, improve steering and reduce tyre and front axle wear.
Wheel weights are the best option as ballast water will slosh around and if antifreeze isn’t added it will turn into an unforgiving ice block come winter. Rear weights work well, but block the three-point-linkage and hitch.
For a four cylinder tractor fitted with 1.75t loader a 100kg weight on each wheel should keep it nicely balanced.
Servicing
It goes without saying, but a well-serviced tractor will last a lot longer than one that isn’t. Make sure the oil and filter is changed every 250 hours unless the handbook says otherwise. On this Zeter Forterra 125 an oil change service should take considerably less than an hour, so put aside some time to do it.
Nice to have
Choosing a machine with a clutchless forward-reverse shuttle will save the left knee and opting for a tractor with a glass sunroof will dramatically improve loader visibility at height. Tractors with fans mounted in the roof can obscure the loader when it’s at full extension.
Painting hooks on all loader attachments in a bright colour, or even better with fluorescent paint, makes implement changes considerably faster, particularly in a dark shed corner. A hydraulic latch is an added bonus meaning the operator needn’t leave the seat. Retro-fit kits are available.
A front bull bar is a worthwhile investment as it protects vulnerable and expensive headlights as well as the bonnet. It also makes the front of the tractor visible from the cab, which is useful when edging up to objects.
Tyre pressure
Keep an eye on tyre pressures – front tyres should generally be inflated to 30psi on a loader tractor. Running a soft tyre will damage the sidewalls, increase wear and make steering heavy.
Front axle
Adding a loader increases front axle loading and puts more strain on pivot points. Frequent turning under load also accelerates wear. Axle pivots and king pins should be greased twice as often as they would be on a non-loader tractor.
Silage wrap
If silage or net wrap is left on it yard it can build up around the trumpet housing. If left, it eventually works its way into axle seals causing them to fail and leak oil. Replacement requires a full axle strip-down, so keep axles free from debris and try not to leave net wrap lying around.