Grassland UK: Alternative rakes can speed the job
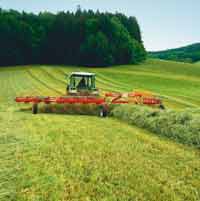
There is, as they say, more than one way to crack an egg. And in the field of hay and silage making there is certainly more than one way of bringing spread grass into a neat and tidy swath ready for baling or chopping.
A pto-powered single- or twin-rotor rake – or a quad-rotor rake in the case of big contractor operators – is the most common method. But Italian firm Tonutti reckons there is still life in the finger wheel design that once dominated the scene (remember the Lely-Vicon Acrobat)?
Tonutti’s machines work in much the same manner – a series of upright finger wheels rotate in contact with the crop and pass it from one wheel to the next.
Things have changed in terms of scale, however. The company still produces a modest six-wheel side rake, but the main focus is on the bigger centre-delivery machines, which can have as many as 20 finger wheels in total spanning 12m (40ft).
“Simplicity and sheer output are the greatest attributes of these implements,” says Paul Allen of Tonutti’s UK importer Sunshine Agriculture. “They will work at twice the rate of a conventional twin- or quad-rotor rake, cost half as much and have maybe four times the life.”
The lack of pto drive-shafts, gearboxes and tine-lifting cam mechanisms means there is little to go wrong and the modern finger-wheel rake is robust enough to cope with a heavy workload and lush crops, he adds.
“We’ve done several thousand acres with our demonstrator and haven’t needed any of the spares we took into stock,” says Mr Allen.
Critics of the finger-wheel rake of old will point to a tendency to roll forage like a rope and bring soil and other debris into the crop.
“Like any rake design, the finger-wheel mechanism needs to be set up and operated correctly, then the likelihood of either of those problems occurring is remote,” says Paul Allen. “If you get the height and spring loading of the wheels just right, these machines are no more likely to bring up debris than a rotary rake that is properly set up. And “roping” will only be problem if the operator tries to produce a really huge windrow.”
In fact, he maintains the way the crop is passed from one finger wheel to the next – rather than being dragged along the ground by the vertical tines of a rotor – is gentler on the crop.
At least one test report supports that view: In a comparison set up by one of France’s regional co-operative federations, a 6.5m twin-rotor rake worked alongside a 13-wheel 8.5m Tonutti side rake in a crop of lucerne was reckoned to cause twice as much leaf loss early in the day when conditions were ideal and eight times as much later in the day.
No difference was found in terms of crop contamination with stones or soil, the report adds. But the side rake working at 17kph (10.5mph) achieved twice the work rate – 8ha/hr (20 acres/hr) – as the twin-rotor machine operated at 12kph (7.5mph).
Add to that an ability to happily work at 24kmh to 26kmh (15mph to 16mph) and it is evident there is a lot of capacity potential in the machines.
“And, of course, there is the flexibility to work at different widths, depending on the weight of crop, to produce the most appropriate size of swath for following machinery,” says Paul Allen.
The UK working debut of one of Tonutti’s biggest implements, the 12m (40ft) Millennium V20 7GW, at last year’s grassland event attracted plenty of attention. But Mr Allen concedes that the smaller models will suit most potential users here.
The Raptor V14, with a working width of 7.8m (25ft 6in) and priced at about ÂŁ9700 has the build to suit farm users, while the heavier-duty Dominator V14 covering up to 8.5m (28ft 4in) comes in at about ÂŁ17,500.
This model also benefits from being fitted with self-steering rear wheels to help turn into gateways and hydraulically-lifted finger wheels which move the grass from the centre line before replacing it with the new windrow.
“We also like to include plastic windshields on all the finger wheels to cope with windy conditions and prevent very short material passing between the spokes,” adds Mr Allen.
Kent contractor goes for output
Versatility is the key attraction to David Quinn and his son Stewart of an alternative form of twin-rotor rake.
The Fella TS1402 trailed implement they operate can gather 12m (40ft) of crop into a single windrow with two passes, put 6m (20ft) into one windrow with a single pass, or leave two small windrows in its wake, each containing about 3m (9ft 10in) of grass.
The latter option is ideal for the 100ha (250 acres) of grass cut for hay and packaged in small bales each year as part of the Quinn Farm Services business they run near Ashford in Kent.
“We used a Haybob-type machine to rake up the grass before and it just couldn’t keep ahead of the balers,” says Stewart Quinn. “With this machine, we’re effectively operating two 3m single-rotor rakes, getting twice the output and have no problem matching the balers for output.”
The Fella rake has two pto-driven rotors, each carrying 10 or 12 tine arms, depending on the model chosen. But instead of being side-by-side, the rotors are arranged in a staggered formation, with the right-hand rotor (looking from behind) set further back on the square-section backbone chassis.
A delayed-reaction hydraulic lift mechanism ensures the rear rotor finishes off the windrow before lifting for a headland turn.
“When you pull the hydraulic control lever, the front rotor arm lifts and there’s a cam that regulates the flow of oil to the rear arm,” says Stewart Quinn. “It’s adjustable, so you can set the delay according to your forward speed to get the rear rotor to lift at the right time.”
The rake is used in the two-swath configuration for most of its workload, with the rotors positioned far enough apart that the grass they gather is left in a pair of windrows of the ideal size for the Quinn’s two John Deere 459 conventional balers.
But when called on to rake up grass for a big baler or forage harvester, changing the arrangement involved nothing more than repositioning a locating rod on the rotors.
“Each rotor is suspended from its supporting arm by a sort of parallel linkage arrangement, which is connected to the chassis by this rod,” says Paul Quinn. “With the rotors in the transport position, you relocate the rod to a different position and when the rotors are lowered they are pulled in closer.”
That is enough for the grass gathered by the front rotor to be collected by the rear one and moved across to leave a single swath. By driving back up the field alongside the swath just laid, it is possible to put 12m (40ft) of material into a single windrow, a technique used effectively last year to deal with some damp straw on neighbouring farms.
“In grass, you have to be a bit careful with your speed, especially if conditions are a bit damp, to get a consistent and even swath,” says Stewart Quinn. “Particularly if it’s for a round baler; it’s not so important for a self-propelled forage harvester.”
GRASSLAND UK |
---|