Getting your grainstore logistics right
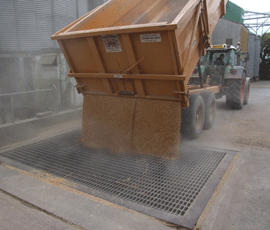
Just like traffic on a busy road, grain entering or leaving a grain store is forced to run at the speed of the slowest component – a large lorry on the road or the smallest auger in the store.
Matching flow rates to ensure every part is working at its optimum output can be a constant challenge as farms become larger, combine output increases, and trailers get bigger.
Sadly, there’s no easy or inexpensive solution. If an existing grain store has a two-inch auger and a washing up bowl for the trailers to tip in to, then it’s unlikely the elevators and conveyors that follow will also have much in the way of spare capacity – so there’s little point digging a large receiving pit and emptying it with a 60t/hour auger.
Present and future needs
![]() |
---|
Making the most of a building’s storage capacity using a levelling conveyor. Always check wall loadings. |
The key question is: where do you set the handling capacity of a grain store – and ensure with some certainty that a complete refurbishment, possibly with the addition of a new drier, is not going to have to be repeated five years later, or less?
According to David Perry managing director of grain handling equipment manufacturer, Perry of Oakley, the starting point when considering flow rate capacities is the rate at which grain is harvested – and is likely to be in the future.
“Farms are becoming ever larger and, with them, comes bigger combines to cope with the increased acreage,” he says. “It follows that the amount of grain being delivered to the store is going to be considerably greater than it was perhaps only a few years ago and the chances are that it will increase again.”
Mr Perry says the secret is to build extra capacity into a system from the start. If, for example, the daily intake during harvest is 300t/day, the aim should be for it to be all dried within a 10-hour period, which means that a 30t/hr drier needs to be installed.
“This provides extra capacity for future expansion and also extra time to dry more heat-sensitive crops such as malting barley or oilseed rape,” he explains.
Conveying problems
Having settled on a suitable drier capacity, the grain handling equipment – the reception pit, the cleaner, the elevators and the conveyors – need to have their capacities assessed and, as a general rule, these would need to be about twice the size of the drier capacity.
This extra capacity is provision for times when the grain is harvested very nearly dry and can be passed though the drier at high speed. So, with our example of a 30t/hr drier, other equipment needs to be geared to 60t/hr.
![]() |
---|
Grain drier capacity needs to match combine capacity – the general rule is that 300 tonnes a day into store requires a 30 tonnes per hour drier. |
As any combine driver will tell you, one of the more infuriating sides of the job is to have a full grain tank and no trailer available to empty it in to. Fast tipping is essential and a large pit capable of holding a trailer load of grain is a real consideration providing it has a 60t/hr conveyor to empty it and, as a result, allow other trailers to tip in quick succession.
Run-over grids
“An alternative is a pit with a run-over grid which has above ground space for a number of trailers to tip their loads and create a large wet storage buffer over the pit,” says Mr Perry. “This allows fast tipping of trailers and also means that driers can continue to work unattended into the night if required.”
Continuous flow driers, of course, need to be kept full of grain and this requires an excess of grain to be fed to the drier, with the surplus being returned to the pit.
“The use of wet grain storage bins is becoming less and less,” he says. “And if you think about it, there is little point storing wet grain due to the drier’s inability to cope with the volume because, the very next day, there’s likely to be a similar amount to dry – and the situation just gets worse.”
Once the grain has been dried it has to be stored and, bearing in mind the high yields this harvest has recorded, space could be at a premium.
![]() |
---|
Conveyors and elevators should have capacities which are about twice that of the drier to allow sufficient grain flow on the occasions when grain is harvested at low moisture levels and its speed through the drier is high. |
One way of exploiting the full capacity of an on-floor store is to have a top conveyor filling system and a levelling cross conveyor. Available as a manually controlled or automatic system, the levelling conveyor spreads the grain to an even, pre-set depth, before moving on a small distance for a repeat performance. It is important not to exceed wall loadings which could lead to the collapse of a grain store.
Loading out
When the day comes to load out and lorries turn up to take the grain away, most will expect to be loaded and sheeted within an hour of arriving. The days of shovelling grain into a 4in auger, which manages to dribble a few tonnes/hour over the back of a lorry have now hopefully past.
Instead, it is the roll of the loader and bucket which provides the speed and the loading capacity – as long as the operator doesn’t damage the cross bars in the lorry’s trailer.
“Fixed grain-handling equipment is not cheap,” concludes Mr Perry. “But when you consider the value of the grain it is coping with and the costs that could be incurred if it isn’t in place, it’s not perhaps too expensive.
“The key point when installing a system is to get it right from the start and allow plenty of capacity for future expansion.”
Grain Event UK
Looking to improve your grainstore? Drier on its last legs? Wondering about central storage? The best place to find answers to these and other grainstore questions is at this year’s UK Grain Event at the East of England Showground on 2 November.
Seminars
10.30: Growing for a specific market
Richard Whitlock, grain marketing consultant
11.30: Central storage and marketing
Rob Sanderson – Head of central storage network, Openfield
12.30 When will the bubble burst?
Jack Watts – Senior analyst, cereals and oilseeds AHDB Market Intelligence
1.30: How to control energy costs
Andrew Kneeshaw – FEC Services
2.30: How to comply with crop assurance codes
UK grain details
When: Wed 2 November 2011 9am to 4pm
Where: East of England Showground, Peterborough PE2 6XE
Cost: ÂŁ15/person on the door or ÂŁ10/person in advance
Tickets and further information: Go to www.farm-smart.co.uk or ring 0845 4900 142
Exhibitors
ACP (Concrete) | Farmex | Openfield |
Agricultural Supply Service | Farm-Tec | Opico |
Agri-Shop | Flach & Le-Roy | Perry of Oakley |
Allmet | FrigorTec | Pro-Therm Controls |
Alvan Blanch | GFT | Robinson Agriculture |
Astwell Augers | GlassGuard | Safety Revolution |
BDC Systems | GrainTek | Satake Europe |
Bentall Rowlands | Griffith Elder | Schenck Process |
Buhler | Hardcastle Ventacrop | Scorpion Engineering Construction |
Buhler Schmidt Seeger | Harvest Installations | Simpson and Allinson |
Calor Gas | Huntsmoor Park Farm | Sinar Technology |
Carier | Kentra Grain Systems | Tey Farm Systems |
Challow Products | Kongskilde | T H White Installation |
Chief Industries | Lodi | Tornum AB |
Cimbria Unigrain | Martin Lishman | Tripp Batt |
Concept Grain Systems | Master Farm Services | Tryac |
Danagri-3S | M.D.Anthony | Welvent |
Dan-Corn | Mecmar Driers | Whites Concrete |
Devizes Control Systems | Milbury Systems | Z-Tech Control Systems |
Emmerson Doors | Octagon Products/Robydome |