Speed is all when it comes to clearing straw
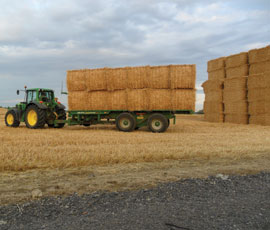
Each year, Charlie Rand buys enough straw to make more 80,000 large square bales, which he stacks and sells to power stations, mushroom composters, horsefeed manufacturers and livestock farmers. He also exports straw to processors in Ireland and mainland Europe who remove the dust so that it can be used for horse bedding.
Based at Hatch Pen Farm, Royston, Hertfordshire, Mr Rand started his straw business 13 years ago with one baler and a Ritchie Traileyre bale chaser – a combination which he says served him well but was soon lacking in capacity.
“Over the years the business has grown to the point that we now run seven New Holland BB9090 square balers, four bale chasers and three JCB telescopic loaders,” he says. “The 200hp tractors we use with the balers and chasers are all hired in for the season.”
Straw is purchased in the swath from arable farms throughout Hertfordshire, Cambridgeshire, Suffolk, Essex and Bedfordshire and a normal year will see him baling upwards of 12,000ha. However, 2012 saw larger-than-average straw yields that reduced this to nearer 10,000ha.
“If you learn anything in the straw business it’s that farmers do not like to see bales in a field,” he says. “They are always keen to get on with cultivations and bales can be a major problem so it’s important not only to have the right machines to make the bales but also to cart them off the field quickly. Delay too long and you can forget about having straw next year.”
“It’s important not only to have the right machines to make the bales but also to cart them off the field quickly. Delay too long and you can forget about having straw next year”
Charlie Rand
Mr Rand concedes that having seven balers is probably one too many for the scale of his operation but points out that there is a two-week period, usually in mid-August, when all combines are at work and the demand for baling reaches a peak.
“We could probably cope with fewer balers before this time because not all the heavy-land growers will be harvesting cereals, and also after this time because the light land growers are starting to finish harvest,” he explains. “But just for two weeks in mid-August everyone’s at it and we need the baling capacity to cope.”
Chasers
Mr Rand runs two Arcusin and two Heath chasers, all shod on wide tyres, which scoot around the fields picking up and stacking bales on to their trailers before transporting them back to the stack for unloading.
The two Heath machines arrived first about two years ago and, like the Arcusin, can stack and carry 12 big square bales on each trip. The Arcusin’s mode of operation is rather different, though, and requires the tractor driver to nudge the bale through 90deg so that it is side-on to the front of the trailer running in an offset position.
The bale is then secured by a two-tined fork, which lifts it up and over on to the trailer bed. A second bale is lifted on top of it and the pair is shunted towards the rear of the platform to make room for the next pair.
When completed, the load is driven back to the stack and tipped vertically to leave the stack six bales high – the top four having an extra push back to lip over the previous stack and bind them in.
Slightly faster
We don’t sheet the bales. I estimate we lose about 16% of the straw through rain damage but even these bales can be sold for composting
Charlie Rand
“I think the Heath is a slightly faster system but it calls for greater operator skill to get it right,” he says. “If the bale is not pushed round in the field properly the tines do not meet it in the same position as the previous bale and the stack is not straight as a result.”
He adds that there are also occasions when brittle straw, damaged by a combine’s rotary threshing system, prevents the tines from supporting the bale and the tines rip through and out of the bale.
This is not a problem for the Arcusin chasers though which have been with him for about a year. These machines pick up bales on an elevator before turning them through 90deg so they can lie square on the platform. Two bales are loaded and then lifted vertically to form the first pair of a two-high stack, which is added to until there are 12 bales on board.
“It’s entirely automatic and the operator just has to drive,” he says. “At the stack, the platform is tipped vertically and the bales released.”
There is one important difference between the Heath and the Arcusin and that is that the latter can leave bales stacked on their strings in the main store – a detail which does not sit well with Mr Rand who prefers bales to be stacked on their sides. He points out that the bale width created by the bale chamber is constant and the stack is always more uniform as a result.
To solve this problem, bales produced for the Arcusin to handle are deflected on to their sides – the bales chute is only half width so the bales topple over as they leave the baler.
Mr Rand aims to create a series of stacks at local sites that are level, well drained and have access for lorries. To reduce surface area and wastage through weathering, a JCB telehandler is used to restack them to a height of eight bales.
“We don’t sheet the bales – there isn’t usually enough time and they tend to blow off or become ripped – I estimate we lose about 16% of the straw through rain damage but even these bales can be sold for composting,” he explains.
His largest customer is Ely power station, which takes about 70% of the straw and collects loads on a weekly basis – using a three-bale grab, it’s a 10-minute job to load a lorry.
Keep up with the latest machinery news